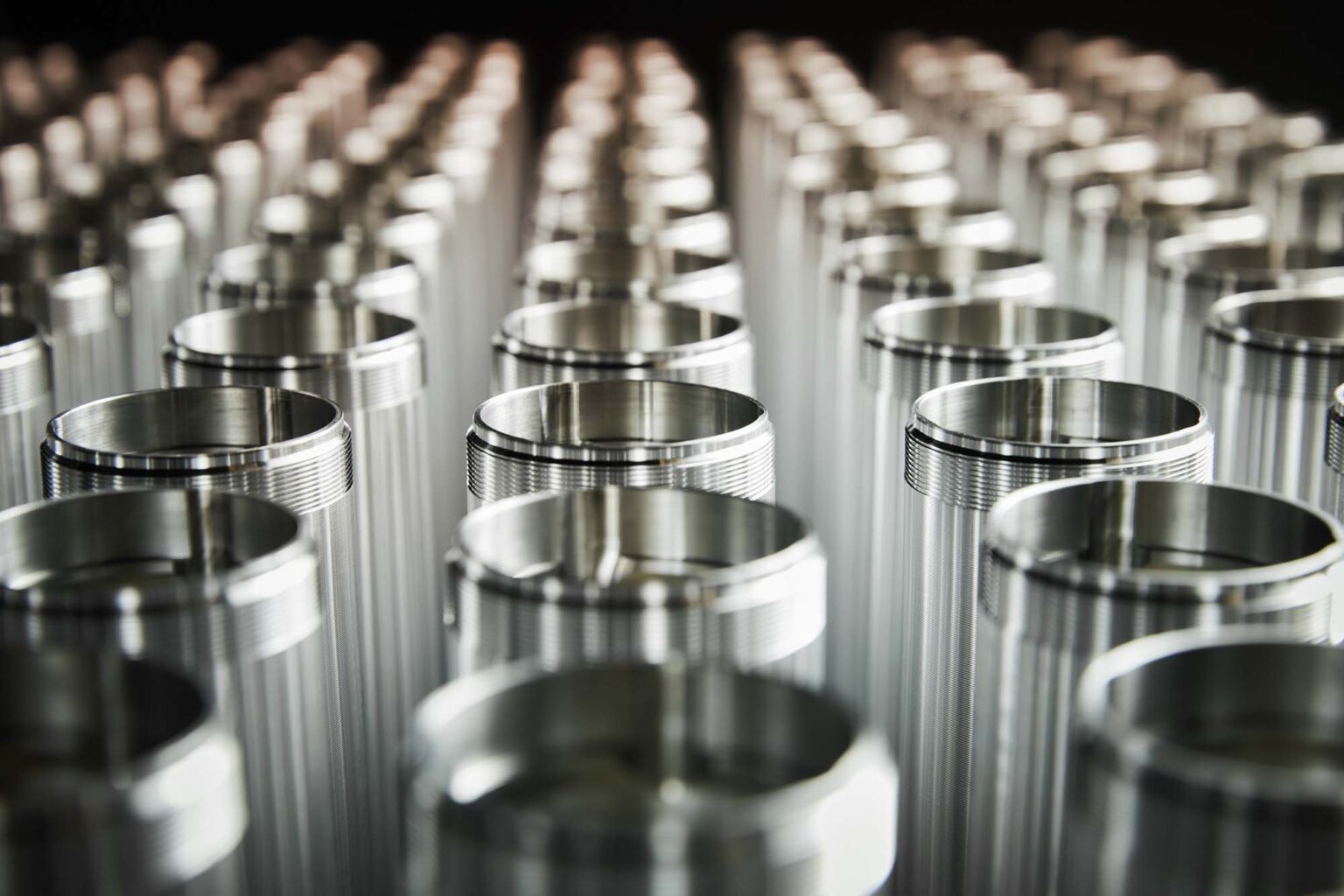
The aluminum alloy that best suits your product
The right aluminum or magnesium alloy for your precision profile; the optimal end product starts with the right choice of material.
