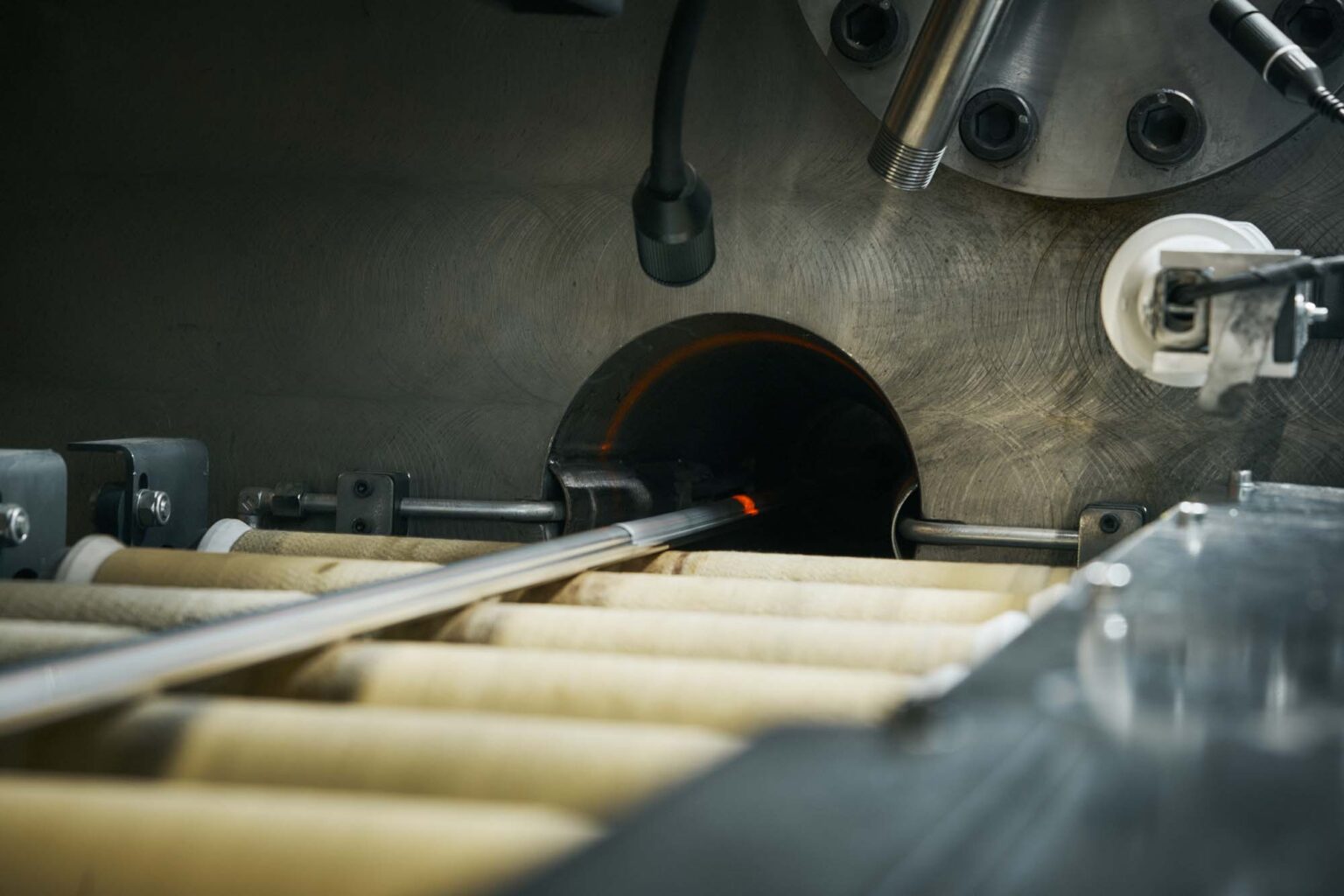
Optimisation of microscope motor housing
From a precision extrusion masterclass to a co-engineered profile, culminating in a microscope.
