Mobility: innovation and quality - in one profile
Customised solutions for mobility, automotive and suspension extrusions
Producers in the mobility industry choose to work with Mifa because of the high level of quality and precision we can provide in our aluminium extrusion profiles. An important focus in the automotive section is innovation; therefore, design freedom is crucial.
Our extensive knowledge and years of expertise result in innovative extrusions for the automotive industry. Our precision extrusion profiles are used in applications such as:
- Cooling heat exchanges
- Interiors
- Suspension systems
- Braking systems
- Suspension
Advantages of aluminium and magnesium extrusion at Mifa
Thanks to precision extrusion, we offer engineers tremendous design freedom. With tolerances of +/- 0.02 mm, the possibilities are endless, and designers do not have to consider limitations or standard norms.
Alloys for the mobility market
Mifa uses various alloys of aluminium, magnesium, and other materials such as copper. With these alloys, we achieve approximately 95% of our extrusion profiles exactly according to specification. Common aluminium alloys for the automotive industry include 3003, 6061, 6082, AZ31, and 1050. Our engineers are happy to advise you on the choice of alloy.
Cost and weight savings with magnesium
One of our customers, Porsche, has for example opted for a magnesium roof after testing magnesium, aluminium, and carbon fiber reinforced plastic (CFRP). Magnesium came out on top, shaving off ten kilograms of weight as the strongest and lightest material. This incredible material is versatile and can be integrated into various stages of the production process. By switching to magnesium components for the mobility industry, we can build lighter cars compared to using traditional materials.
Contact us for more information
Tolerances from +/- 0.02 mm
Wall thicknesses from 0.25 mm: substantial weight savings
Profile weight from 0.003 kg/m to 10 kg/m
Profile dimensions from ø 180 mm / 220 x 60 mm
Avoid/reduce costly machining (post) processing steps
Vertical integration: all processes can be realised in-house
Precision extrusion
With dimensional tolerances as low as +/- 0.02 mm, we go beyond the norm for complex aluminium and magnesium extrusion profiles.
Machining
In a modern machine park with more than 30 CNC machines, we perform all machining operations on aluminium and magnesium profiles.
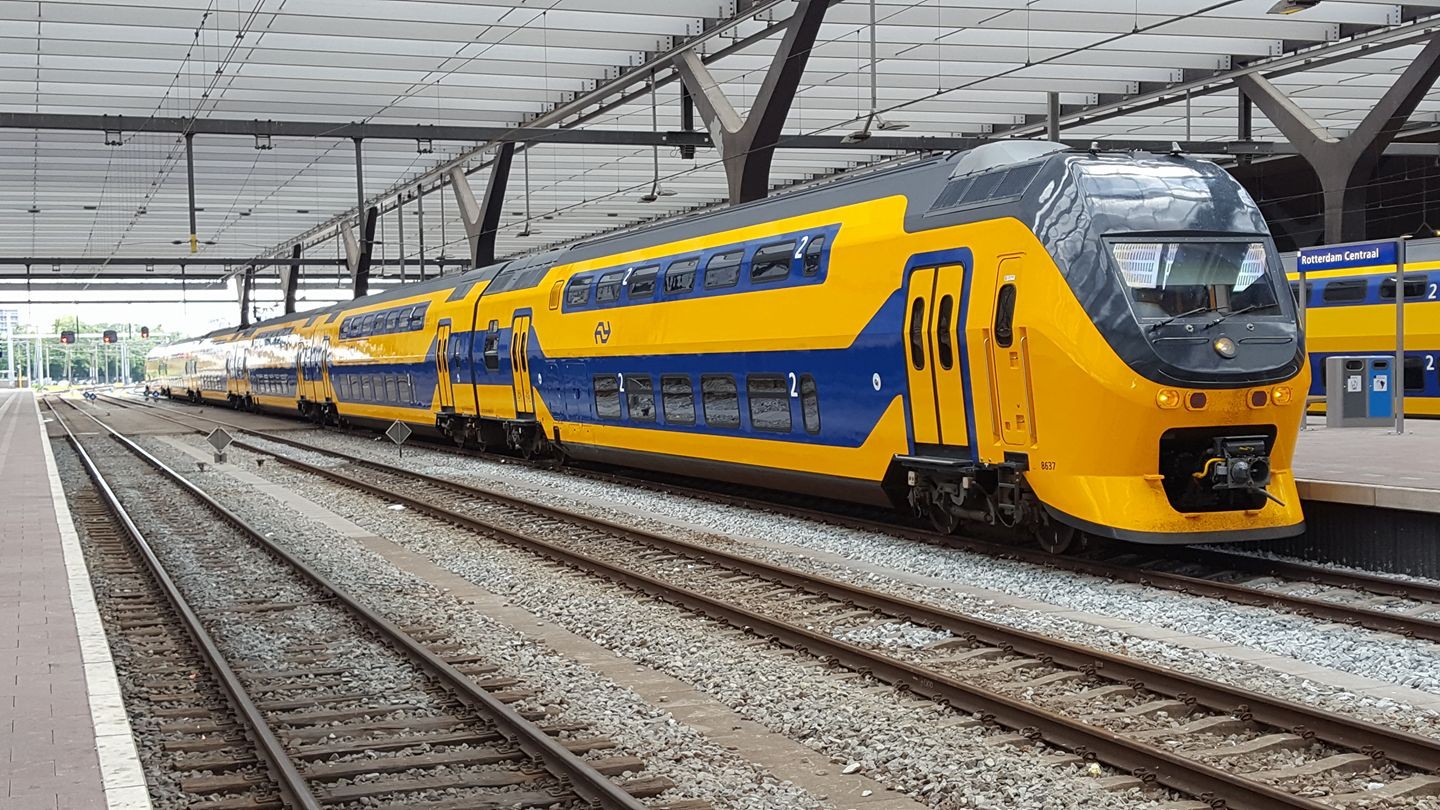
Case study: Mifa delivers a complete package to NedTrain
Vertical integration makes Mifa unique. We can fully produce the profile in-house for many customers. With techniques such as extrusion, sawing/brushing, machining, surface treatment, and assembly, we can take full responsibility for an aluminium profile. For more than 50 years, our customers have chosen Mifa.
