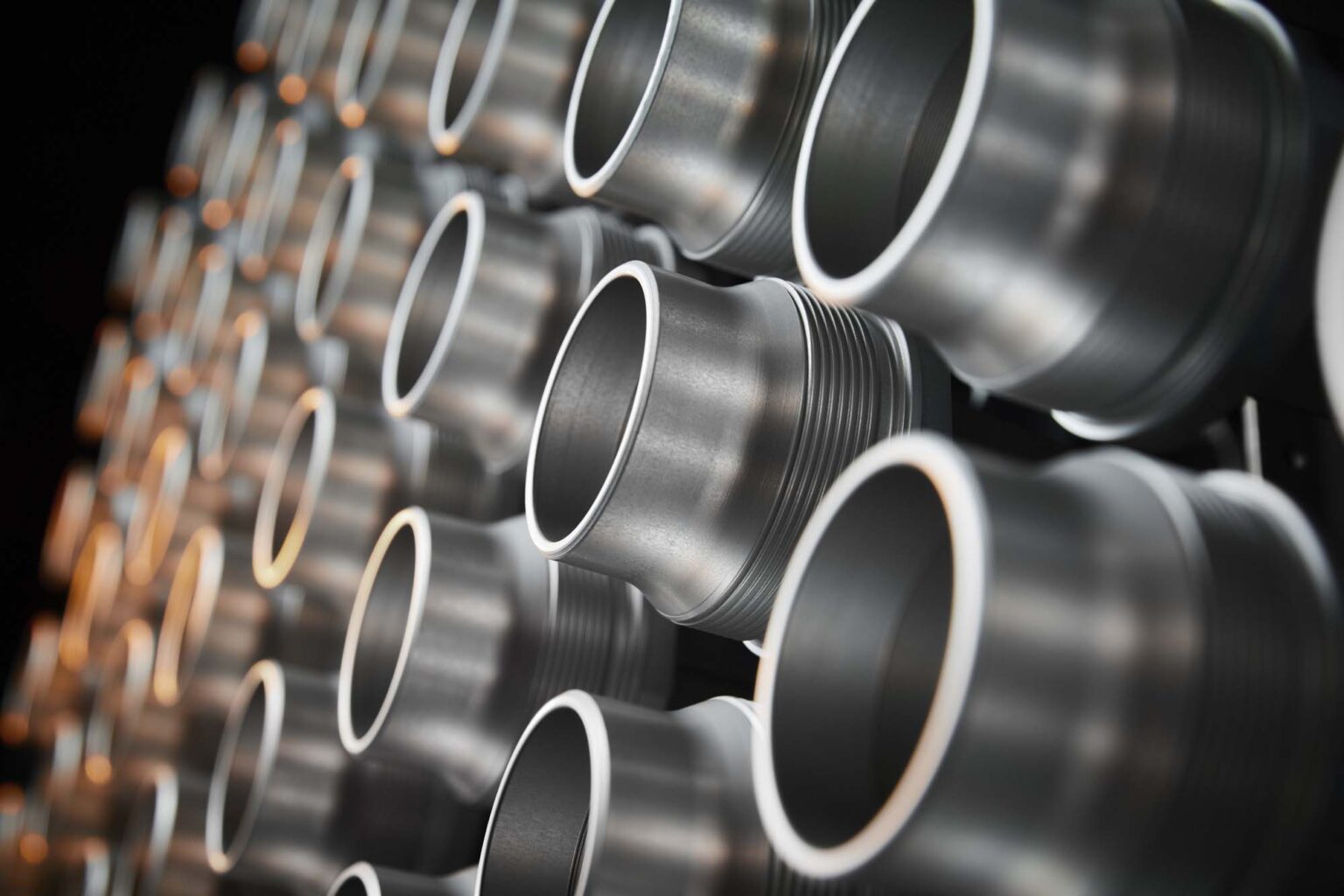
Anodising aluminium profiles at Mifa
A process where strength and aesthetics come together to create a durable aluminium profile. What anodising exactly involves and what Mifa can do for you can be found on this page.
At Mifa, there are various possibilities and unique processes to enhance products, including the anodisation of aluminium extrusions. With our in-house surface treatment process, we go beyond just extruding aluminium profiles: by creating an additional protective oxide layer, we elevate products to an even higher level. Additionally, through an electrolytic treatment, we not only create an improved corrosion layer but also enhance aesthetics and achieve durability.
What is anodising?