New insights thanks to a Mifa Masterclass
The microscope manufacturer is a familiar partner of Mifa. We have been producing a component for one of their microscopes for several years. However, it remained limited to this one part. Because we believed that we could offer more to each other, we organized a masterclass for their engineers. During this session, we explained the possibilities of extrusion. Key points included precision, the ability to produce small quantities, and design freedom in construction. The masterclass convinced the engineers that precision extrusion is a viable alternative or even the best solution for many designs. It immediately resulted in an inquiry.
The manufacturer is working on a new platform. It includes a drive mechanism for positioning a stage. The manufacturer asks us to propose a possible housing design. A part where multiple functionalities need to come together: cooling, precise assembly of the drive unit, easy placement of circuit boards, and ‘design’.
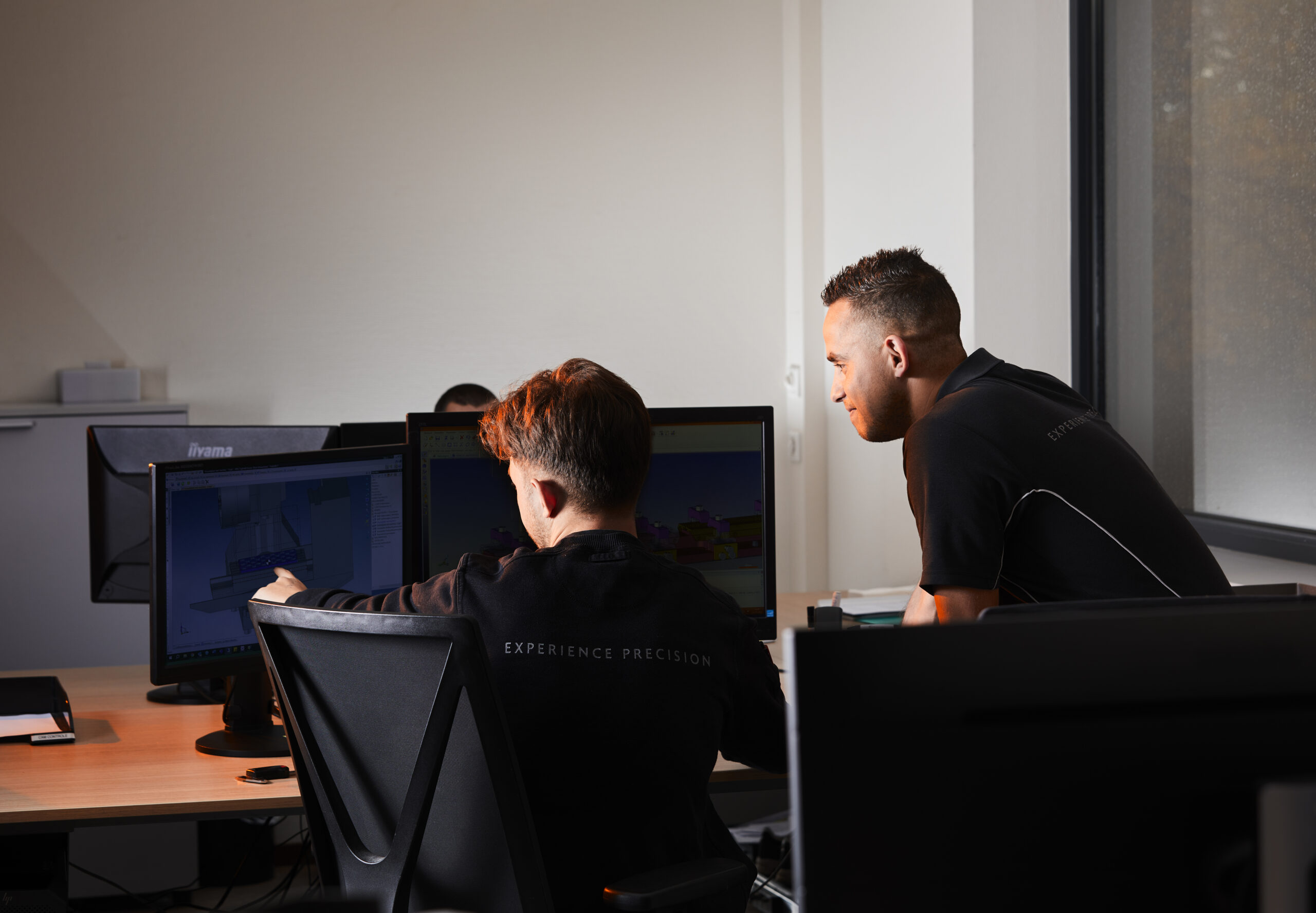
The optimal profile thanks to co-engineering
The original construction was the idea of an optimal extrusion according to the manufacturer. Unfortunately, this proposal was not feasible in terms of extrusion technology. We immediately came up with a counterproposal to split the part into two sections that could slide into each other. Based on this proposal, we entered into discussions with the engineers. It quickly became clear what the most essential aspects of the product were. With this knowledge, it was possible to create the optimal profile.