Aluminum and magnesium alloys
Aluminium and magnesium alloys are lightweight, strong metal mixtures that are frequently used in the aerospace, automotive, and construction industries due to their high strength and corrosion resistance.
Mifa specialises in producing precision extrusion profiles made from aluminium and magnesium. We possess the expertise and experience to select the appropriate alloy for each product. As such, we supply profiles to a variety of sectors, including industry, aerospace, the medical sector, mobility, and defence. In each market, properties such as material strength and wear resistance are crucial factors in choosing the right aluminium alloy. On this page, you can read about the characteristics of all the alloys we offer.
Key factors in choosing an alloy
Alloys, composed of various metals and other elements, exhibit different characteristics that are crucial for the final application. It is therefore of great importance that the aluminium or magnesium alloy offers the right properties, as they withstand external temperatures, humidity, or chemical conditions to varying degrees. The following factors play a role in selecting the appropriate alloy:
- Heat resistance
- Corrosion resistance
- Mechanical strength
- Ductility/elongation
- Formability
- Weldability
The advantages of co-engineering at Mifa
Mifa’s engineers have the expertise and knowledge to advise you on the various types of aluminium and magnesium alloys, so that together we can create an optimal product. Additionally, we combine our knowledge of metal alloys with our expertise in extrusion. Co-engineering offers the following benefits:
We are pleased to advise you on the most suitable alloy
Faster development and testing phase
Cost savings
Design improvement
Process optimisation
-
EN AW 1070
The 1070 alloy is the only variant from this series that Mifa stocks as standard. Due to its excellent electrical conductivity, it is an almost automatic choice for many electronic applications.
- Strength: low
- Formability: good – excellent
- Corrosion resistance: good
- Weldability: fair
- Surface finish: good
-
EN AW 3003
Due to the addition of manganese, this alloy is 20% stronger than the 1xxx series. It is primarily used in the automotive industry for manufacturing radiators.
- Strength: moderate
- Formability: excellent
- Corrosion resistance: good
- Weldability: good
- Surface finish: good
-
EN AW 6060
The 6060 aluminium alloy is one of the most commonly used mixtures when strength is not the decisive factor. It offers excellent formability, a very good surface finish, and is suitable for most surface treatments. Moreover, it is easily weldable. The 6060 alloy can, in fact, be used almost anywhere but is often chosen when the product is visible, such as interior elements in aircraft, industrial applications, and so forth.
- Strength: moderate
- Formability: good
- Corrosion resistance: good
- Weldability: good
- Surface finish: good
-
EN AW 6063
The 6063 aluminium alloy is almost identical to the previously described 6060 alloy, but due to a higher magnesium content, the 6063 alloy exhibits better mechanical properties than the 6060 alloy.
- Strength: moderate
- Formability: good
- Corrosion resistance: good
- Weldability: good
- Surface finish: good
-
EN AW 6005A
-
EN AW 6061
The 6061 alloy is commonly used in the United States. It has excellent mechanical properties but compromises somewhat on surface finish and is more difficult to extrude than other 6xxx variants. It has a higher strength than many other 6xxx variants, with strength lying between that of the 6005 and 6082 alloys.
- Strength: moderate
- Formability: good
- Corrosion resistance: good
- Weldability: good
- Surface finish: moderate
-
EN AW 6082
The 6082 alloy has very good mechanical properties and is stronger than other variants in the 6xxx series. However, due to the difficulty in extruding it, it is not widely used for complex profiles.
- Strength: moderate to good
- Formability: good
- Corrosion resistance: good
- Weldability: good
- Surface finish: poor
-
EN AW 7020
Due to its high strength, the 7020 alloy is widely used in the aerospace industry. A notable feature of the 7020 alloy is its ability to recover its final strength after welding, regaining up to 80% of its original strength. No other variant of this aluminium alloy possesses this characteristic.