Even NS Train Modernization, known to Mifa as NedTrain, has been a customer for years. Mifa produces KITS for various profiles found in a train. In this case, you can read about how the collaboration has unfolded.
High quality standards
At Mifa, we go beyond the standard quality control and assurance covered by the EN-755-9 and EN-12020-2 standards. With the special AS9100 certificate, we adhere to all rigorous quality standards for the aerospace industry, ensuring product quality in the mobility market as well.
Co-engineering
Our certifications are a validation of continuous quality in all of our processes. But our quality standards are also verified through our years of expertise. Our engineers provide advice during the development of a custom profile, component or product. This involves selecting the appropriate aluminium alloy, thinner wall thicknesses, saving CO2-emissions: some of the many choices our engineers can help you with. This partnership can result in a product with enhanced efficiency, quality and refinement.

Sustainability: top of mind
Aluminium has a long lifespan and remains 95% recyclable after use. It requires minimal maintenance, but at Mifa, we go a step further. We constantly consider energy consumption, waste management, vitality, safety, and the health of our employees. Specifically, Mifa has achieved the following performances:
- Mifa saves 78% emissions with in-house production compared to others.
- With full in-house production, Mifa saves a significant amount of CO2, a common ecological culprit: transport.
- Mifa’s thin-walled profiles result in a material saving of 33%.
Sustainability has become a crucial topic in many sectors, including the mobility market. Reducing the ecological footprint and promoting environmentally friendly solutions are goals receiving increasing global attention. As a result, our thin-walled profiles are finding their way into mobility-related sectors. By contributing to weight savings and energy efficiency, these thin-walled aluminium profiles contribute to the transition to more sustainable mobility solutions.
Together with our partners and engineers, we have developed a specialized tool for life cycle analysis (LCA). This tool calculates emissions and demonstrates the positive impact of co-engineering on reducing the CO2 footprint. Contact us for more information
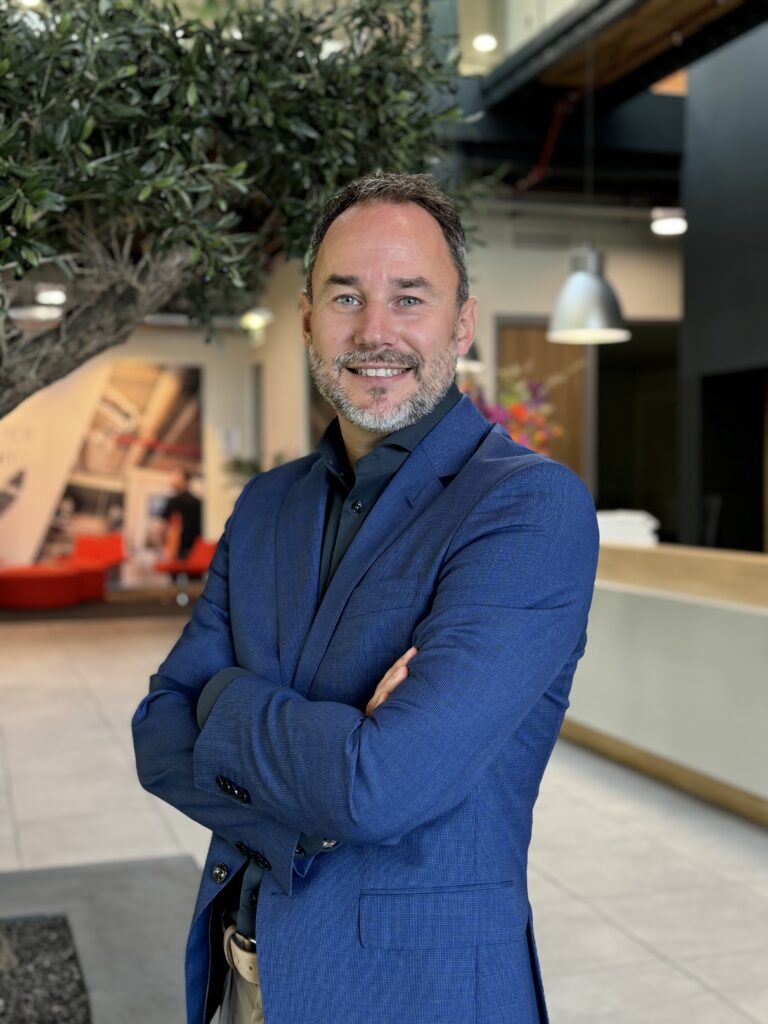