Custom aluminium extrusion supplier
High-end custom aluminium profiles with a maximum dimensional tolerance of ±0.02 mm.
Freedom of form in the design process
Firstly, our production process offers our customers a lot of design freedom. Designers can ignore almost all restrictions and standards: at Mifa, you can think in terms of possibilities instead of limitations. Here are some examples of extrusion profiles that Mifa can produce.
Great precision and a high level of detail
Secondly, Mifa excels in producing bespoke aluminium profiles with great precision and a high level of detail. Thanks to our state-of-the art machines we are able to produce thin-walled aluminium profiles with the most complex shapes and with a maximum dimensional tolerance of ±0.02 mm.
• Wall thicknesses from ±0.25 mm;
• Profile weight from 0.003 kg/metre tot 10 kg/metre;
• Profile dimensions from Ø 3 mm to Ø 180 mm / 220 x 60 mm.
Our experts will be happy to advise you based on your needs and requirements.
Economically advantageous
Mifa’s custom-made aluminium profiles are also economical. Our efficient aluminium extrusion process saves money compared to many other production techniques. Moreover, the cost of an extrusion die is relatively low. So our custom aluminium profiles save you time and money.
Advantages of custom aluminium extrusions in brief
- Freedom in design;
- Great precision and a high level of detail;
- Economically advantageous;
- Low minimum order quantity;
- Wide range of different (custom) aluminium alloys;
- High material strength and wear resistance;
- Co-engineering.
Driving progress together: Mifa’s autonomous excellence in the Aalberts family
Mifa is part of Aalberts, a stocklisted company that has been pioneering technology since 1975. Aalberts develops mission-critical technologies for both groundbreaking industries and everyday applications, enhancing business performance while promoting environmental sustainability.
Known for its entrepreneurial spirit, the Aalberts culture, called ‘the Aalberts way’, emphasizes winning with people, taking ownership, and pushing boundaries. As an autonomous entity within Aalberts, Mifa benefits from a financially stable framework that fosters innovation and growth.
With over 16,000 employees and operations in more than 50 countries, Aalberts provides a robust platform for continuous development and embracing cutting-edge technologies.
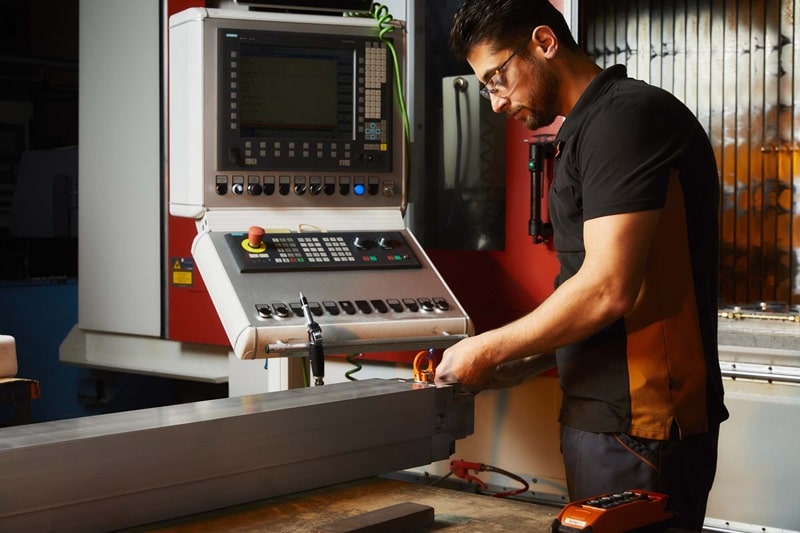
One stop-shop
Mifa takes full responsibility for the development and production process of the profiles. Our knowledge and experience in precision extrusion, machining, assembly and all other techniques we master, guarantee an optimal product. Mifa is therefore a one-stop-shop for customers. The techniques below are at our disposal:
- Precision extrusion;
- Machining;
- Assembly;
- Aluminium surface treatments;
- Magnesium technology;
- Other techniques: bonding, welding, marking, engraving and laser processing, bending and pre-treatment.