This makes it a particularly reliable choice for welded components that must retain their strength, such as structural frameworks, construction structures, and also structural parts in aircraft and aerospace applications. For example, Mifa previously developed a part for a zeppelin using this composition, where the component recovers and reaches 80% of its original strength after approximately three months.
- Strength: high
- Formability: fair to good
- Corrosion resistance: fair
- Weldability: good
- Surface finish: moderate
-
EN AW 7022
The aluminium 7022 alloy is highly suitable for heavily loaded components due to its high mechanical properties and good fatigue resistance. This hard alloy is therefore excellent for use in the aerospace, defence, and space sectors.
- Wear resistance: high
- Machinability: good
-
EN AW 7075
Due to its high strength, the EN AW 7075 aluminium alloy is widely used in the aerospace industry. It has excellent mechanical properties and offers good resistance to metal fatigue. It is one of the most commonly used aluminium alloys for (heavily loaded) constructions. However, due to its high material strength, it is not possible to manufacture hollow profiles with the EN AW 7075 alloy.
- Strength: very high
- Formability: good
- Corrosion resistance: fair
- Weldability: good
- Surface finish: moderate
-
AZ31
The AZ31 alloy contains a small percentage of aluminium, which enhances its mechanical properties and improves its corrosion resistance.
- Strength: strong
- Formability: good
- Corrosion resistance: good (when combined with the appropriate coating/surface treatment)
- Weldability: good
- Surface finish: fair
-
AZ61
The AZ61 alloy exhibits similar properties to the AZ31 alloy, but due to its higher aluminium content, it has increased corrosion resistance and higher material strength. However, because of its high material strength, it is not possible to manufacture hollow profiles with this alloy.
- Strength: very strong
- Formability: fair to good
- Corrosion resistance: good (when combined with the appropriate coating/surface treatment)
- Weldability: good
- Surface finish: fair
-
6066
This alloy is used for extrusion in welded constructions. It contains a significant amount of both magnesium and silicon and is formulated primarily for shaping into rolled products.
- Strength: good
- Formability: moderate to poor, due to high strength
- Corrosion resistance: excellent
- Weldability: good
- Surface quality: moderate
-
6463
The 6463 alloy is similar to the 6063 but offers the possibility of achieving an excellent surface finish with reflective properties. The 6463 is very easy to extrude.
- Strength: moderate
- Formability: excellent
- Corrosion resistance: good
- Weldability: good
- Surface quality: good
-
6061 (20% SiC)
The 6061 alloy is known for its wide range of applications across industries such as aerospace, construction, marine, sports, recreation, and electronics. This alloy is difficult to extrude and has limited surface properties. The 6061 is widely used in the United States.
- Strength: excellent
- Formability: good
- Corrosion resistance: good
- Weldability: good
- Surface quality: average
-
Metal Matrix Composites (MMCs)
Metal matrix composites (MMCs) often consist of a low-density metal, such as aluminium or magnesium, reinforced with particles or fibres of a ceramic material.
- Strength: high
- Wear resistance: good
-
Aluminium-scandium alloys
These alloys are a group of aluminium alloys intentionally alloyed with scandium to enhance their properties. They are primarily known for their ability to provide significant strength improvements at high temperatures compared to conventional aluminium alloys.
- Strength: excellent
- Formability: good
- Corrosion resistance: good
- Weldability: good
- Surface quality: good
Contact us for more information
Aerospace alloys
In our range, we offer various alloys for aerospace applications. For instance, the 6061 and 7075 aluminium alloys are frequently chosen for extrusion profiles due to their excellent combination of strength, corrosion resistance, and machinability. Aluminium 6061 is valued for its versatility in aerospace applications, while aluminium 7075 excels in uses requiring maximum strength.
Additionally, the 7020 and 7022 alloys are also highly suitable for aerospace and aviation. Aluminium 7020 stands out for its improved resistance to corrosion and fatigue, whereas aluminium 7022 is particularly suited for components that must withstand high loads, thanks to its excellent mechanical properties and good fatigue resistance.
