
50 years of Mifa: interview Hans
The heart of precision extrusion: the story of a true Mifa precision hero
From the former LTS, where Hans Niessen studied mechanical engineering, he found his way to Mifa Aluminium. At school, he learned about aluminium as a metal, but one thing you don’t learn in school is precision extrusion. That is a technique you master on the job. And after nearly 40 years at Mifa, Hans has become a true expert in his field. From the moment a profile goes into production to the next step in the process, Hans oversees everything and steps in where needed.
Continuous innovation: magnesium as a replacement for extrusion profiles
Over the past 40 years, Hans has held various roles at Mifa. He started in the extrusion department, then worked for several years in the technical service, before returning to the extrusion department, where he now serves as Extrusion Technology Officer. As the expertise of Mifa’s staff grew, so did Mifa’s innovation. Precision extrusion is a technique you only truly know if you work at Mifa; we have the expertise in-house – it’s at the heart of our colleagues.
Hans contributed to this innovation as a knowledge carrier of extrusion, playing a central role in several projects. One of these projects involved magnesium technology – a technique that continues to make us unique in the market to this day. Both magnesium and aluminium are metals, but each has its own strengths – and therefore requires different processes. “Together with our colleagues Chris, Theo, and Aart, we developed the magnesium technology and presented it to one of our oldest clients. It would turn the aluminium world upside down – but not every client is ready to embrace magnesium,” says Hans.
Magnesium is a lighter and more wear-resistant metal than aluminium. It is more expensive, and its possibilities are not as vast as aluminium’s, but there is still a lot that can be done. “Our client was looking for a component for a machine that needed to be wear-resistant. We previously made it with aluminium, but we took on the challenge of extruding magnesium with full courage – and expertise. To this day, we are still making these magnesium components for the same client.”
