Aerospace: high-quality standards
Lightweight aluminium profiles with high-quality, consistent standards
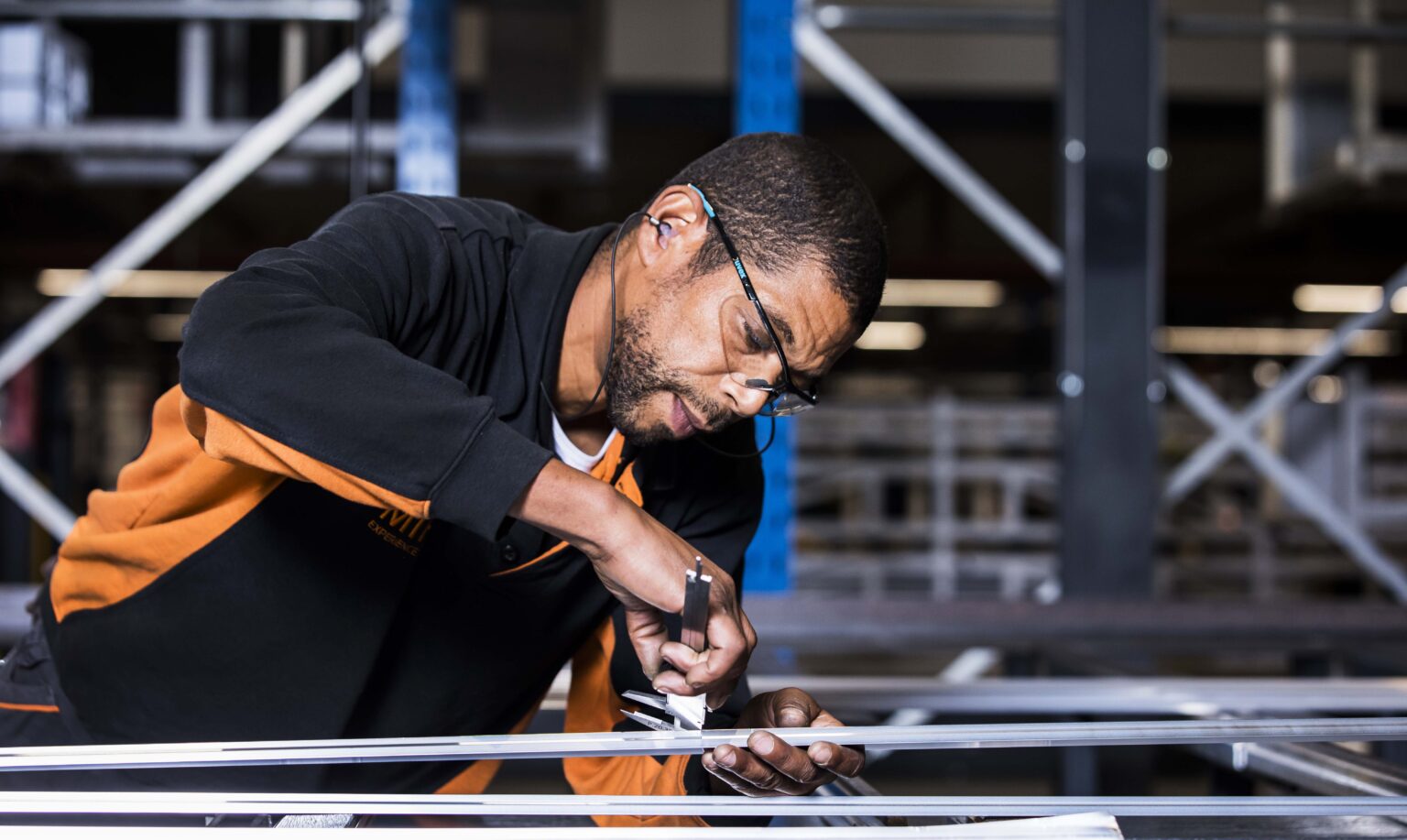
Precision extrusion in the aerospace industry
EN-755-9 and EN-12020-2 are the common standards for the extrusion of aluminium profiles. They allow deviations of +/- 0.15 millimeters or more. Mifa goes beyond that through our precision extrusion technology, which can achieve accuracy up to 0.02 mm. Thin-walled lightweight profiles, post-processing such as surface treatments and assembly, and automation make Mifa unique as a supplier for the aviation industry, all under one roof with deliveries in large volumes.