With our extensive knowledge and years of experience, we use the right technology for each product. A technique that is particularly interesting for our customers, is surface treatment.
6xxx family
EN AW 6060 (Al MgSi)
EN AW 6063 (Al Mg0.7Si)
EN AW 6005A (Al SiMg(A))
EN AW 6061 (Al Mg1SiCu)
EN AW 6082 (Al SiMgMn)
EN AW 6463
7xxxx family
EN AW 7020 (Al Zn4,5Mg1)
EN AW 7022
EN AW 7075 (Al Zn5,5MgCu)
1xxx family
EN AW 1070
2xxx family
EN AW 2024 (Al Cu4SiMg1)
3xxx family
EN AW 3003 (Al Mn1Cu)
Magnesium extrusions
Mifa has mastered the production of high-quality magnesium profiles and components, achieving tolerances as tight as 0.02 mm, similar to aluminium. Magnesium offers the same design flexibility as aluminium but with added benefits.
Key Advantages of Magnesium:
- Lightweight: Magnesium is up to 30% lighter than aluminium and 70% lighter than steel. This weight reduction is crucial for products like bicycles, cars, and airplanes, enhancing performance and user experience.
- Cost Efficiency: Lighter components reduce production, handling, and operational costs in industries like automotive, aerospace, and transportation.
