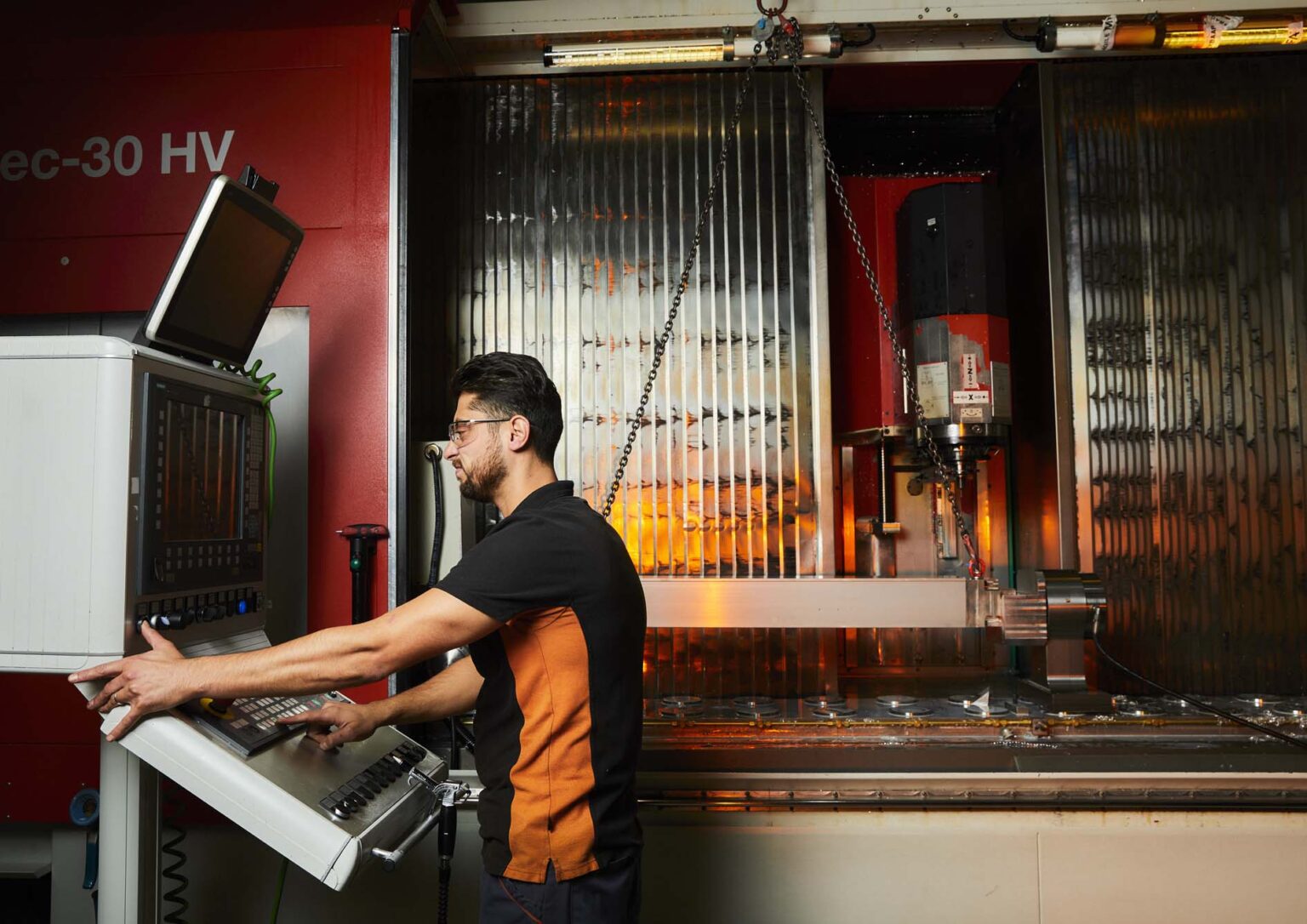
The possibilities of machining at Mifa
At Mifa, we specialise in precision machining of aluminium and magnesium profiles using modern CNC machines. Discover how our co-engineering, precision extrusion, and CNC machining result in high-quality end products with lower costs.
CNC Machining at Mifa
At Mifa, we specialize in producing aluminium extrusion profiles with tolerances as tight as +/- 0.02 mm. The combination of precision extrusion, CNC machining, and surface treatment allows us to shorten the total production time of machining operations while simultaneously improving the quality of the product.
Machining at Mifa summarized:
- Tolerances starting from +/-0.01 mm;
- A machine park of approximately 30 CNC-controlled machines, partially roboticized;
- 3-, 4-, and 5-axis machining with up to 60,000 revolutions per minute;
- Maximum dimensions: X=6500mm, Y=1000mm, Z=500mm;
- Special profile machining machines;
- Special Aerospace CNC machining machines;
- CAD/CAM programs: SolidWorks, SolidEdge, Unigraphics, Catia, TopSolid, Step, IGES;
- We write our own software programs;
- Clamping/workholding methods;
- Machining techniques: milling, tapping, turning, drilling, sawing, boring, countersinking, and honing.
