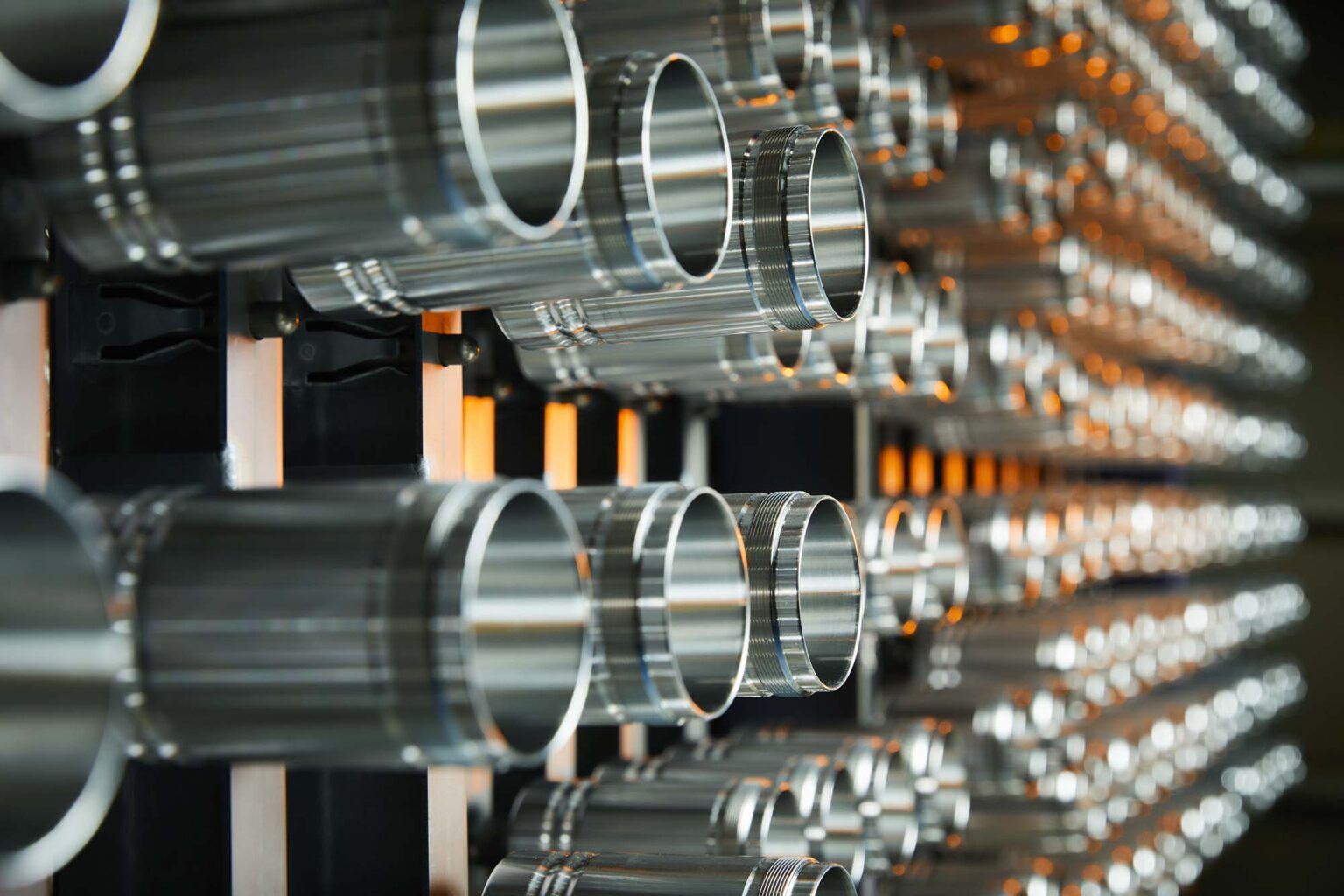
Polymer layers: protection and style in one coating
Polymer layers on aluminium offer an innovative coating for protection and versatility
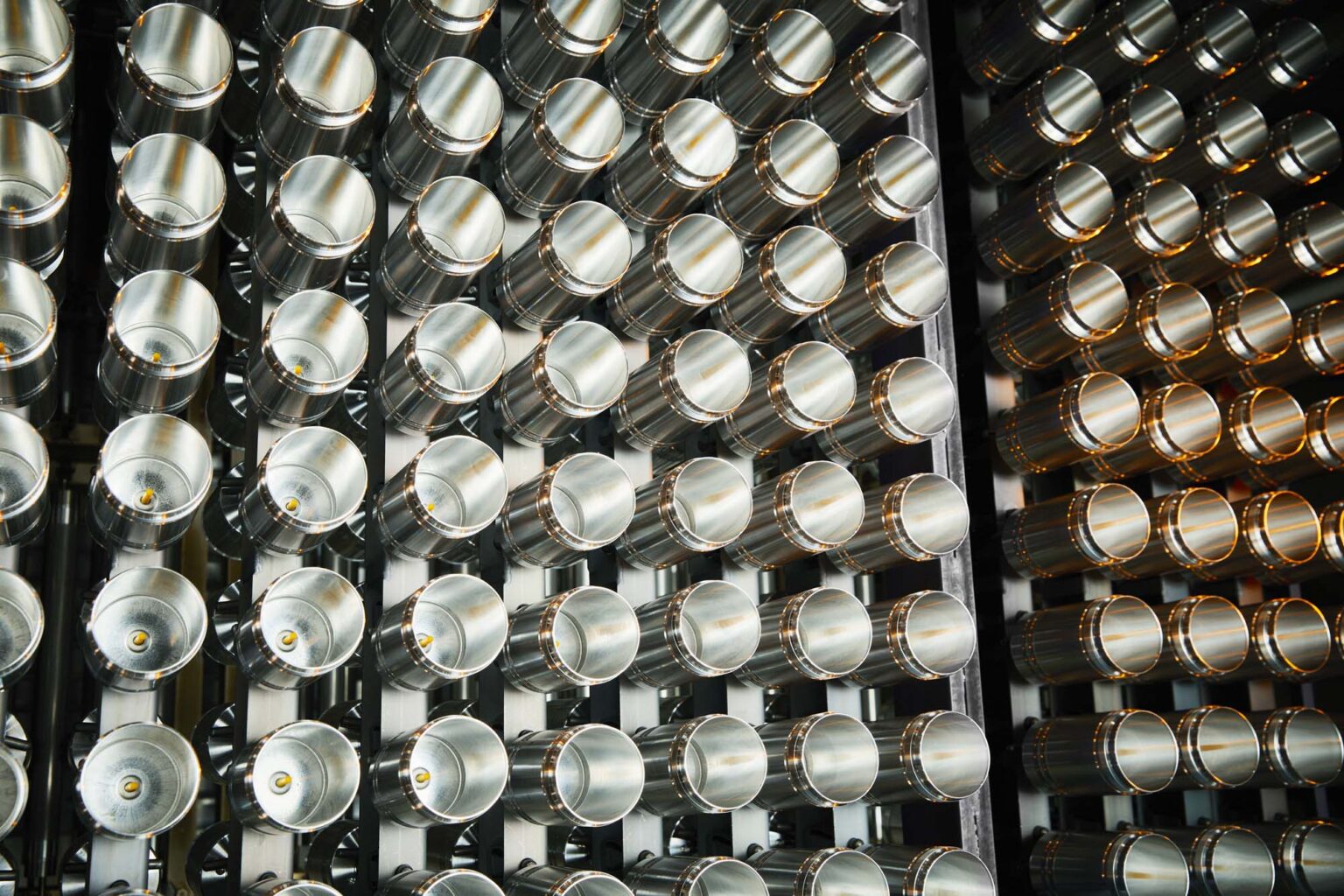
The TUFRAM® polymer coating
TUFRAM® is the collective name for a family of coatings, where the aluminum surface is converted into aluminum oxide (Al2O3). During the process, the aluminum crystals grow into a porous layer that remains hygroscopic for a short time and possesses optimal adhesion properties. The heat molecule of this newly formed ceramic oxide layer is replaced by inert polymers, providing a self-lubricating surface. This results in a hard, self-lubricating, ceramic surface in which the polymer particles are integral. TUFRAM® can be used in various applications, including the food industry, automotive industry, pharmaceutical industry, and aerospace industry.