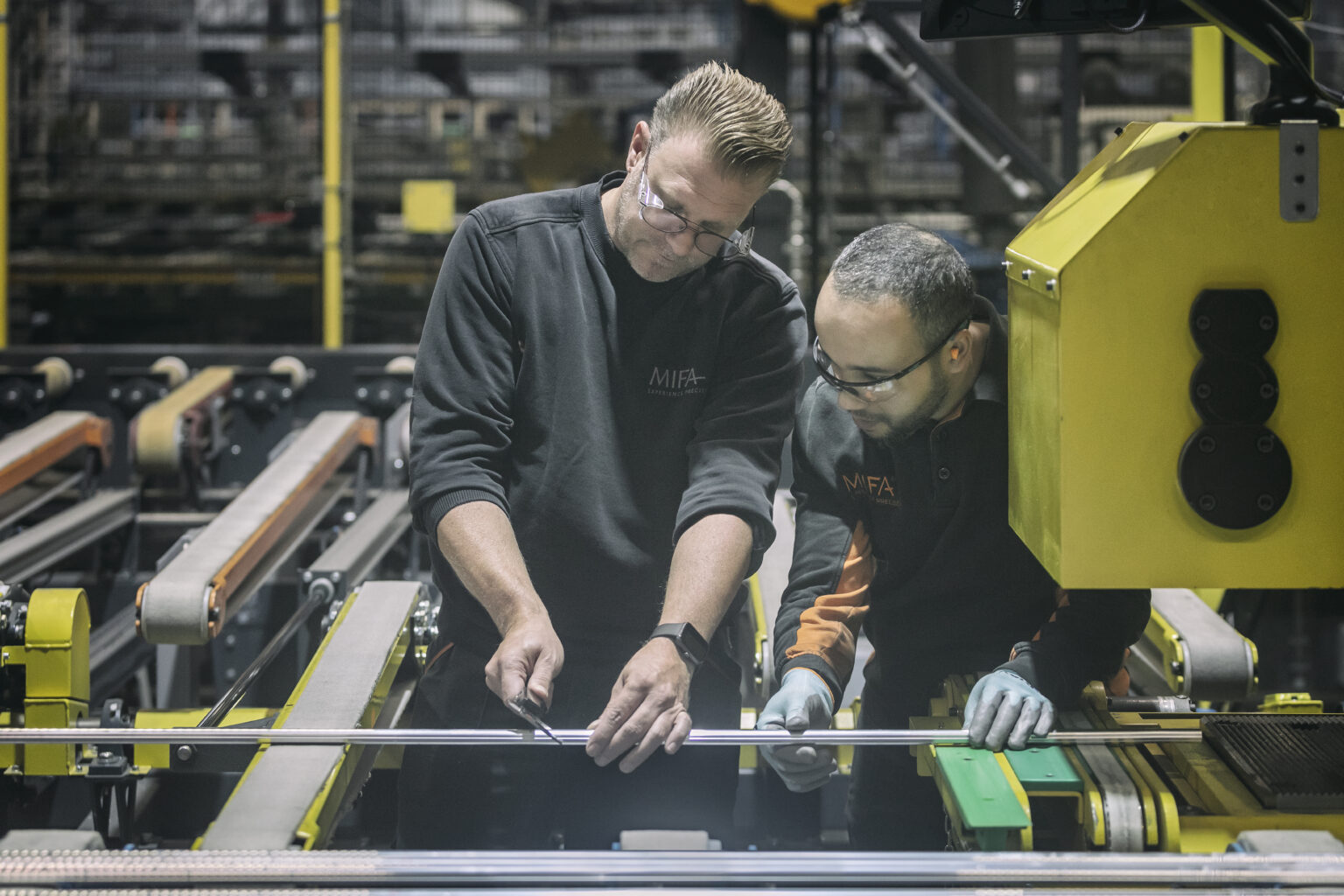
Aluminium heat treatments
To enhance specific properties of aluminium alloys, heat treatments are applied. These treatments can improve strength or enhance formability.
