Precision extrusion: aluminium extrusion profiles without concessions
Mifa specializes in the production of complex aluminium and magnesium profiles with dimensional tolerances starting from +/- 0.02 mm.
What is precision extrusion?
Precision extrusion is a manufacturing process in which material is pressed through a die with great accuracy to create complex shapes with precise tolerances – here at Mifa we start from ± 0.02 mm.
For several decades, Mifa has been the benchmark in the B2B market when it comes to aluminium extrusion components. We are focused on customizing an extrusion profile to optimize and process it into a high-quality end product, and are specialized in extruding complex aluminium and magnesium profiles. We often manage to produce these aluminium and magnesium profiles completely in-house, serving various markets.
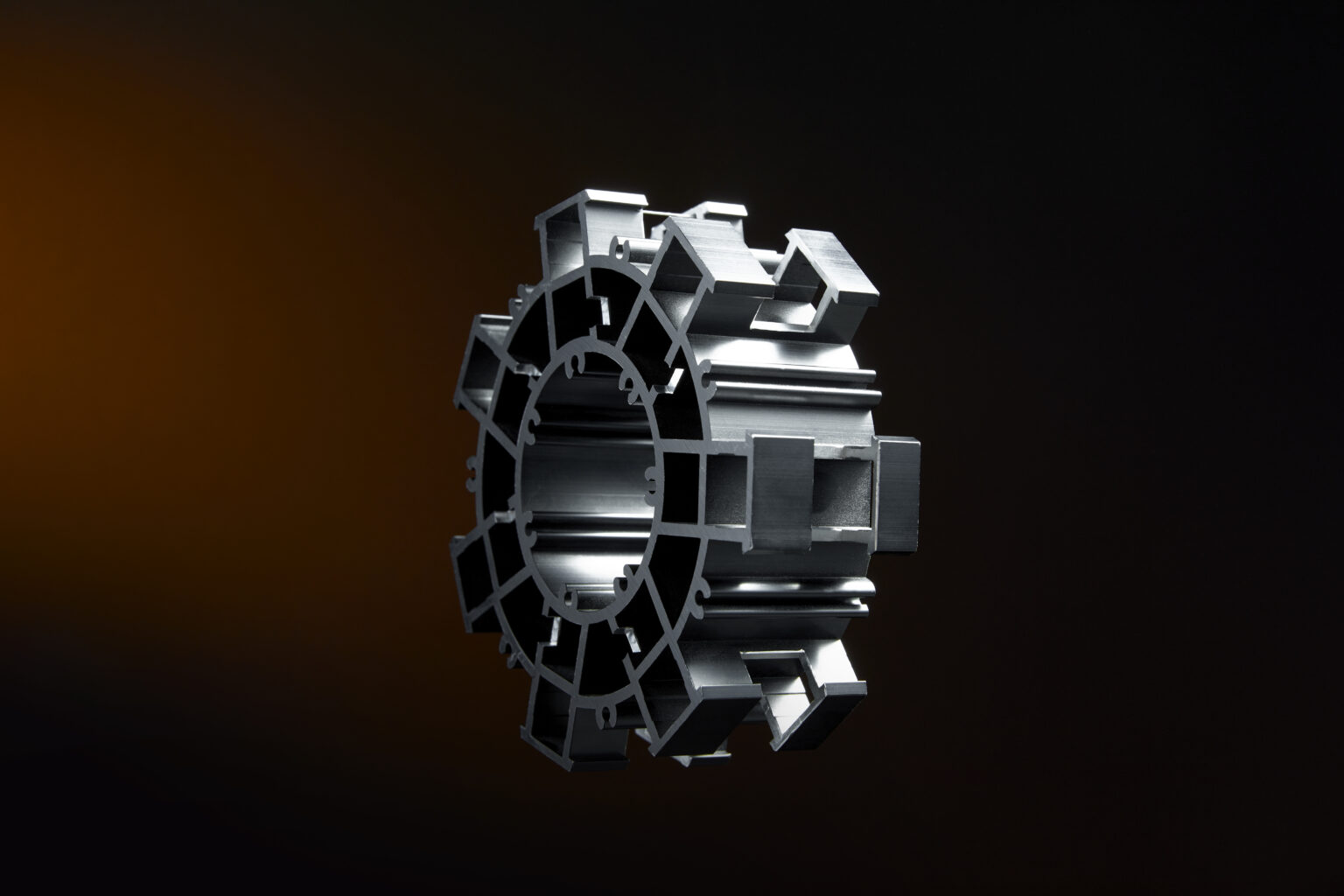
Precision extrusion at Mifa
Our aluminium and magnesium profiles are utilised in various products destined for different markets, including the industrial market, aircraft and aviation industry, mobility market, and the medical market. Each market and every company has specific requirements in the development and production of magnesium and aluminium extrusions.