Anodising is an electrochemical process in which aluminium is converted into aluminium oxide (Al2O3) in a controlled environment. By using electric current and an electrolyte (sulfuric acid) and continuously dissolving aluminium, a layer is formed with numerous pores.
An anodised layer is hard and brittle, with properties comparable to glass or ceramics. The layer may ‘break’ under strong bending, as it is an inherent material-specific layer with exceptional adhesion to the substrate, which is aluminium. Practical anodised layers range from 5 to 60 µm, depending on the alloy and application. The physical law governing the anodising process is Ohm’s Law: U = I x R, where Voltage (V) = Current (A) x Resistance (Ω).
Anodising is a galvanic process but with a reversed pole. The workpiece is connected to the anode, unlike standard galvanic processes (such as silver plating). During anodising, the resistance of the formed layer increases, influencing the anodising process/build-up speed, which is controlled by programmed process sequences.
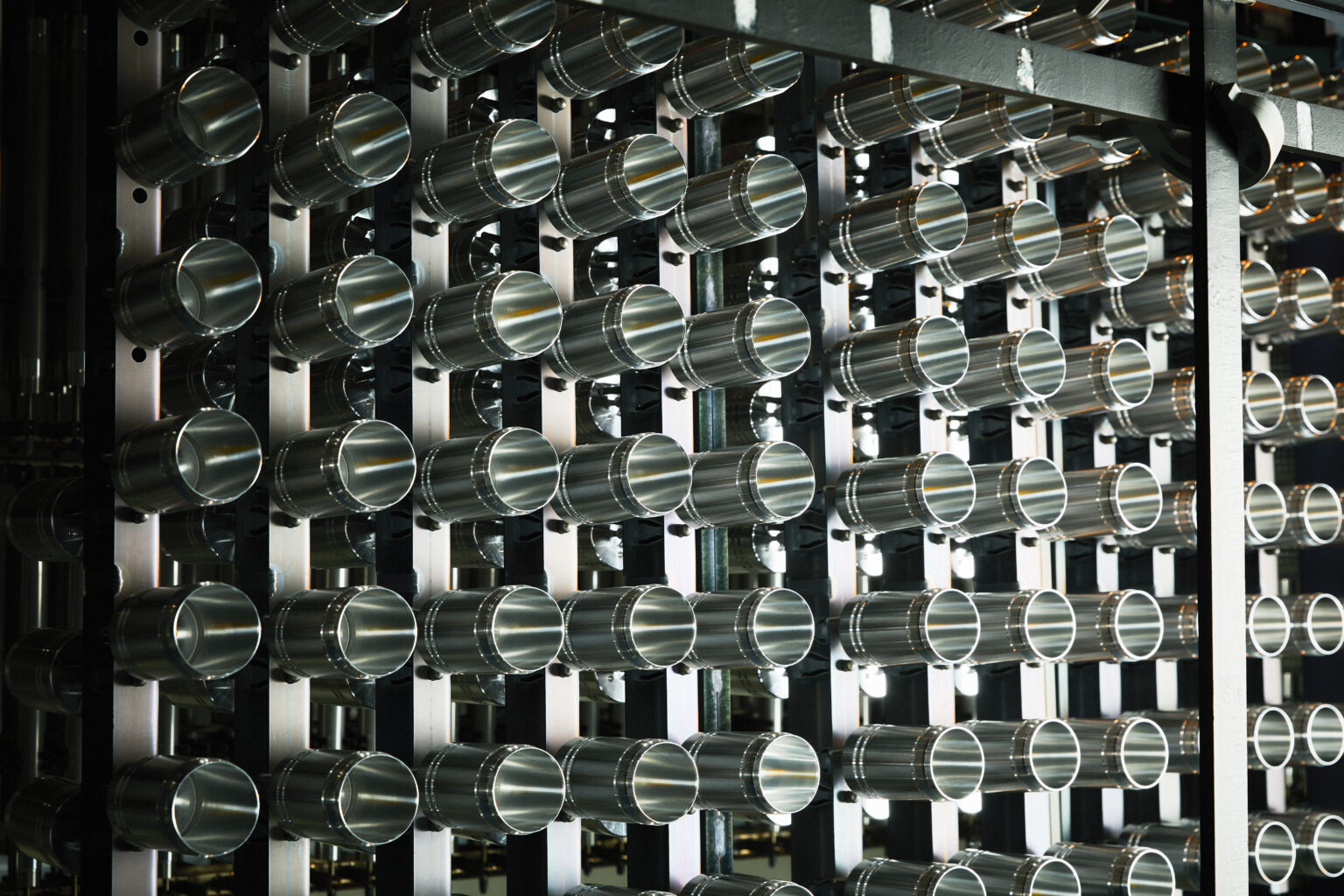
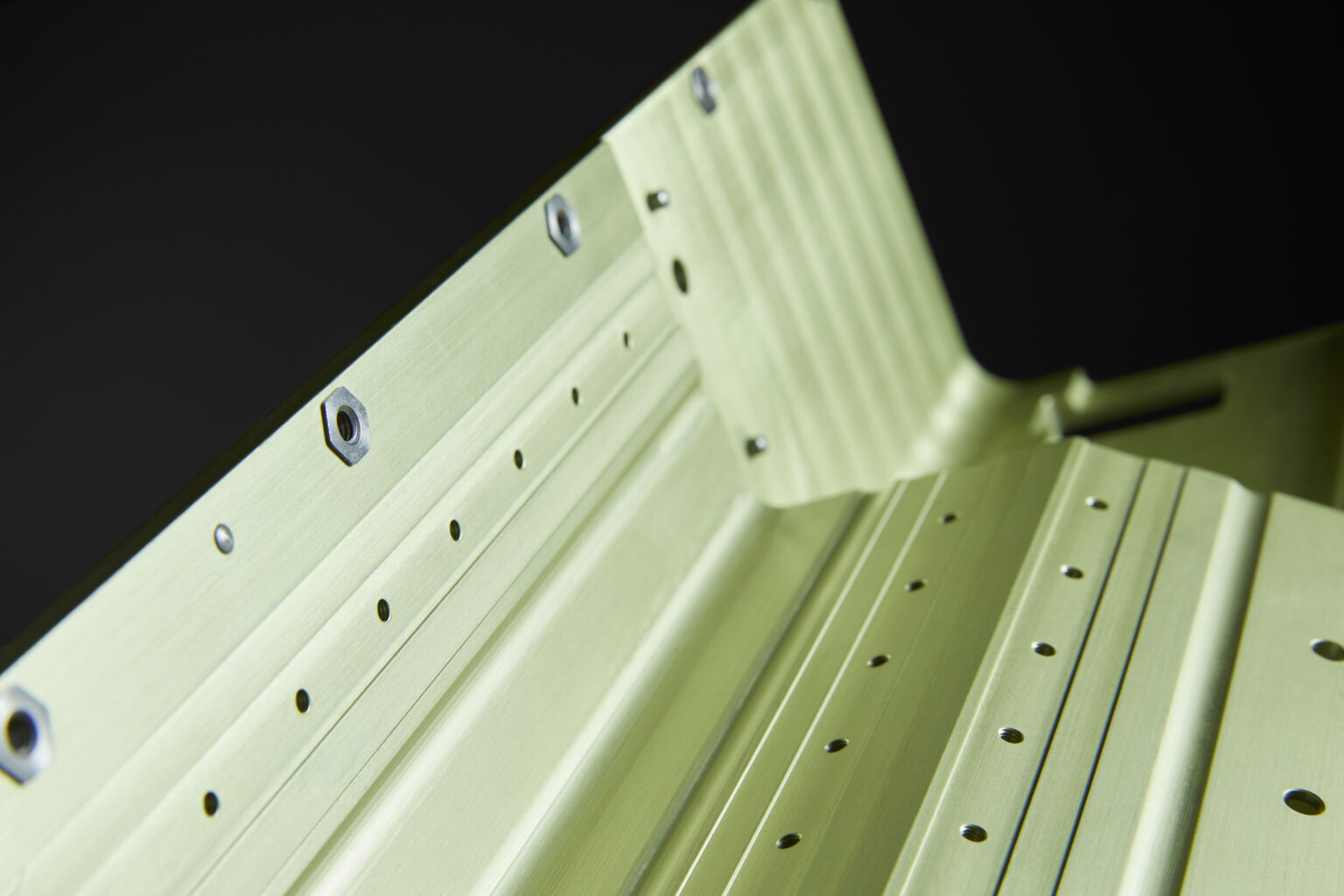
Why anodise aluminum?
The anodisation of aluminium profiles provide advantages in terms of weight and (mechanical) workability. Some benefits of anodising that can contribute to the properties of aluminium include:
- Corrosion resistance;
- Wear resistance;
- Optical requirements;
- Insulation and reflection;
- Adhesive base for paints or adhesives;
- Sliding properties;
- Non-stick.