Our high quality profiles are also being used as high end components in other demanding markets. Medical precision components are a good example.
Sustainably responsible through lightweight profiles
In various markets, it is essential for components to be strong and light. This also applies to the aviation industry, as well as the aerospace market. More and more aviation manufacturers are therefore exploring the possibilities of aluminium in aircraft to reduce CO2 emissions, among other benefits. By providing sustainable solutions that can help reduce CO2 emissions, we aim to have a positive impact on environmental challenges. Our EN AW 6061 and EN AW 6082 alloys for thin-walled extrusion profiles are a prime example of our commitment to sustainability. These alloys not only save material and costs but also contribute to a cleaner air transport system.
The production of thin-walled extrusion profiles offers several advantages for the aircraft and aviation industry. They are significantly lighter than traditional materials, reducing fuel consumption and CO2 emissions. The EN AW 6061 and EN AW 6082 alloys provide excellent strength and corrosion resistance, making them perfect for aerospace applications.
At Mifa, we have made significant progress in controlling temperature, flow, and die technology for our alloys. This allows us to achieve tight tolerances for dimensions, torsion, and straightness, meeting the rigorous aviation standard EN 755-9
Aluminium components for the defense market
Within the aerospace sector, Mifa produces and supplies microwave components to various leading manufacturers of radar systems around the world.
Thanks to our precision technology, we can machine products on all sides, apply MIL-SPEC surface treatments, and assemble components into a complete product. We do this for, among others, the following products in the defense market:
-
Waveguides
-
Wing components
-
Drones
-
Electronic enclosures
Download our waveguides brochure for more information
Vertical integration
Thanks to our technology, knowledge, and experience, we can produce the most complex shapes of aluminum at Mifa. We can manufacture these complex shapes into a qualified end product using various techniques. We offer a complete in-house package through techniques such as:
- Extrusion;
- Brushing;
- Robotics;
- Belt grinding;
- Bending;
- Assembly;
- Surface treatments.
We can realize complete components for our customers because we write our own software and create molds for CNC machines. Each profile requires a specific machining method, especially if it is a visible surface. Our engineers use CAD/CAM programs like Solid Works, Solid Edge, and Unigraphics for this purpose. By involving our engineers in the development phase, we can provide advice and make the production process more efficient and faster. At Mifa, we are happy to take complete responsibility for your product.
Automation of processes
At Mifa, we focus on transforming business processes through advanced automation and robotics. These technologies can provide strong benefits, and we can achieve this through the extensive experience and expertise of our colleagues.
Robotics can make business processes more efficient. Our machine park is designed to load machines, process products, and perform automatic measurements. We strategically employ co-robotization to take over repetitive and strenuous tasks. This way, both colleagues and robots can excel in tasks that require a human touch.
Quality and consistency are crucial concepts in the aircraft and aviation industry. Through (co-)robotization, large volumes can be delivered with consistent quality.