Many manufacturers extrude standard profiles. However, at Mifa, we go further. Mifa focuses on manufacturing complex, tailor-made aluminium and magnesium profiles.
It is our high standard for quality, precision, and design freedom that sets us apart from the competition.
What are the advantages of extrusion at Mifa?
Mifa is known for its expertise in extruding aluminium and magnesium with extreme precision and attention to detail. That’s why Mifa produces parts like medical precision components. Our extrusion processes are focused on achieving optimal accuracy.
Mifa’s aluminium profiles surpass the standard through properties such as straightness, torsion, concentricity, parallelism, surface roughness and precision; with dimensional tolerances as low as +/- 0.02 mm.
Our profiles can be processed in flexible quantities, in-house, through a process from extrusion to surface treatment. This allows us to take full responsibility of the production process and deliver the best possible end result to our customers.
We can also extrude starting from as little as 10 kg, which is suitable for both prototypes and small production runs. For higher volumes, we can set up full production lines, including post-processing such as CNC machining, surface treatments, and assembly. This benefits in ways such as faster development and testing phase, cost savings, design improvement and process optimisation.
Contact us for more information
Tolerances from ± 0.02 mm
Wall thicknesses from 0.25 mm: substantial weight savings
Profile weight from 0.003 kg/m to 10 kg/m
Profile dimensions from ø 3 mm up to ø 180 mm / 220 x 60 mm
Avoid/reduce costly machining (post) processing steps
Vertical integration: all processes can be realised in-house
Mifa's extrusion process: from aluminium billet to extrusion profile
What does an extrusion process look like?
The extrusion of aluminium is a process in which an aluminium billet is heated in an oven until it becomes soft enough to be deformed. This aluminium extrusion process involves different temperatures, depending on the alloy, which significantly influences the end result.
The complete extrusion process consists of the following steps:
- Extrusion billets are cut to size.
- Preheated to ca. 450°C and placed into the extrusion ram.
- The container slides into place, holding the billet.
- The ram pushes the billet through the extrusion die.
- The profile gets cooled and cut to size on the run out table.
- The profile get stretched and stretch ends get cut off.
- Profiles are collected and receive a final heat treatment.
Custom aluminum extrusion profiles; our engineers collaborate with you
In precision aluminium extrusion, customization takes center stage. Advanced technology and precise dimensional tolerances offer unprecedented design freedom. Our engineers can design custom aluminium extrusion profiles without having to compromise and with minimal constraints on standard norms.
Some specifications:
Tolerances | From ± 0.02 mm |
Minimum order | From 10 kg for protos |
Maximum quantity | Unlimited |
Profile size | From ø 3 mm to ø 180 mm 220 x 60 mm |
Profile weight | From 0.003 kg/m to 10kg/m |
Surface roughness | From Ra 0.3 in extrusion direction |
Wall thicknesses | From 0.25 mm |
More information?
We offer a wide selection of whitepapers on various techniques. They are written by our experts and delve deeper into the specifications of each technique. Our whitepapers are free to download!
Multi-core profiles
Extruding small cores requires a high degree of precision. Thanks to the years of knowledge and experience of our engineers, Mifa can create cores that are sometimes no larger than 0.5 mm.
Normally, cores are added afterward, but we can also integrate them into the profile by pressing them from a single piece, without the need for drilling. Co-extruding a profile, instead of drilling it afterward, offers several advantages:
- Precision: It is at least as precise as drilling afterward and requires less work since no machining or assembly is needed. This shortens production time.
- Finish: The finish is perfect, and the profile is easy to keep clean because there are no assembly seams.