- Durability and Corrosion Resistance: Mifa’s advanced coating technology prevents corrosion, ensuring magnesium remains strong and durable. Its high strength-to-weight ratio makes it an attractive alternative to heavier metals.
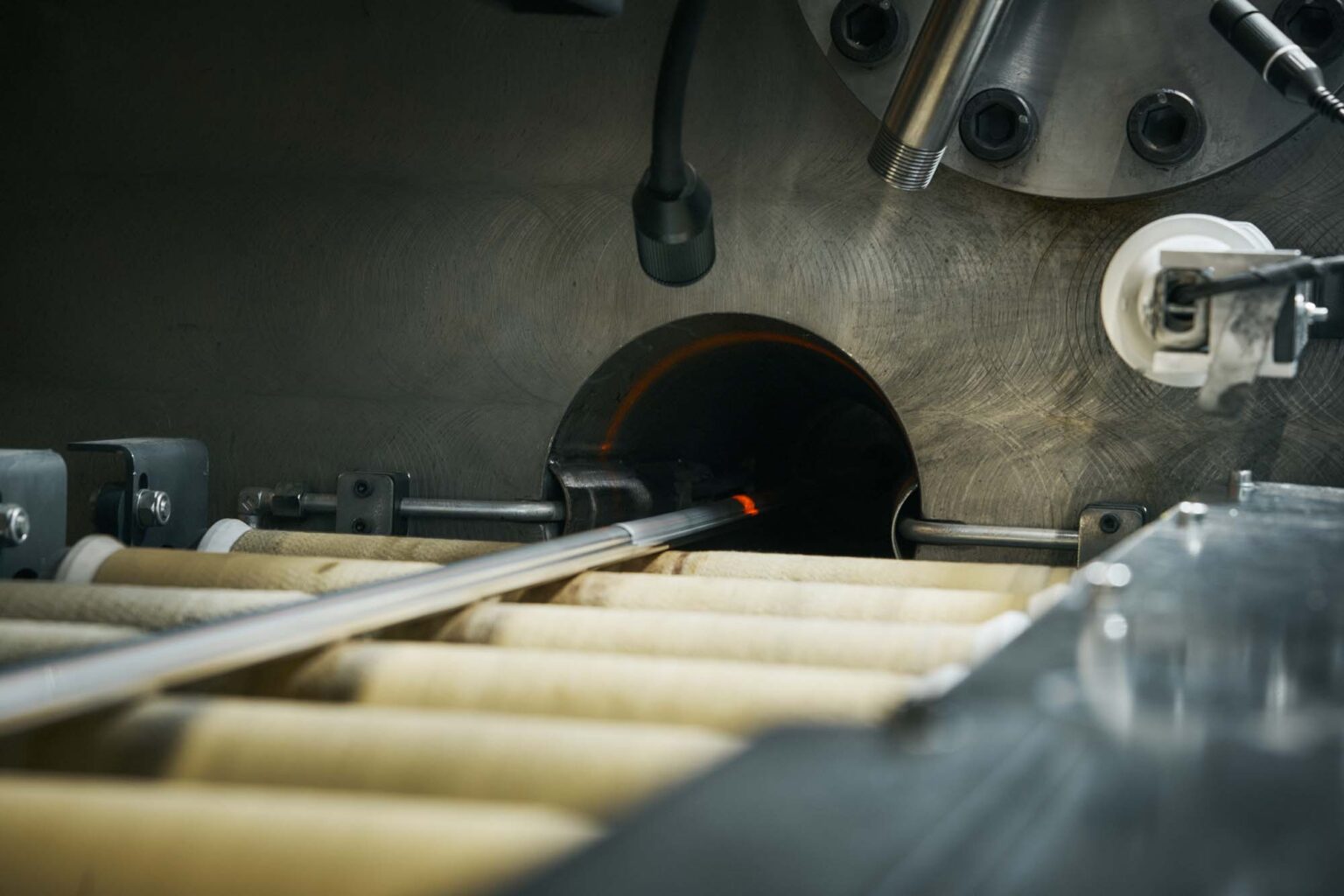
Sustainability: a top priority
In addition to supplying high-quality extruded aluminium profiles, Mifa attaches great importance to sustainability. For example, we have our own recycling centre where we separate our raw materials.
Mifa received the silver EcoVadis award in May 2025. With EcoVadis, we measure our progress in the areas of sustainability and corporate social responsibility. This recognition puts us in the top 15% of all companies assessed. EcoVadis is the market leader in assessing the sustainability of hundreds of thousands of companies.
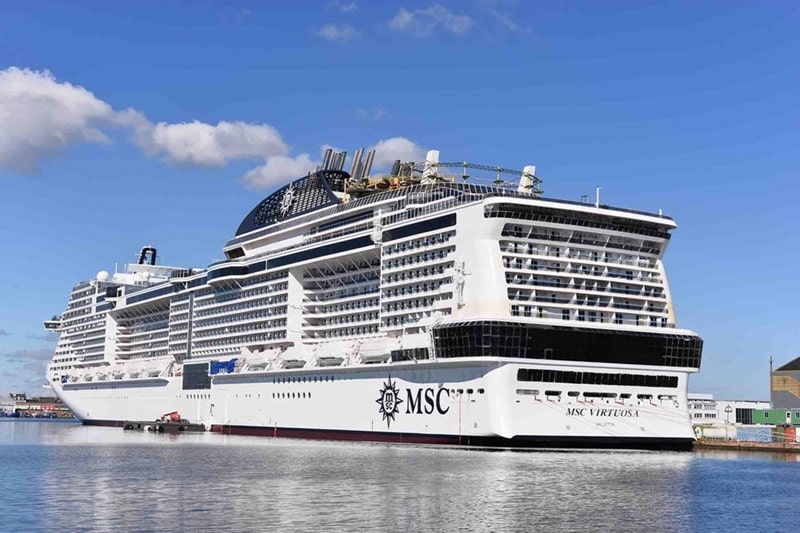
Custom aluminium extrusions for Chantiers de l'Atlantique
Because Mifa produces custom profiles with high accuracy (up to ±0.02 mm), our profiles are being used in various markets. However, what might come as a surprise, is that our extrusion profiles are also being used for one of the biggest cruise ships in the world (a ship that’s 331 meters long and 43 meters wide).