Mechanical pre-treatments | Chemical pre-treatments | Post-treatments |
Blasting: machining in-house, glass bead via external partner | Standard (dimensionally stable) pickling: products delivered at final dimensions retain their dimensions | Colouring: absorbent color baths provide a deep black coloration; other colors are negotiable. |
Tumbling: deburring and polishing technique using stones | Matte pickling: a matting of the surface ensures retouching of irregularities (not dimensionally stable) | Sealing: the open pore structure is compacted using hot water (96 °C), creating corrosion resistance |
Belt grinding | (Medium) gloss pickling: satin finish effect that also makes light scratches less visible (dimensionally stable is possible) | Application of primers and/or paints through wet painting (for project-based applications) |
Impregnation with polymers: see Tufram® in the polymer layers process group |
GLISSCOAT® | HART-COAT® (hard anodising) | Technical anodising (normal anodising) | |
Specifications |
|
|
|
Applications |
|
|
|
Anodising aluminium profiles makes a sustainable contribution
Anodising aluminium profiles is a process that not only enhances the aesthetic value of aluminium but also makes a sustainable contribution to the industry and the environment. This process, which creates a protective oxide layer, has several sustainable benefits:
- Corrosion resistance: anodisation forms a hard and durable oxide layer on the aluminium surface, making the profile resistant to rust and corrosion. This extends the lifespan of the aluminium components, resulting in less waste as they need replacement less frequently.
- Energy efficiency: the anodisation process involves chemical reactions and electricity but occurs in a controlled environment. The energy consumption is relatively lower compared to alternative methods such as galvanization.
- Recyclability: aluminium is naturally a recyclable element, and an anodised aluminium profile retains its properties during the recycling process.
- Reduced harmfulness: anodisation serves as an alternative to traditional paint and coating systems, which often contain harmful solvents and chemicals. Anodisation contributes to cleaner production and reduced environmental impact.

Unique bright-dip on the profiles of SodaTASTE
Together with our customers at Mifa, we create the best end product. With one of our knowledge partners, SodaTASTE, we have anodised aluminium bottles in colour. During the design phase, various steps were taken to achieve a unique product. A great example of how Mifa employs co-engineering to collaborate with the customer during the design phase.
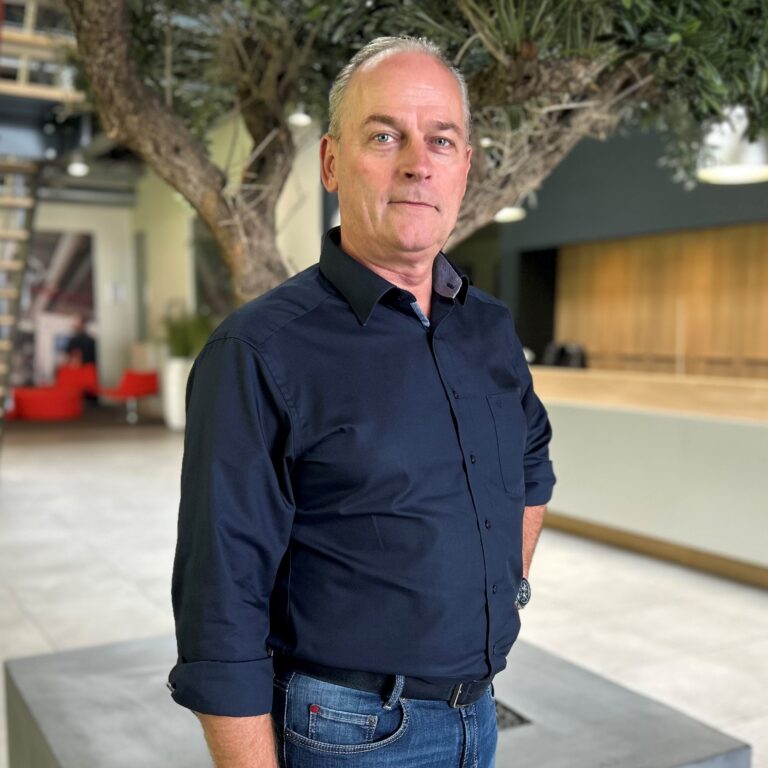
Get in touch with us
Call or email Fons
Manager Surface Treatment