Co-engineering: working together towards the optimal outcome
At Mifa, co-engineering results in the highest quality, sustainability, and an optimal end product.
Co-engineering at Mifa: sustainable solutions in every step of the proces
Selecting the appropriate aluminium alloy, thinner wall thicknesses, saving CO2-emissions: some of the many choices our engineers can help you with. Customers have the freedom to submit their own designs, however, we also encourage collaboration through co-engineering. This partnership can result in a product with enhanced effiency, quality and refinement. In summary, these are the benefits of co-engineering at Mifa:
- A refined profile or component
- Optimal results
- Faster time-to-market
- Lower costs for an efficient design
- Single-party responsbility
As a leading aluminium precision extrusion company, with 50 years of experience in various markets, we can offer sustainable, cost effective, solutions in every step of the proces:
Precision extrusion
With dimensional tolerances as low as +/- 0.02 mm, we go beyond the norm for complex aluminium and magnesium extrusion profiles.
Machining
In a modern machine park with more than 30 CNC machines, we perform all machining operations on aluminium and magnesium profiles.
Co-engineer with our experts during a masterclass!
We offer masterclasses on precision extrusion – Rely on the power of precision – during which our experts tell you more about the specifics of Mifa’s techniques. The program of the masterclass consists of knowledge sessions in the field of aluminium precision extrusion, the extrusion process, and surface treatments. Sustainability is also covered, as it currently plays a crucial role in our production process, and we would like to assist you in improving your ecological footprint.
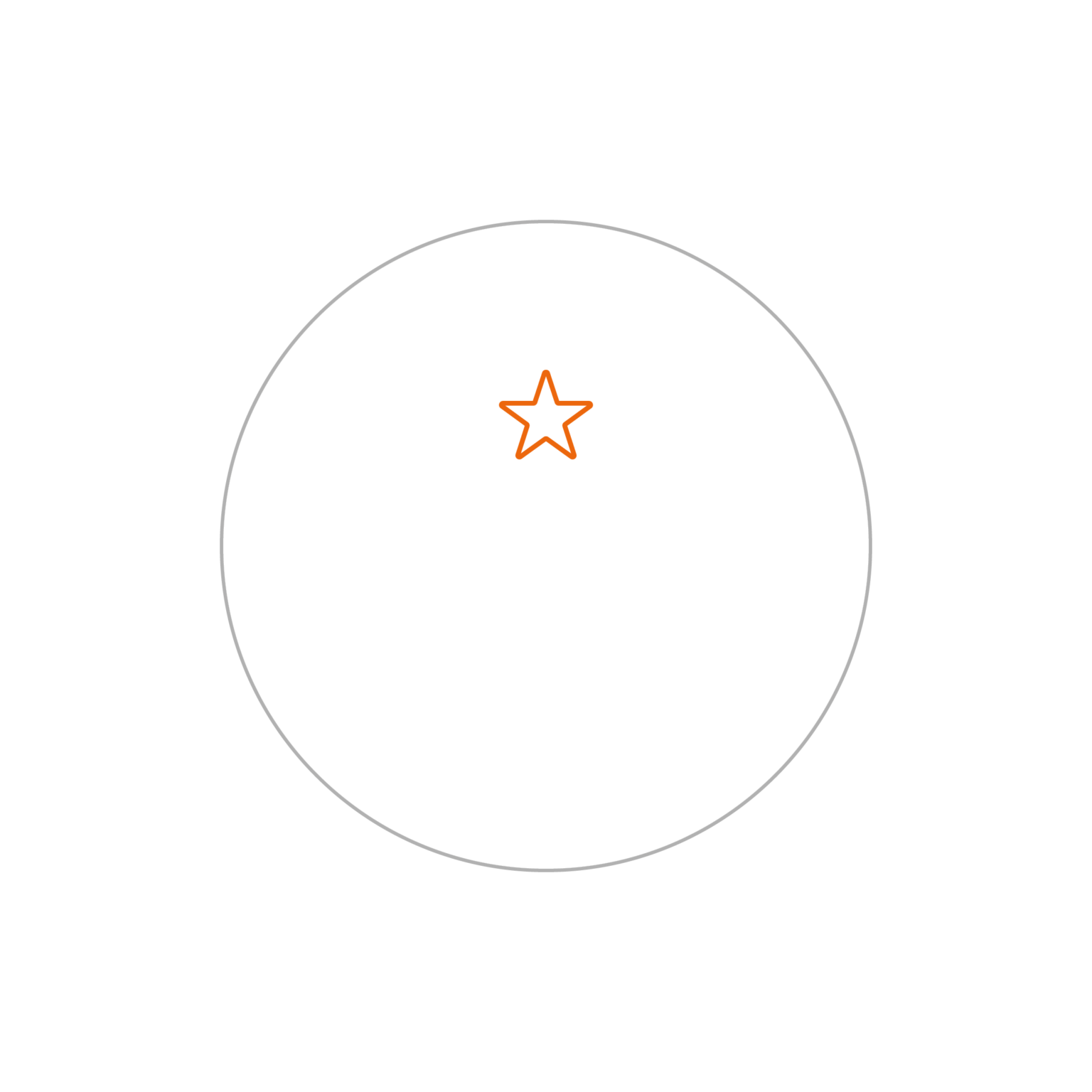