The profiles were produced for Chantiers de l’Atlantique, one of the world’s largest innovative shipbuilders. Our technical engineers worked together with the engineers at Chantiers de l’Atlantique to work out an ingenious concept. Curious to learn more? Read the full case study for all details.
Modernization of double-deck trains
NedTrain is aiming to refurbish its renowned double-decker trains. This entails a complete disassembly of each train, followed by reassembly. Mifa provides custom aluminium extrusion profiles for this process. Since many of these profiles are positioned under the floor, they are either partially seen or entirely hidden.
This project is subject to a European tender process, allowing any company to bid for this public contract. Out of all the participants, Mifa was eventually selected for the task. A primary factor in this decision was that Mifa possesses all the necessary technologies in-house for Nedtrain’s initiative. These include:
- Extrusion
- CNC machining
- Bending
- Engraving
- Surface treatment
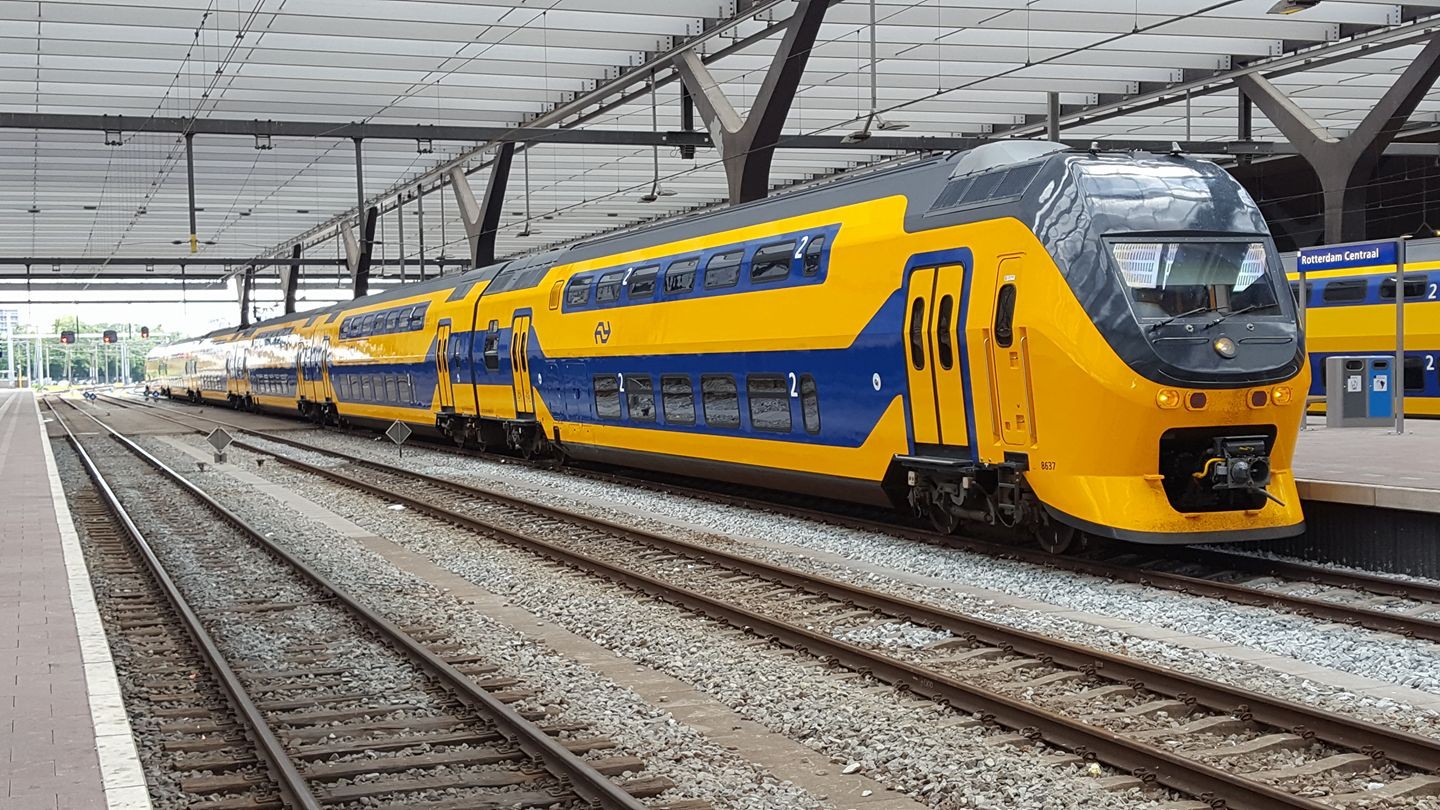
Medical precision profile for new product B|Braun
In another case study, Mifa developed a medical precision component in collaboration with B|Braun. B|Braun produces light, small customised medical devices and solutions. Braun contacted us for the development of their next generation infusion pumps: the new Perfusor® Space.