The second concept followed with the proposed changes, which already incorporated some typical precision extrusion “smart” features:
- Half-opened screw channels to be incorporated during extrusion;
- Connections for a cover profile;
- Ribbed cooling fins to increase the surface area.
These are typical elements that are easily integrated into a profile during the extrusion process.
After a final discussion between engineers and designers, we ultimately arrived at the third and final design. This design is precise, stable, manufacturable in a single process, and meets all the customer’s requirements.
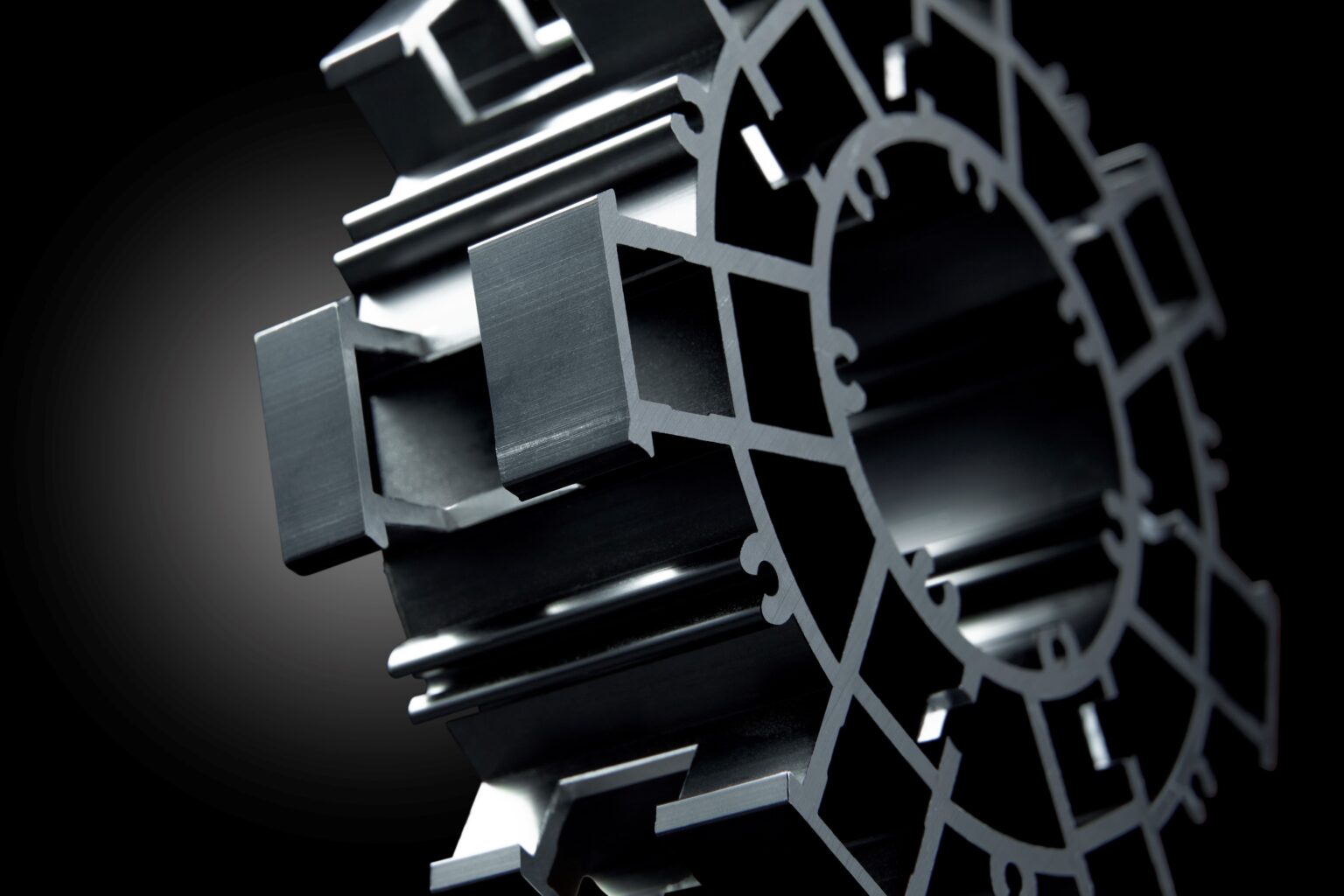
Precision extrusion brings new insights
