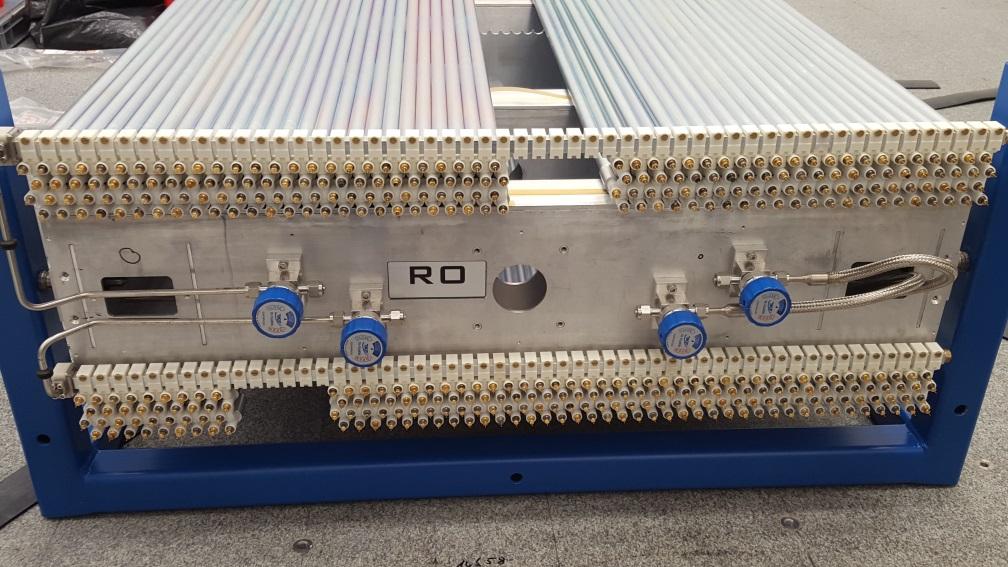
Muon spectrometers for experiment of CERN
A new generation of spectrometers for the research of a pioneering institute.
Unprecedented precision in the new generation of spectrometers.
“The new drift tubes have a diameter of 15 mm, only half of the earlier models. The signals can now be read within 200 nanoseconds, which is four times faster than before. This means that the drift tubes and their electronics are exposed to neutron and gamma radiation, which is ubiquitous in the ATLAS detector, for less time – and therefore can react to muons 10 times faster,” explains Dr. Hubert Kroha, project leader at MPP.
An essential contribution to the high spatial resolution is provided by the incredible mechanical precision of the muon chambers. During the construction of the chambers, the positions of the counting wires in the middle of the drift tubes are assembled with an accuracy of 5 micrometers. For comparison, a human hair is about 100 micrometers thick.
These extruded aluminium tubes have very high demands regarding thin wall thickness (0.4 mm), roundness, and concentricity within 0.1 mm, and low surface roughness, all of which are far beyond regular standards. There were concerns about the feasibility of producing such tubes.

Mifa delivers unparalleled precision
At Mifa, everything revolves around knowledge and technology. With our extensive machinery and expertise in aluminium and magnesium profiles, we produce the most accurate profiles. In collaboration with the Max Planck Institute for Physics, we worked on the ATLAS Detector Project at CERN Geneva. A project where Mifa’s precision extrusion with tolerances of ±0.02 mm and very thin wall thickness provides the Max Planck Institute for Physics with unprecedented possibilities.
The ATLAS project requires unparalleled precision for all components. Specifically for this reason, the Max Planck Institute for Physics chooses to have the aluminium profiles made at Mifa. The design requires a wall thickness of 0.4 mm, with minimal tolerance. Common standards for the extrusion of aluminium profiles often allow deviations of ±0.15 mm. Mifa can extrude with an accuracy of ±0.02 mm. This was the reason why the Max Planck Institute for Physics chose Mifa as a partner for this challenging project.
Surface treatments for special purity
In addition to the precision that Mifa provides, there is another reason why the Max Planck Institute for Physics chose Mifa. To protect the aluminium profile, the product undergoes a surface treatment. The surface treatment is a chemical processing of the metal surface. The layer applied to the profile, called Surtec, ensures, among other things, that the profile is protected against corrosion.
At Mifa, we not only have expertise in machining, precision extrusion, and assembly, but thanks to the fully automated large and small production lines of Mifa Surface Treatment, we are capable of taking full responsibility for the entire surface treatment process. This ultimately saves time and costs in the overall process.