- Cost Savings: Compared to (deep hole) drilling, it is often cheaper and more precise. This is a significant advantage, especially for machines in the food industry. Although the extrusion costs are higher due to the cores, the total production and process costs for the final product will be lower.
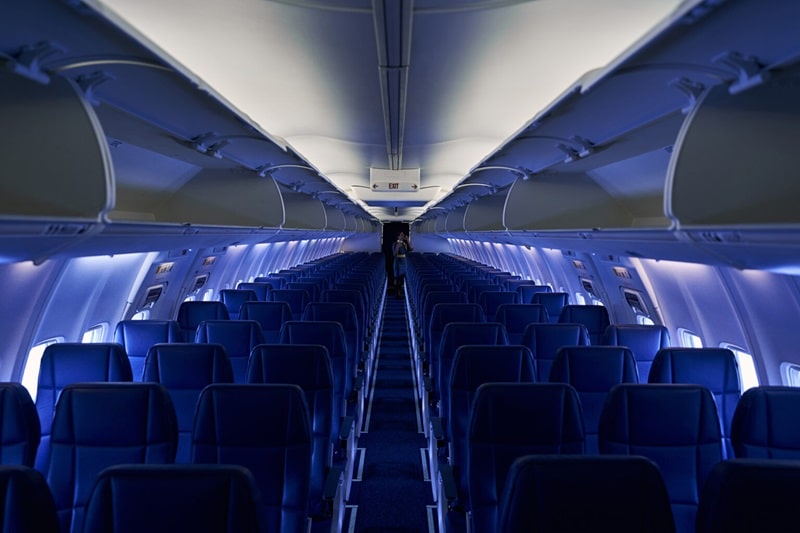
Demanding markets
Mifa specialises in the production of high-quality profiles for demanding markets such as the aircraft and aerospace industries.
We produce for customers such as Airbus and Collins Aerospace. For these profiles, we offer an extensive range of techniques. In cooperation with our customers in the aerospace industry, we develop extrusion profiles and parts for, among others:
- Instrument panels;
- Lighting systems;
- Radar components;
- Luggage compartments.
As an additional service, we also focus on customers’ cosmetic requirements. For this, we have special processes to meet the aesthetic requirements of profiles and ensure their consistency. Besides aviation, Mifa focuses on other markets, including industry and mobility.
Co-engineering: cooperation leads to the best result
Co-engineering is the joint development of a product through multidisciplinary collaboration starting from the design phase.
Mifa is an involved partner throughout our customers’ projects, which has allowed us to build successful collaborations. Our support in the design process allows us to advise our customers on a high quality aluminium or magnesium alloy. Consulting our engineers on time will result in a refined profile, component or product.
- We have experience in various market segments;
- Together, we achieve the optimum result;
- Shorter time-to-market;
- Lower costs thanks to efficient design;
- All responsibility lies with one company.
Contact our engineers
Vertical integration: all technologies in house
Mifa can manage the entire process: development, production, and finishing of aluminum extrusion profiles. We have all the necessary techniques for the entire product process in-house, where our sustainable entrepreneurship is applied at every stage.
Vertical integration within Mifa provides the following benefits:
- Single point of contact;
- A fully finished precision product;
- Control and knowledge throughout the entire chain;
- Cost savings;
- Shorter total production time.
Precision extrusion
With dimensional tolerances as low as +/- 0.02 mm, we go beyond the norm for complex aluminium and magnesium extrusion profiles.
Machining
In a modern machine park with more than 30 CNC machines, we perform all machining operations on aluminium and magnesium profiles.
From prototype to series production: flexible quantities
A prototype is an initial model of an extruded profile designed to test its design and functionality. Customers often opt for a prototype first to verify the design and functionality before proceeding with large-scale production.
Prototypes offer significant advantages on the path to series production. With a low starting threshold, the entry barrier for production is also relatively low. This allows for the rapid development and testing of an initial version of a product. This version enables us to implement design and functional specifications early on, saving time and costs in later production phases. Developing prototypes also provides the opportunity to refine and optimize the design before beginning series production.