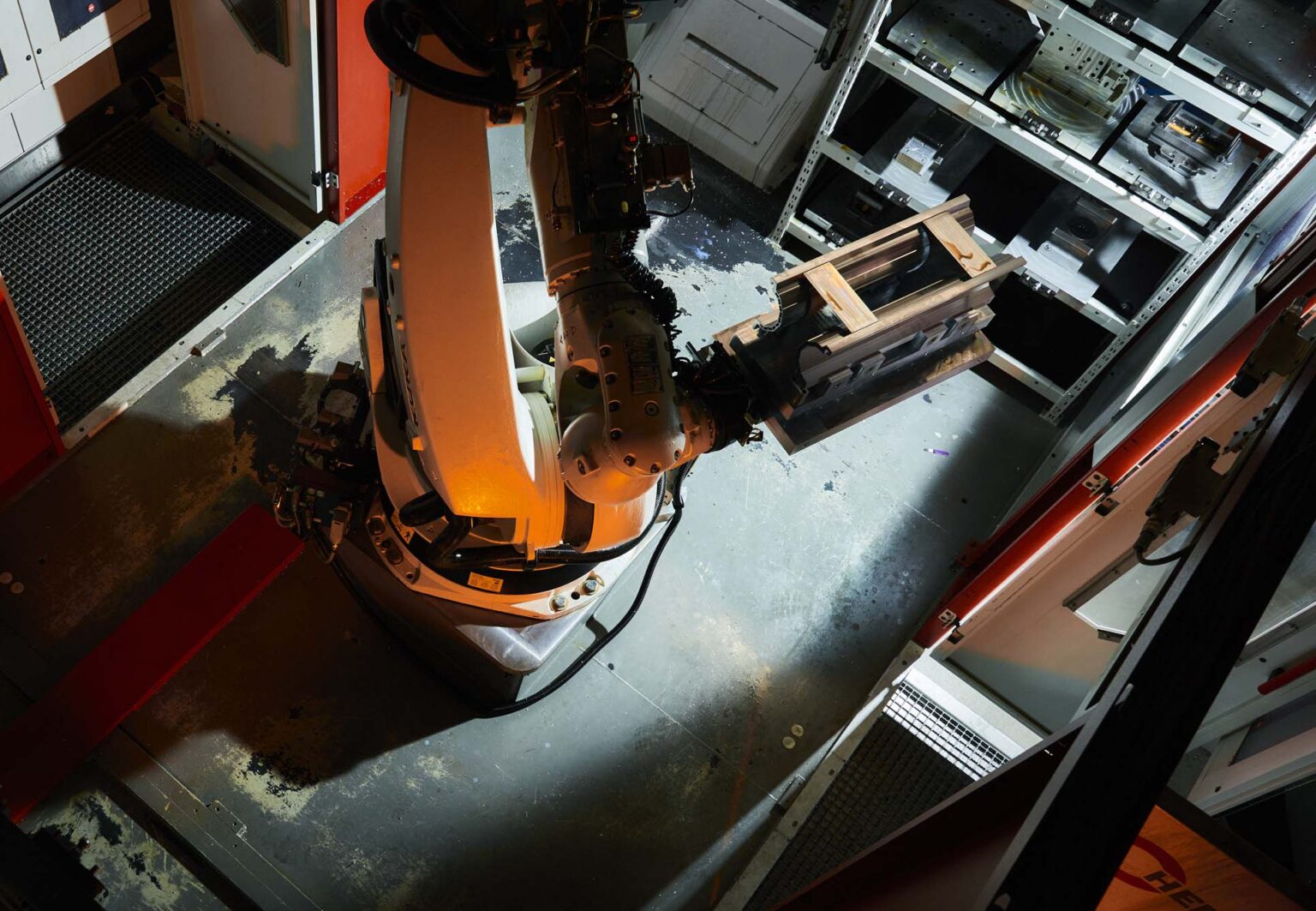
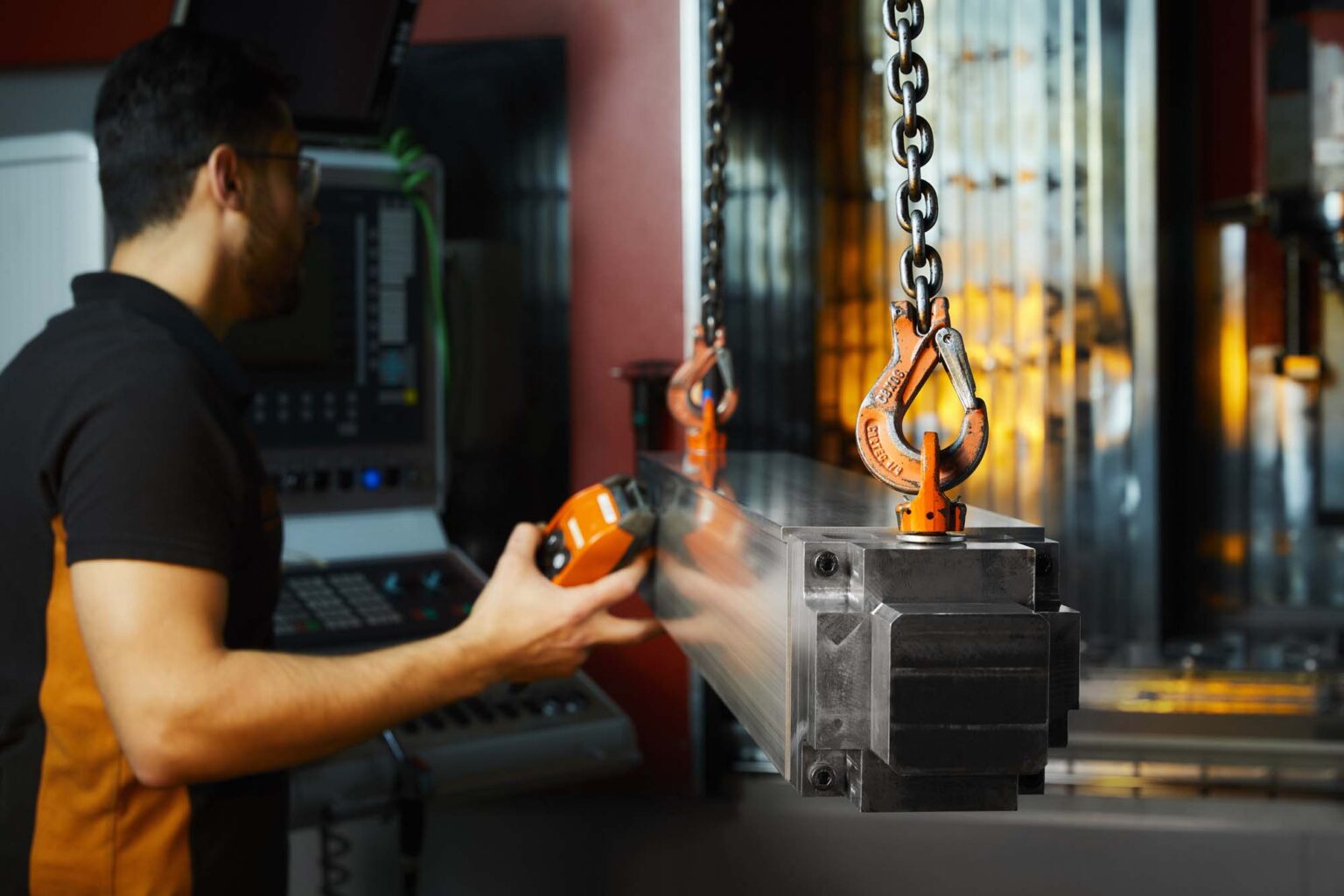
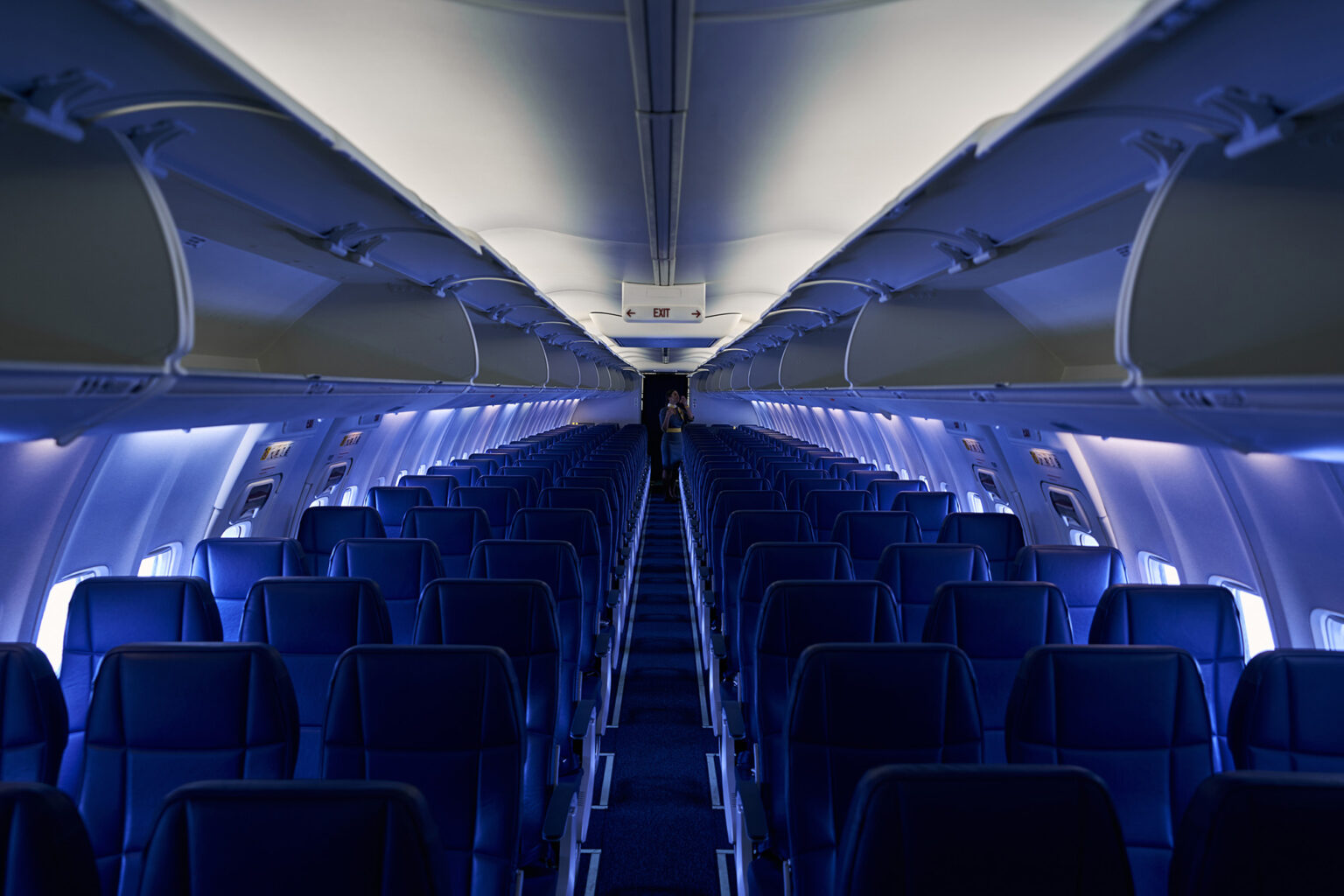
High quality for various components
Mifa produces high quality extrusion profiles for customers such as Airbus and Collins