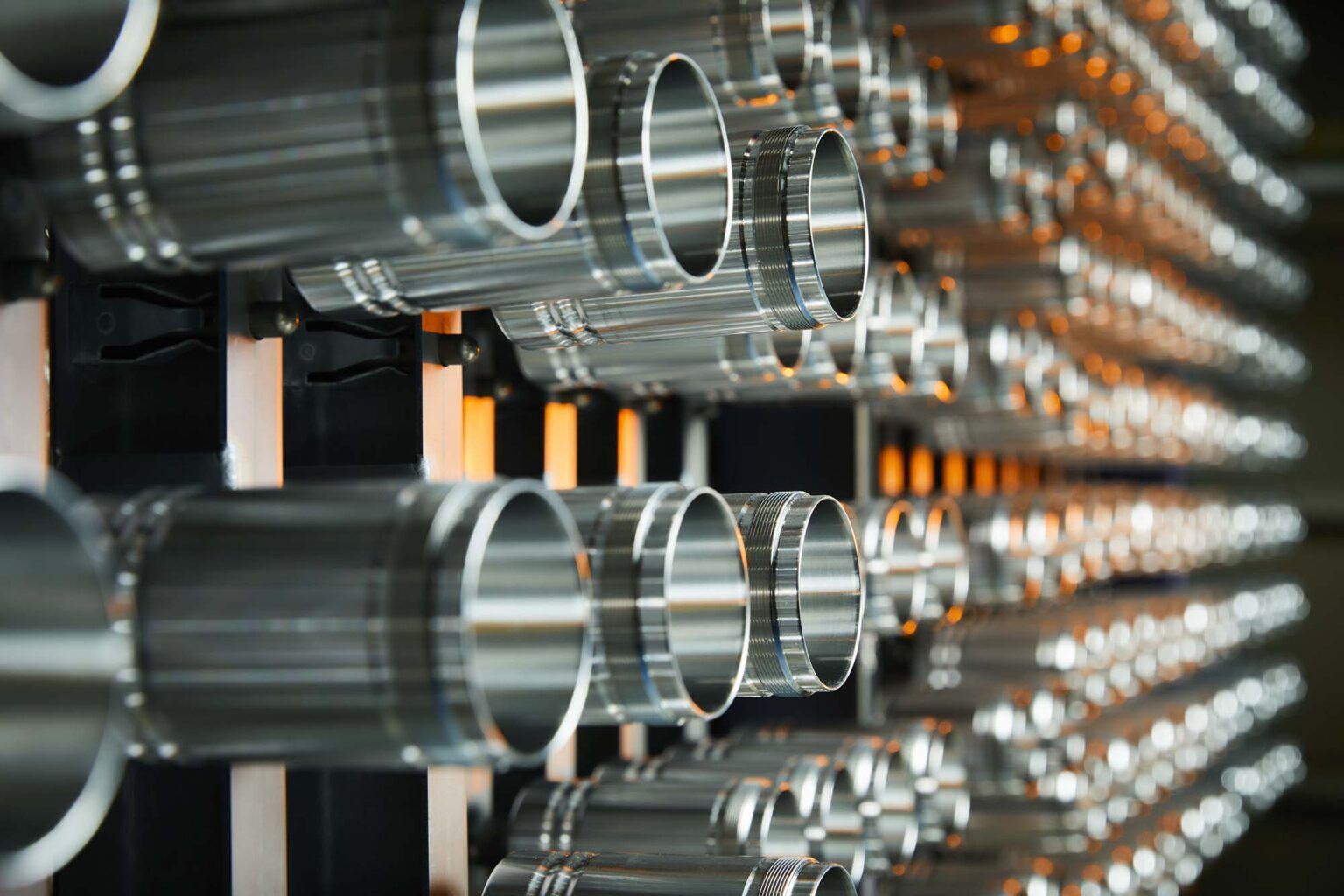
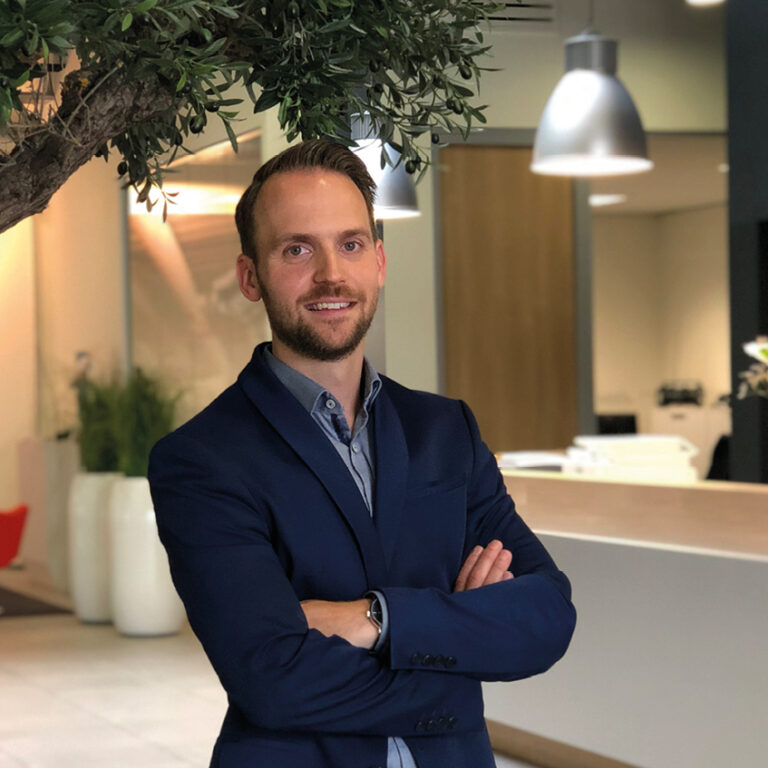
Innovative extrusion profiles for 3D printer of Rapid Shape
Innovative extrusion profiles for 3D printer of Rapid Shape
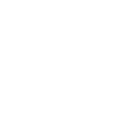
High performance cosmetic requirements in aerospace
High performance cosmetic requirements in aerospace