At Mifa, we can extrude starting from as little as 10 kg, which is suitable for both prototypes and small production runs. For higher volumes, we can set up full production lines, including post-processing such as CNC machining, surface treatments, and assembly. All of this takes place entirely under one roof, ensuring a streamlined and efficient production process.
The benefits of prototypes summarized:
- Faster development and testing phase
- Cost savings
- Design improvement
- Process optimisation
From a minimum quantity of >10 kg per order to an endless maximum for series production.
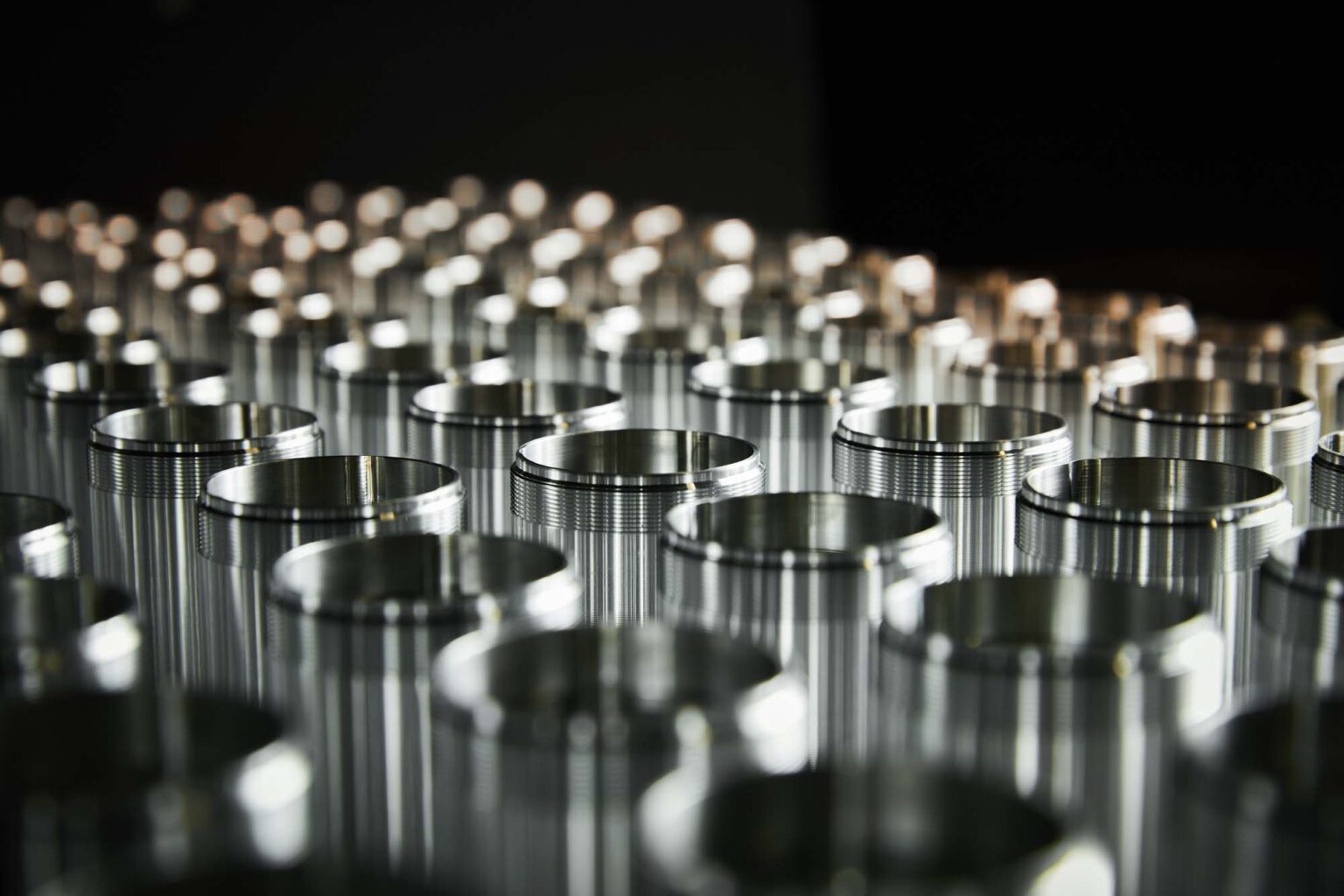
Wide range of alloys
Mifa offers a wide range of aluminium and magnesium alloys. Each alloy has its own characteristics that must be considered when choosing the right one for a specific application. These include factors such as heat resistance, corrosion resistance, mechanical strength, ductility, formability, and weldability. As standard, we provide alloys in the 1xxx, 3xxx, 6xxx, and 7xxx series. Additionaly, we also offer specific aerospace alloys.