The designers of this client had not been thinking in terms of extrusions for a while. This was mainly due to the persistent prejudice that aluminium extrusion is only interesting for bulk production. In the masterclass, we were able to convince the designers that Mifa delivers precision extrusion in quantities starting from 10 kilograms and also provides profiles so accurate that post-processing is often not necessary anymore. The client is satisfied with the design and the result. It left them wanting more: the company has since entrusted us with five orders for other components.
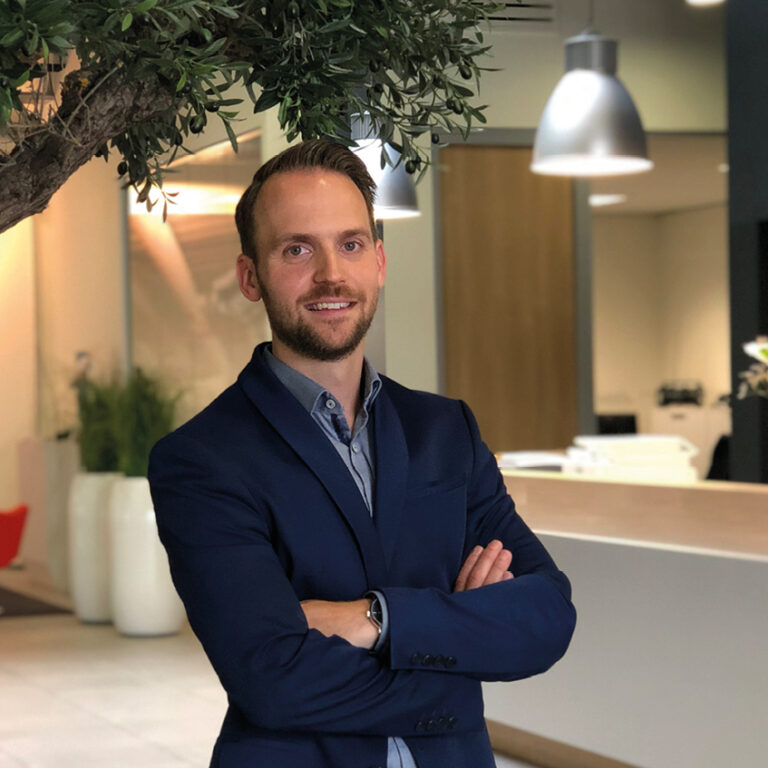
Innovative extrusion profiles for 3D printer of Rapid Shape
Innovative extrusion profiles for 3D printer of Rapid Shape
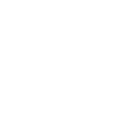
High performance cosmetic requirements in aerospace
High performance cosmetic requirements in aerospace