Aerospace. We can offer these extrusion profiles via a diverse range of techniques. Together with our aerospace customers, we develop extrusion profiles and components for:
- Kitchens and trolleys;
- Instruments;
- Lighting;
- Seats;
- Toilets;
- Radar components;
- Luggage compartments.
As an added customer benefit, we at Mifa focus on various cosmetic requirements. For this, we have special processes to continuously realise the cosmetic importance of our profiles.
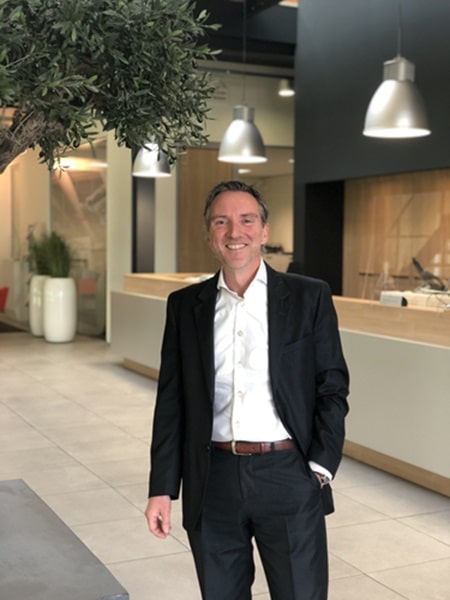