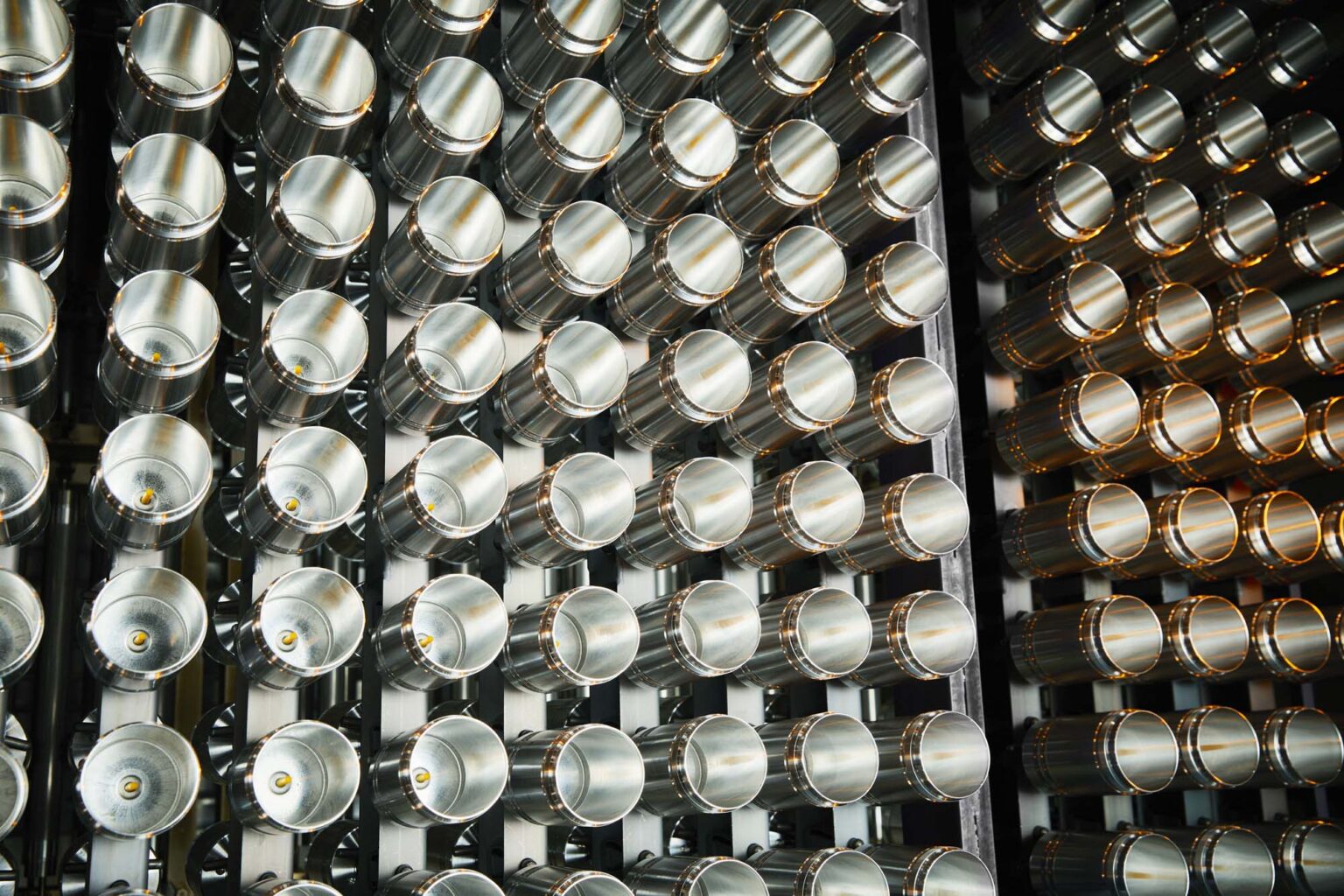
Passivation of aluminium at Mifa
Passivating aluminium provides long-term corrosion protection and durability, serving as the key to aluminium preservation
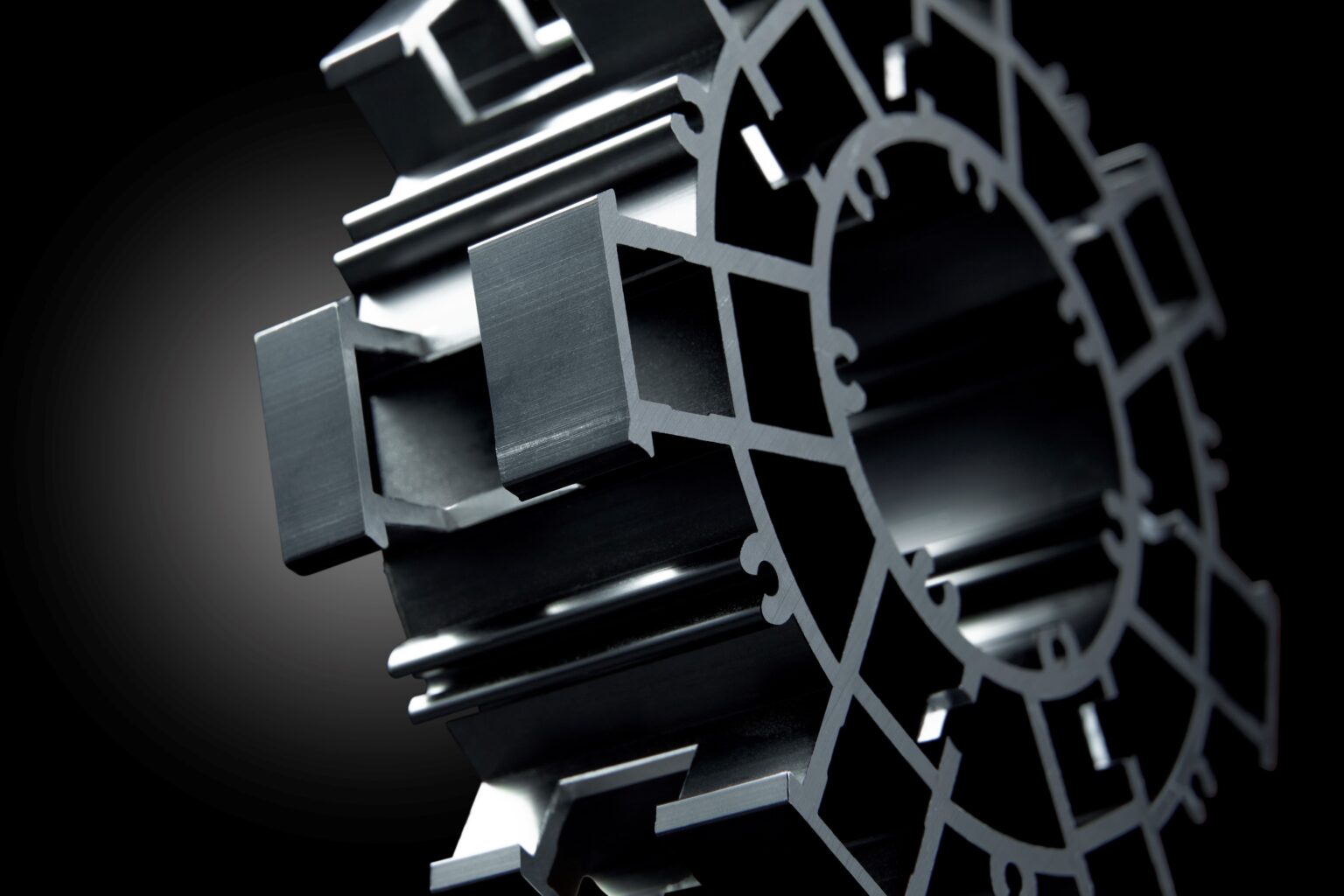
The advantages and disadvantages of passivating aluminium
By making the surface of a workpiece passive, corrosion is prevented. The formed conversion layer also serves as a good foundation for applying various types of paint. This layer is electrically conductive with a constant resistance, providing the following benefits:
- Improvement of corrosion resistance;
- Basis for (wet) coating systems;
- Constant resistance for electrical conduction.