Coordination of extrusion, CNC machining, and surface treatment
Through knowledge and experience, we can significantly enhance products. The coordination between the extrusion process, CNC machining, and surface treatment is crucial in achieving this. If extrusion can be precisely produced directly, we save a considerable amount of time in machining. Experience has taught us the minimum wall thicknesses needed in an extrusion profile to machine various materials.
Your own designs are, of course, welcome with us. Whether it’s developing or machining a custom profile, component, or product, we deliver it to you exactly according to your preferences and specifications.
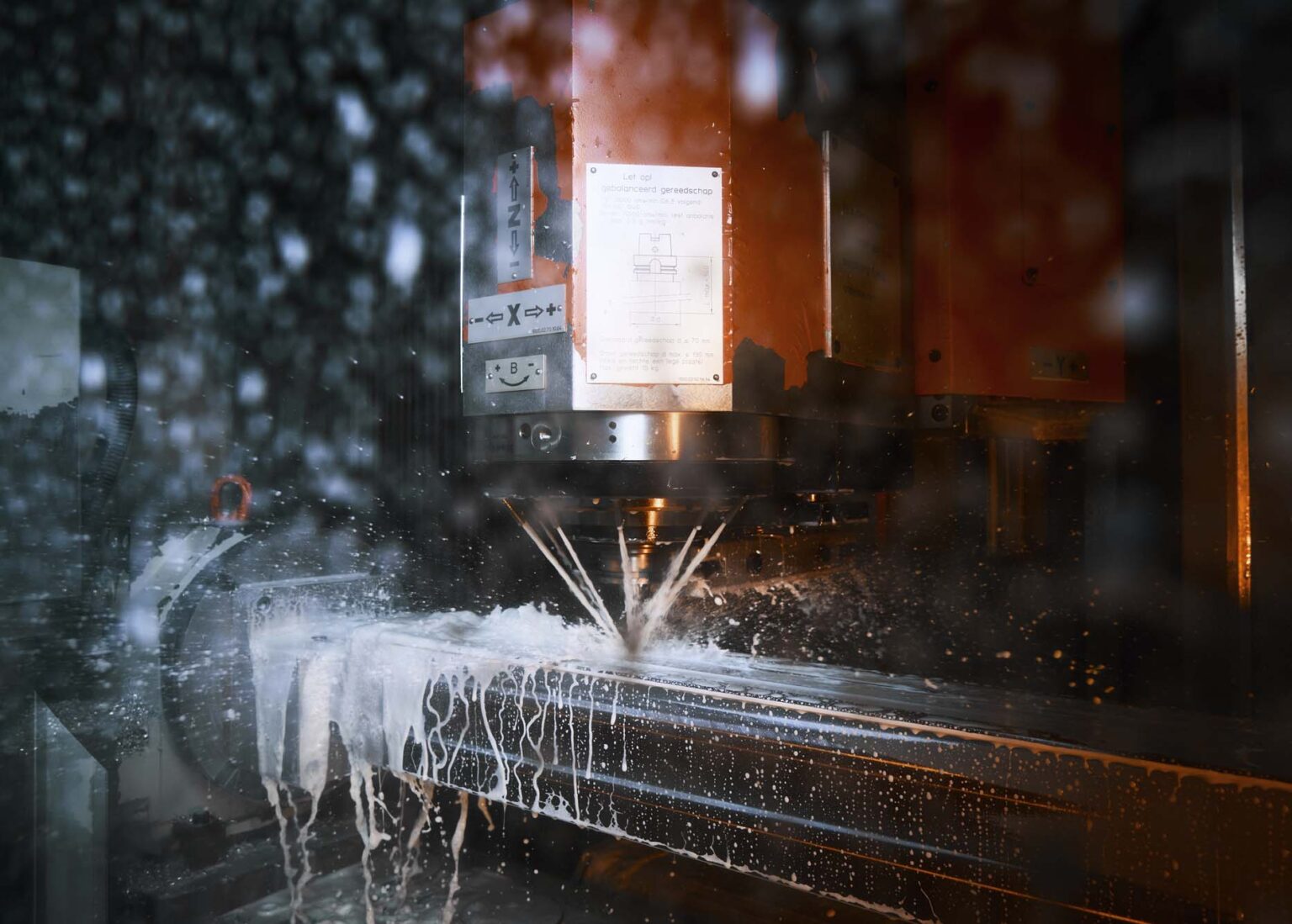
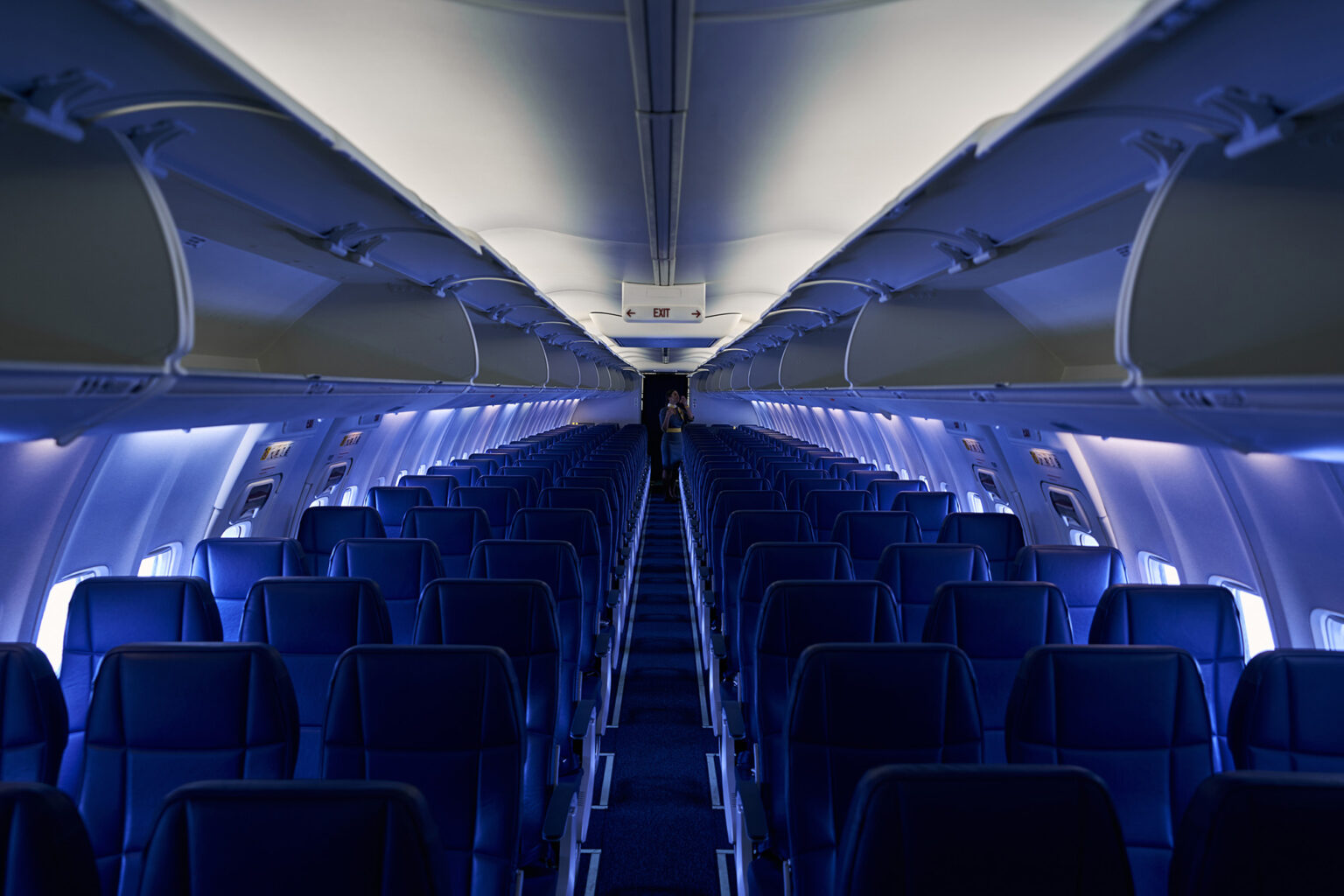
Co-engineering, extrusion, and machining result in a better end product
For a customer, we are manufacturing a housing for the aircraft control system. Electrical conductivity is crucial, and the customer’s preference was to produce the product as much as possible in one piece, with minimal connections. Originally, the customer made the product from bent sheet metal, attaching many different components. This involved a lot of manual work and assembly, resulting in unique products with numerous connections.
In close collaboration with the engineers, we explored the possibility of creating the housing using a combination of extrusion and machining. This led to a creative solution with three extruded parts connected precisely through a dovetail joint, with only four separate components attached. Together with the customer, we developed a stable process where each product is identical, and assembly time is minimized. Benefits include a superior end product at reduced costs.
Get in touch with us
If you want to benefit from our experience and expertise in precision extrusion, machining, and surface treatment, involve Mifa’s engineers early in the process. Ultimately, this results in a more efficient, higher-quality, and refined profile, component, or product that can typically be produced faster and at lower costs.