The properties altered in the aluminium depend on the temperature, intensity of the process, alloy type, and duration of the treatment. During heat treatment, the profile is strengthened by the precipitation of alloying elements. This process differs significantly from the hardening process in steel. Heat treatments are applicable to the 2xxx, 6xxx, and 7xxx series.
Heat treatments are classified according to the T-temper designation. The “T” stands for ‘tempered’, followed by a number between 1 and 10 that defines the basic treatment. Additional numbers specify further details.
Several treatments are possible, including:
- Peak strength (maximum strength)
- Natural ageing (improved formability)
- Over-ageing (enhanced corrosion resistance)
Common temper designations include:
- T5/T6: Solution heat treated, quenched, and artificially aged
- T4: Solution heat treated, quenched, and naturally aged
- T7: Solution heat treated (in an oven), quenched, and over-aged. This is only applicable to the T7 7075 alloy
- O: Annealed. Only solution heat treated or aged
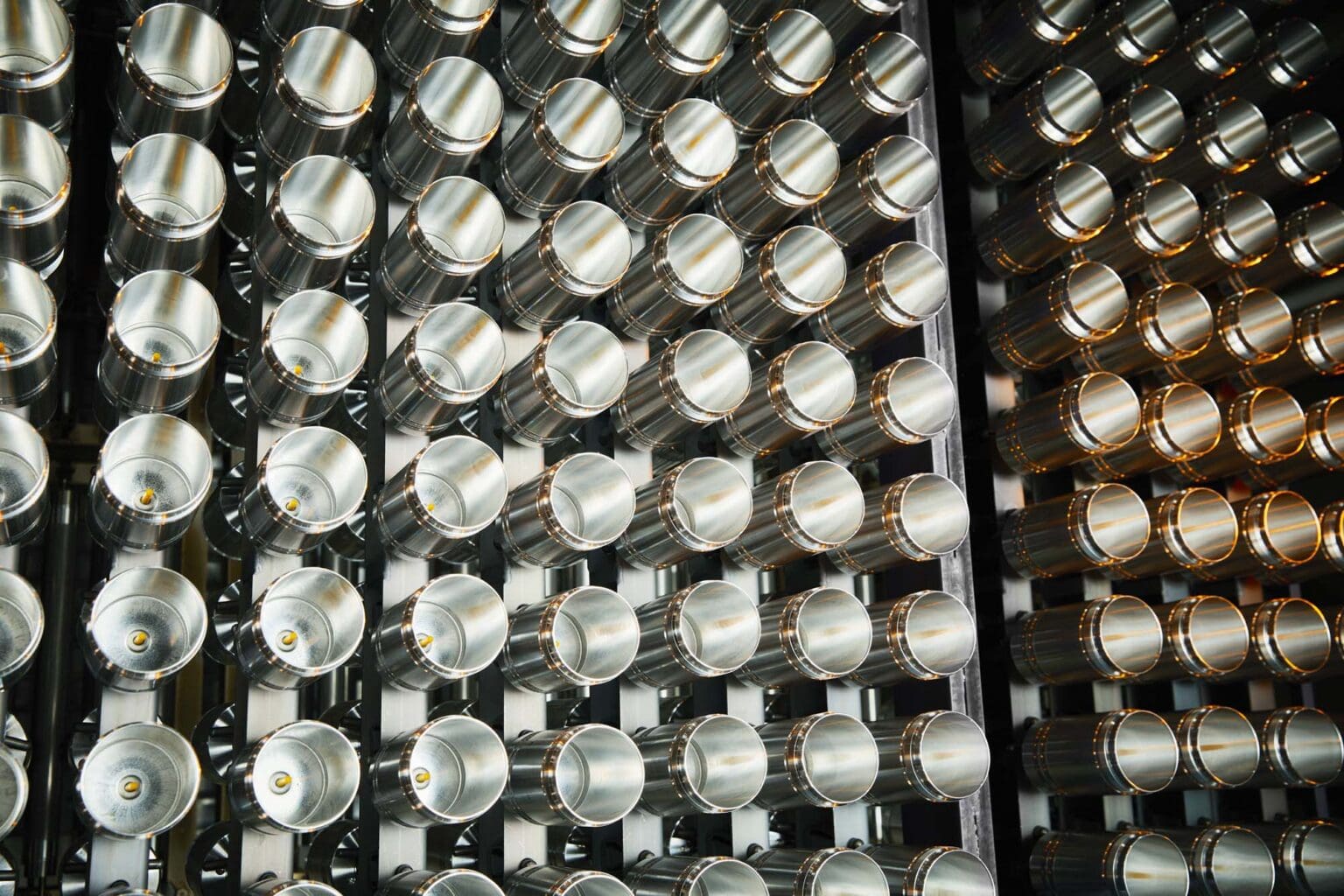
Surface treatment by metal alloy type
Choosing the right alloy plays a significant role in achieving a high-quality extrusion profile. Additionally, surface treatments can further enhance the quality of the final product.