Passivation is a chemical process and can be applied through immersion or spraying. The process is contactless, and the workpiece can often be treated in baskets, providing cost advantages. The layer complies with various standards and is also approved for the aviation industry. The mechanical load capacity of this layer is very limited, and the layer is not self-healing.
Passivation of aluminum profiles as a sustainable solution
Aluminium passivation is a process used to enhance the corrosion resistance of aluminium profiles. A thin oxide layer is applied, protecting the underlying metal from corrosion, resulting in prolonged life and structural integrity of the aluminum. This provides various sustainable solutions:
- Extended lifespan: by applying aluminium passivation, we extend the lifespan of our aluminium extrusion profiles. This means the profiles need to be replaced less frequently, reducing the demand for new raw materials and energy for production.
- Energy efficiency: passivating aluminium contributes to energy efficiency as the oxide layer on the surface reduces heat conduction. This can contribute to preserving energy in applications where heat loss is a concern.
- Reduced environmental impact: since oxidized aluminium is more resistant to corrosion, there is less need for aggressive cleaning and maintenance procedures that can cause environmental damage. This leads to a lower environmental impact of aluminium production and use.

Unique Bright-dip on the profiles of SodaTASTE
Together with our customers, we strive to produce the best end product. Our engineers are eager to engage in a conversation with you to elevate your end product to the next level. With one of our knowledge partners, SodaTASTE, we have anodized aluminum bottles in color. During the design phase, various steps were taken to create a unique product. A great example of how Mifa employs co-engineering to collaborate with customers during the design phase.
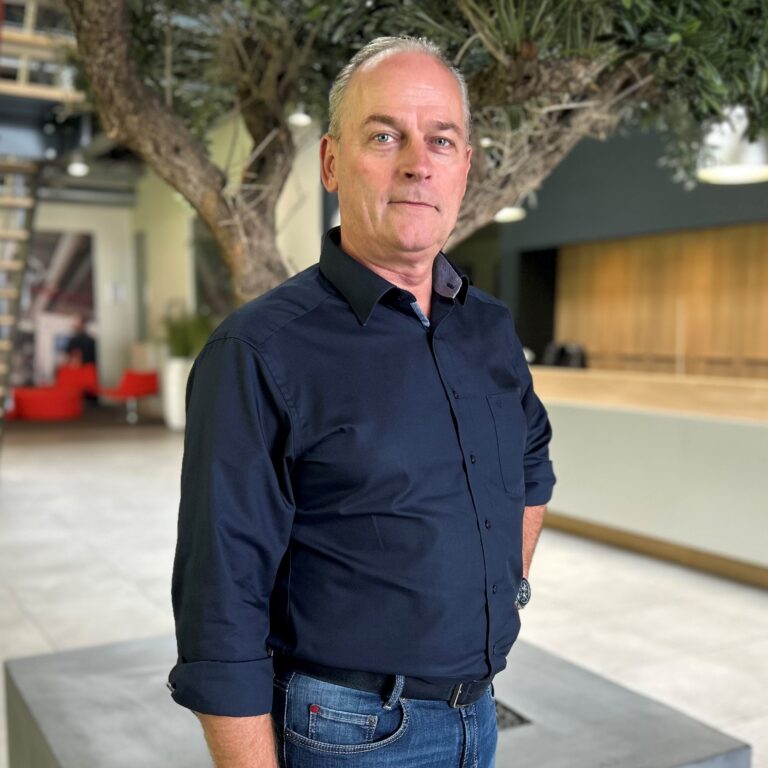
Get in touch with us
Call or email Fons
Manager Surface Treatment