By offering their engineers more freedom in the design process, we were able to jointly develop the product our client was looking for. This enables us to guarantee the highest quality, at a lower cost and shorter lead time.
Are you currently looking for a custom aluminium extrusion supplier? We are one of the most advanced extruders worldwide. Wondering how we help our customers to reach their goals? Take a look at the other case studies for more details.
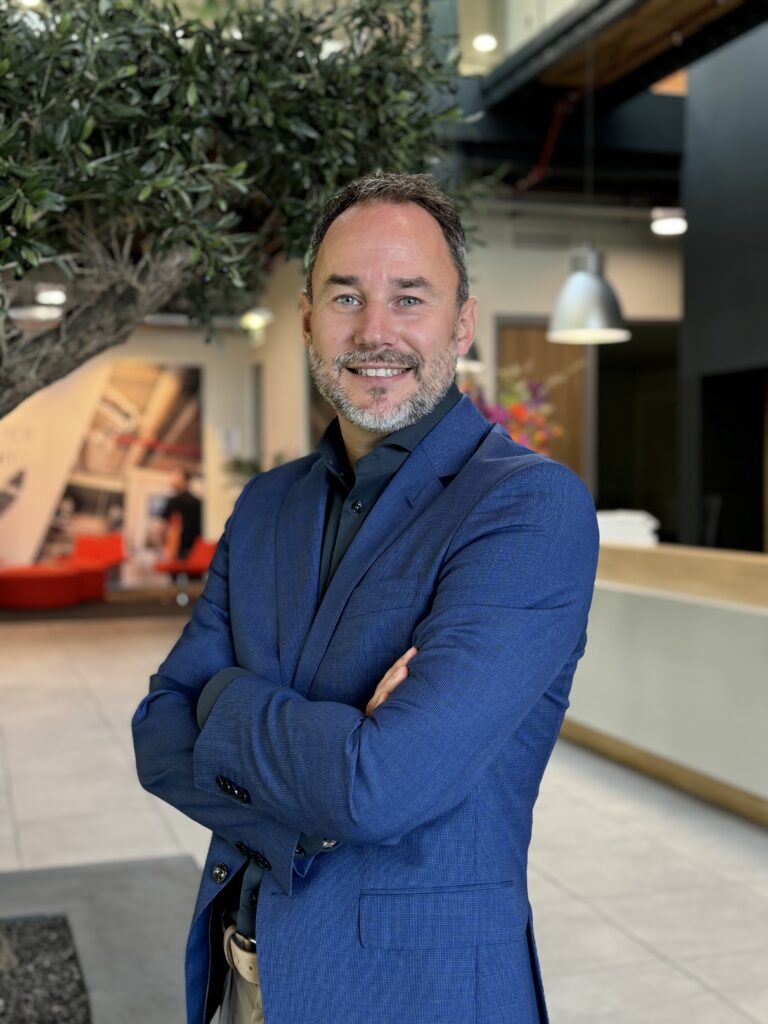