The polymer layer LECTROFLUOR®
The LECTROFLUOR® series provides superior protection against corrosion, chemicals, and abrasive wear for metal components and equipment. Due to the FDA/USDA compliance of some variants, these coatings are ideal for applications in the food and pharmaceutical industries, as well as for external medical applications. The series enhances the wear resistance and performance of various types of metal, offering excellent protection against corrosion and chemical attacks. LECTROFLUOR® coatings are based on carefully blended technical polymers with a low coefficient of friction. The metal parts are first cleaned and pretreated in a specially developed production line. The selected polymers are then applied either by standard spray treatment or by electrostatic spraying, depending on the type of polymers and the final application.
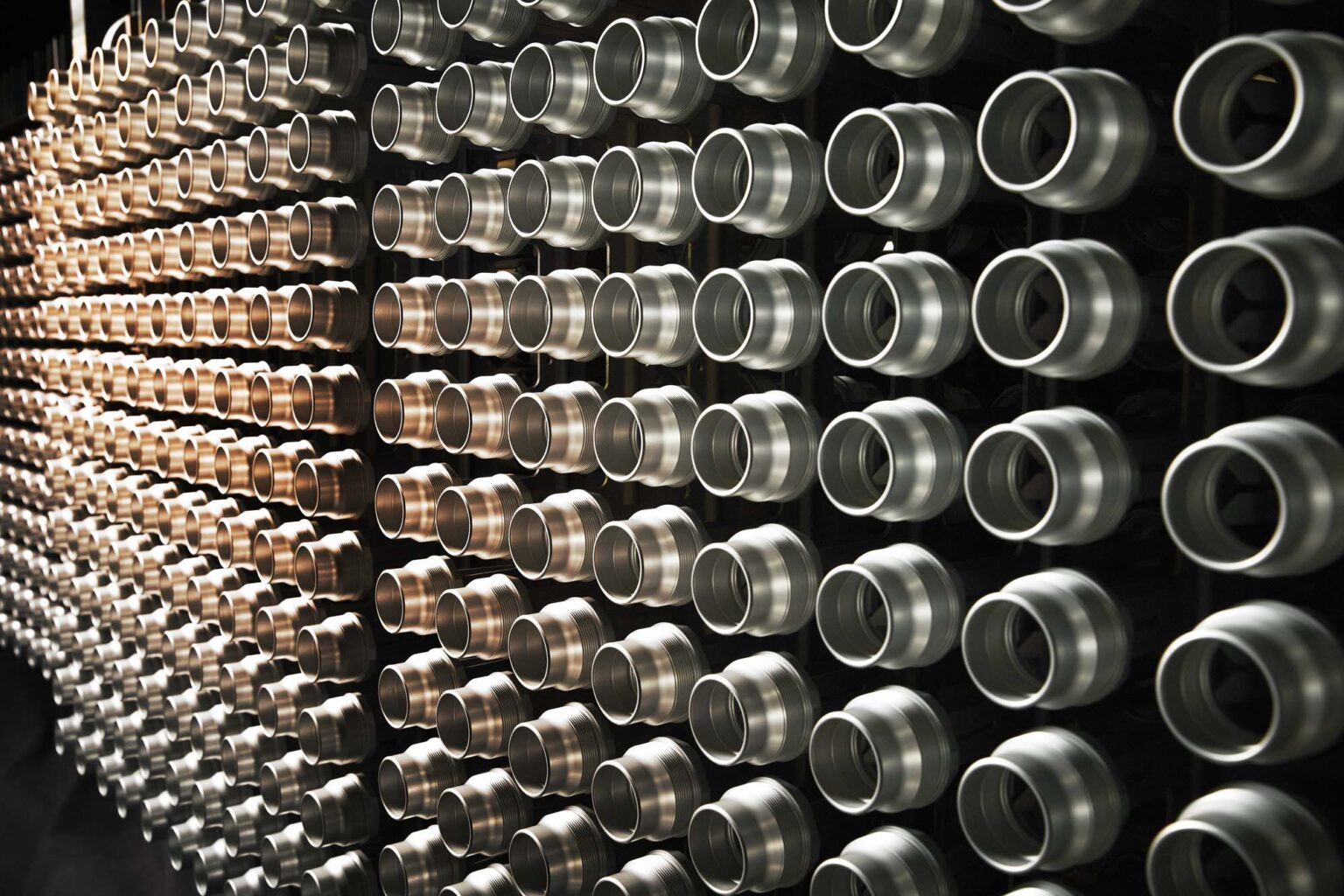
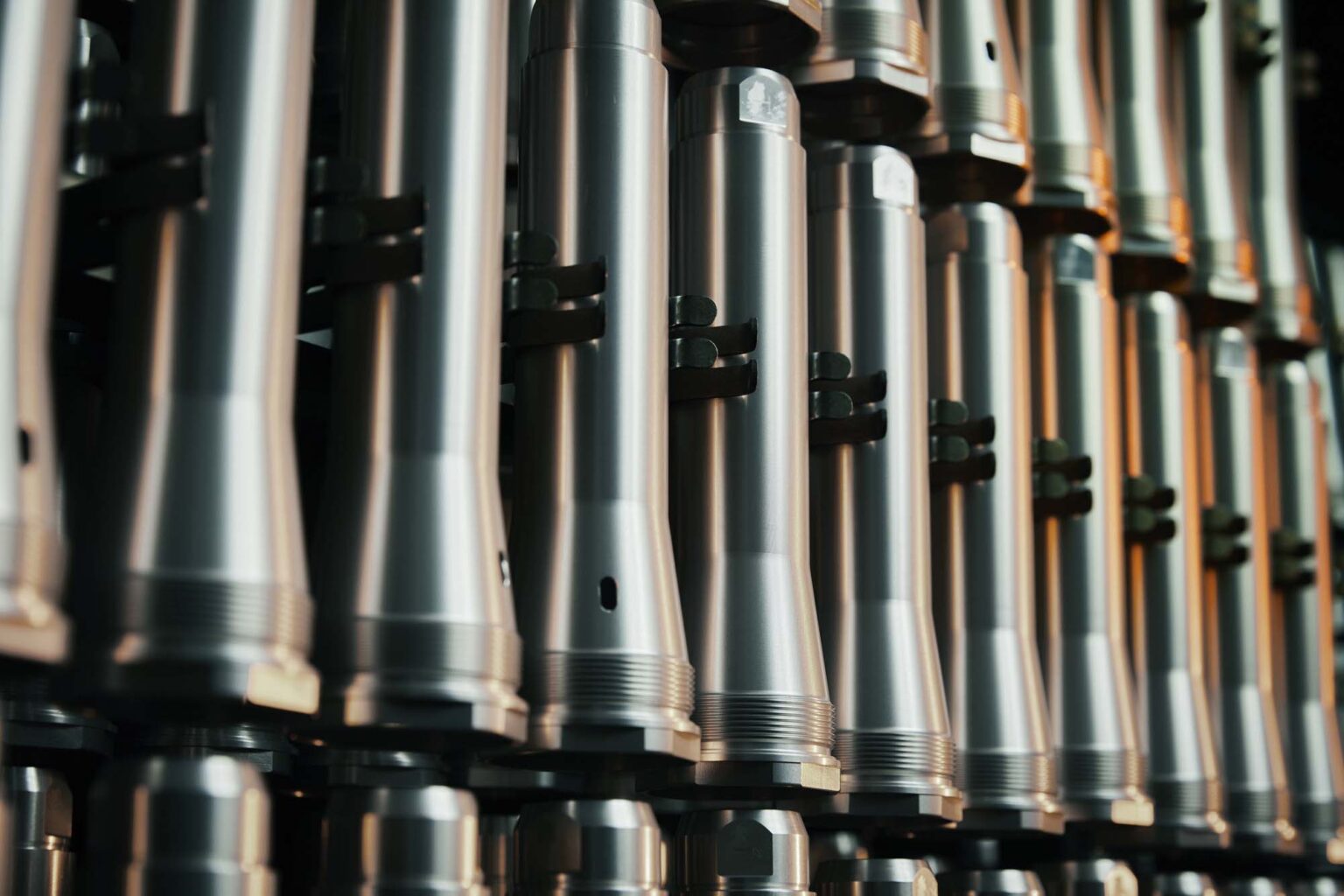
The polymer layer NEDOX®
In the NEDOX® process, we apply a nickel-phosphorus alloy to the metal surface under conditioned circumstances. This layer contains countless pores that are enlarged through a series of patented process steps. The surface is compacted by the controlled introduction of polymers, and in the final phase of the NEDOX® process, a complete integration occurs between the polymers and the surface. The NEDOX® process creates a new, hard, smooth, and self-lubricating surface with high wear resistance and corrosion resistance. NEDOX® is also highly chemically resistant, possesses permanent non-stick and antistatic properties. NEDOX® is often used for applications in the following industries: pharmaceutical, mobility, and semiconductor.