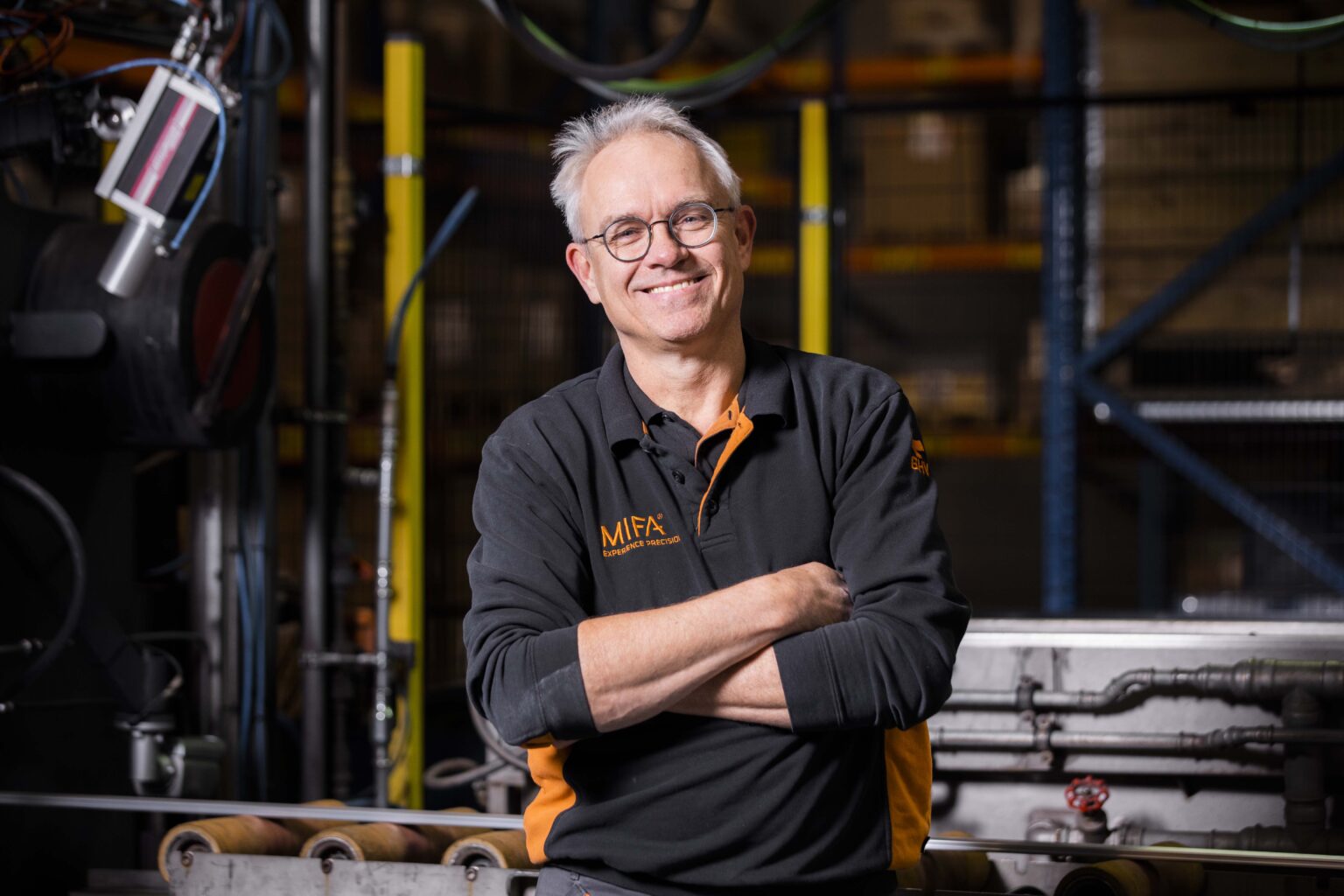
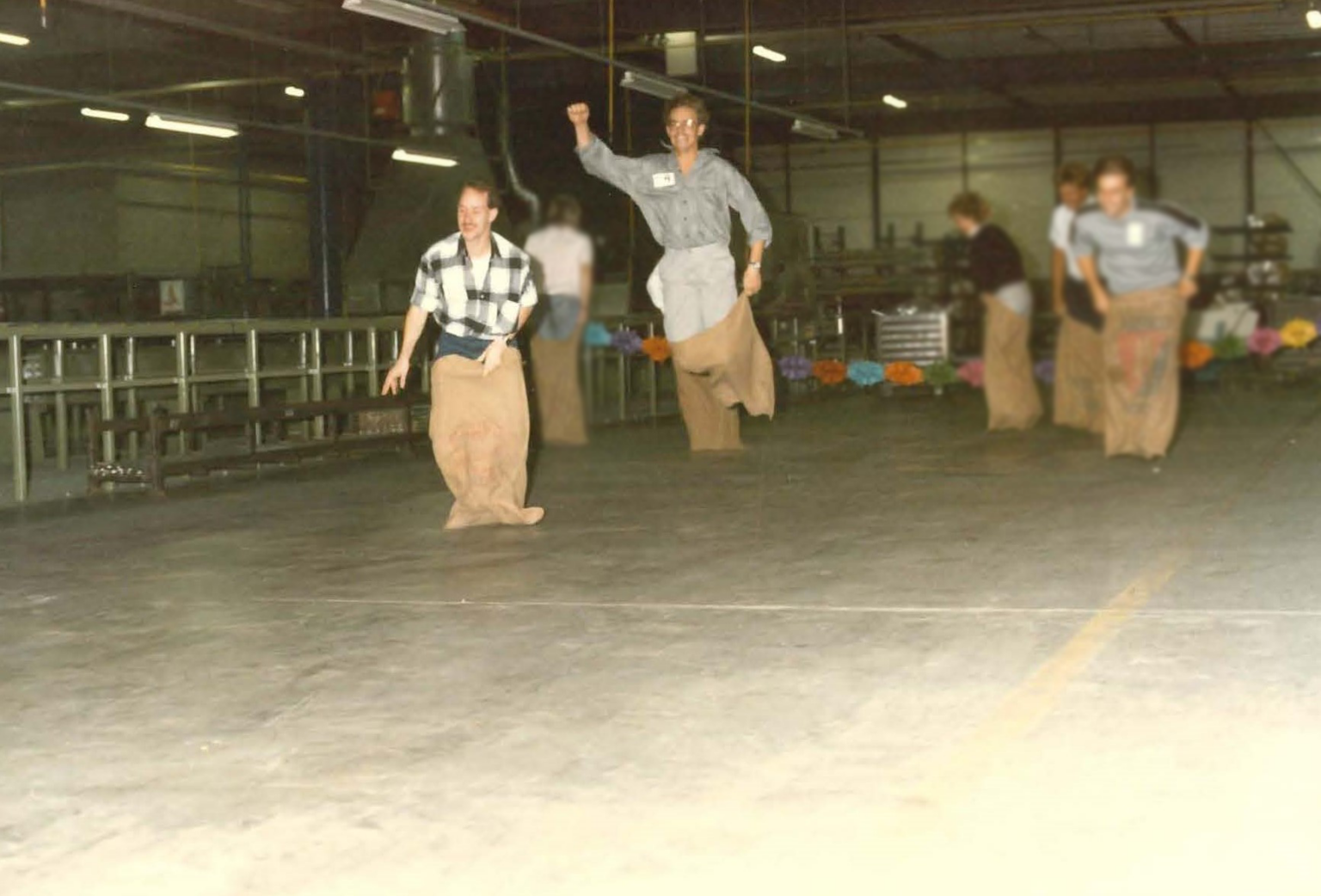
Colleagues Jan and Hans have been working at Mifa for over 40 years
Taking the lead in technology
“What Mifa has in-house, others do not. Mifa has the entire supply chain in-house, and that with high quality.” This quality was guaranteed in 2013, when we were officially qualified to supply Airbus. Extrusion profiles that make airplanes rise and safely land; Mifa gets to contribute to that. Since 2013, we have been supplying profiles to Airbus and have been AS9100 certified – a certificate we worked hard for and have received again every year since.
“Achieving the qualification was not without its challenges. It took a lot of time and effort, and many colleagues from every department had to put a lot of energy into it. Back then, almost no one understood why we had to put in so much effort – what were we really achieving?”
Taking the lead in technology are the words of Mifa’s founder, Mr. Jan Aalberts. Words that Hans still lives by every day. The AS9100 qualification was a major step in innovation, both for the colleagues and the company. All documentation had to be automated, and we got computers on the machines. “You can hardly imagine it, but before that, everything was on paper.” These innovations, along with the hard work of our colleagues, continue to ensure that we supply unique profiles to the biggest brands, contributing every day to a sustainable and safe world – the reason why Hans still works at Mifa with pride after 40 years.
50 years of Mifa: making dreams come true
Over 50 years ago, we laid the first building blocks for the power of precision. The power of precision extrusion to make dreams come true. We are part of the very latest technologies – technologies that enable us to detect diseases earlier, achieve faster internet, and make travel more environmentally friendly.
Innovative extrusion profiles for 3D printer of Rapid Shape
Innovative extrusion profiles for 3D printer of Rapid Shape
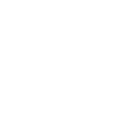
High performance cosmetic requirements in aerospace
High performance cosmetic requirements in aerospace