Besides precision extrusion, Mifa specialises in surface treatments, meaning we can facilitate the entire processing in-house. We often see custom aluminium profiles receiving surface treatments to improve or, in some cases, eliminate specific product properties such as corrosion resistance. Selecting the correct treatment is crucial for the intended application.
At Mifa, we offer three types of surface treatments:
- Anodising (including GLISSCOAT®, HART-COAT®, technical anodising)
- Passivation
- Polymer coatings (including Tufram®, Lectrofluor, Nedox)
We calculate the CO₂ emissions of your extrusion profile
The choice of an aluminium alloy can have a significant impact on the sustainability of a product—both in terms of environmental effects and the product’s lifespan. Consider the following aspects:
- Recyclability: Aluminium is one of the most recycled materials worldwide. Some alloys are more recyclable than others, meaning they require less energy when reused.
- Corrosion resistance: The durability of the aluminium profile or product heavily depends on the alloy’s resistance to corrosion, which also affects the product’s lifespan.
- Energy consumption and CO₂ emissions during production: The chosen alloy can influence the energy used in manufacturing aluminium.
- Alloy properties such as weight: These directly impact energy consumption and CO₂ emissions.
Our engineers are happy to assist you in selecting the right alloy. Based on the chosen alloy, they can also calculate the CO₂ footprint for producing an aluminium extrusion profile and advise on aspects like wall thickness using our customised LCA tool.
-
What are the properties of aluminium?
Aluminium is known for being lightweight, strong, and corrosion-resistant. It’s also highly formable and a great conductor of heat and electricity. These properties make it ideal for technical applications especially when precision and efficiency matter.
-
Are aluminium alloys corrosion resistant?
Definitely, but it depends on the alloy and the post-treatment. Unfinished aluminium naturally forms an oxide layer, but for demanding applications we apply extra treatments like anodising or passivation to ensure maximum protection.
-
Is magnesium stronger than aluminium?
Magnesium is lighter than aluminium, but usually less strong and less resistant to corrosion. That’s why in applications where structural strength and long-term durability are essential — such as in aerospace or precision engineering — aluminium alloys are generally the better choice.
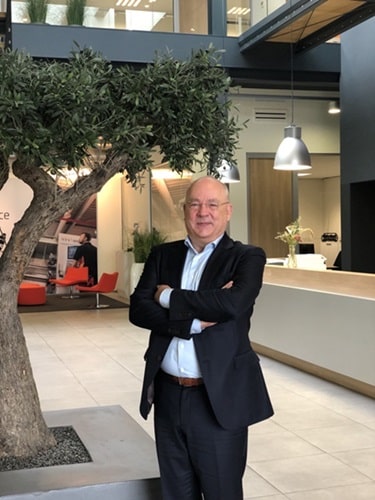