Polymer coatings on aluminium profiles provide sustainable benefits
Polymer coatings on aluminum contribute to the sustainability of components and products in various ways:
- Corrosion Protection: Polymer coatings effectively shield aluminum against corrosion. Aluminum is susceptible to corrosion, and applying a polymer layer helps protect it from corrosive substances such as moisture, salts, and chemicals, significantly extending the lifespan of aluminum profiles.
- Extended Lifespan: Polymer coatings enhance the wear resistance of aluminum, prolonging the life of components before replacement is necessary. This reduces the need for frequent replacements, thereby decreasing waste and raw material consumption.
- Energy Efficiency: Aluminum profiles with polymer coatings can last longer and maintain effective performance, reducing the need for replacement and energy-intensive production processes. This leads to improved energy efficiency and a smaller ecological footprint.

Unique Bright-dip on the profiles of SodaTASTE
Together with our customers, we create the best end product at Mifa. With one of our knowledge partners, SodaTASTE, we have anodised aluminium bottles in color. During the design phase, various steps were taken to achieve a unique product. A great example of how Mifa uses co-engineering to collaborate with the customer during the design phase.
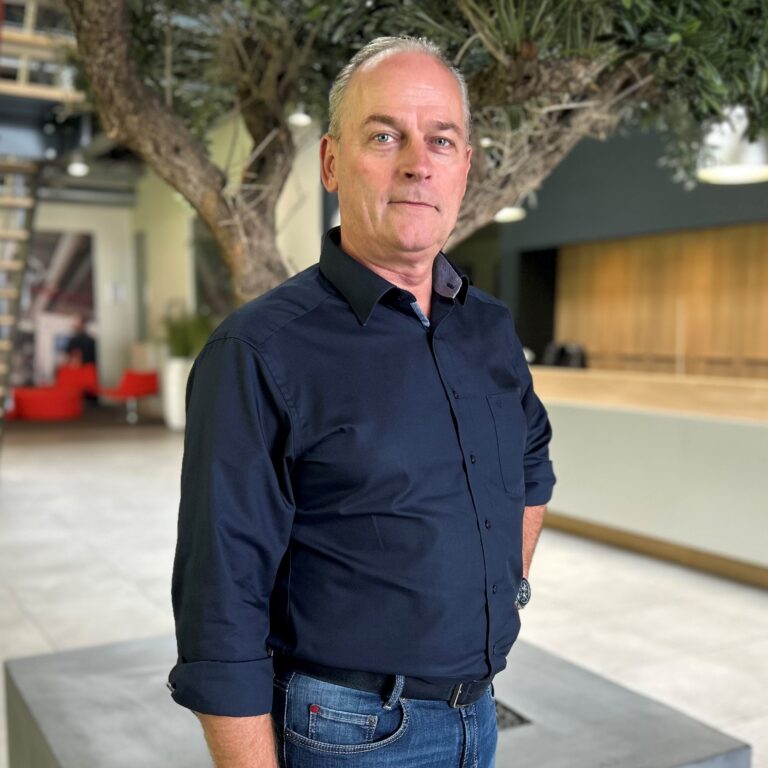
Get in touch with us
Call or email Fons
Manager Surface Treatment