Together towards net zero emissions
Aluminium has a long lifespan and remains 95% recyclable after use. It requires minimal maintenance, but at Mifa, we go even further. We continually consider energy consumption, waste management, vitality, safety, and the health of our employees. Specifically, Mifa has achieved the following performances:
- Mifa saves 78% emissions with in-house production compared to others.
- With full in-house production, Mifa saves a significant amount of CO2, a common ecological culprit: transportation.
- Mifa’s thin-walled profiles result in a material saving of 33%.
Sustainability is a crucial theme in developing new products. We understand that questions arise about the CO2 emissions associated with the production of aluminium profiles at Mifa. Alongside our partners and engineers, we’ve developed a specialized tool for life cycle analysis (LCA). This tool calculates emissions and demonstrates the positive impact of co-engineering on reducing the CO2 footprint.
Innovative extrusion profiles for 3D printer of Rapid Shape
Innovative extrusion profiles for 3D printer of Rapid Shape
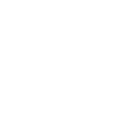
High performance cosmetic requirements in aerospace
High performance cosmetic requirements in aerospace
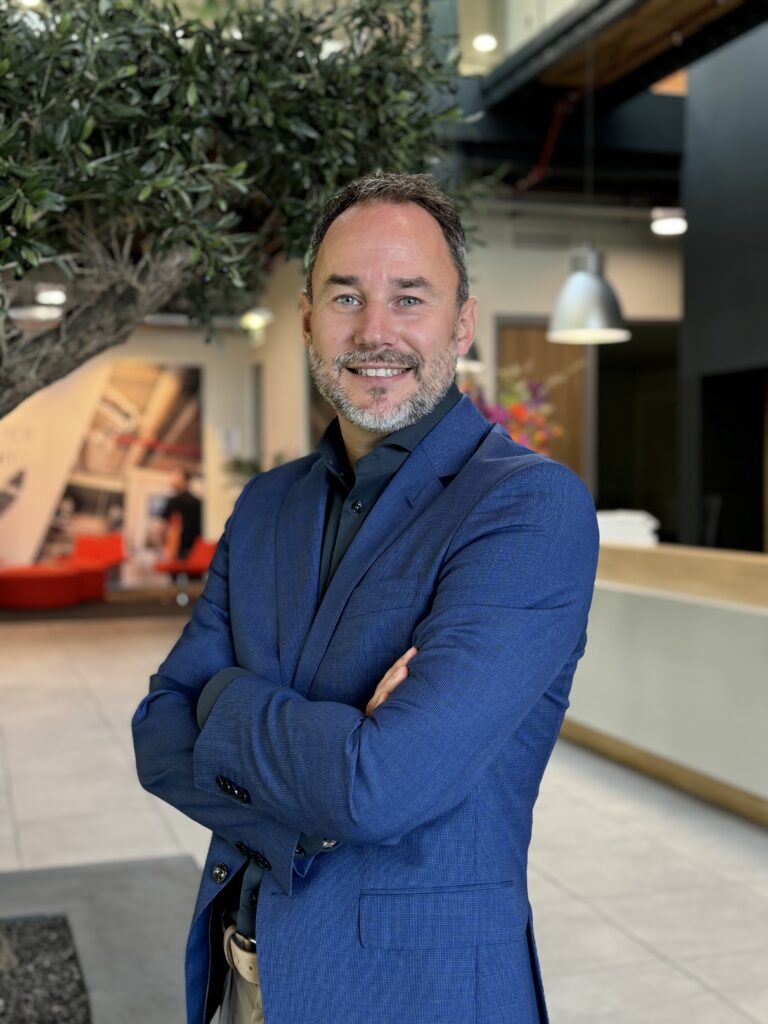