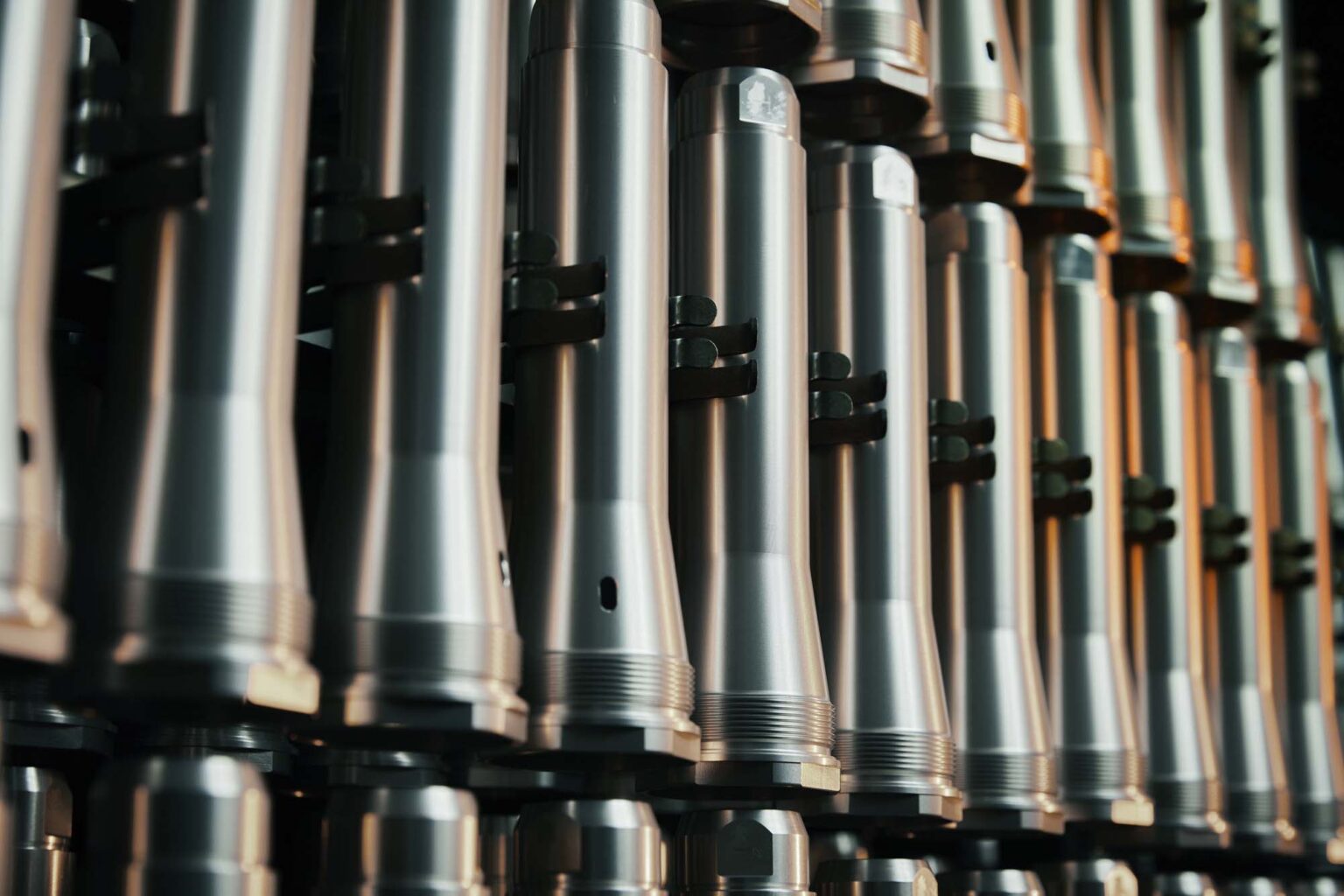
Discover the possibilities of magnesium extrusion
Mifa offers an alternative to aluminium extrusion profiles in the form of magnesium extrusion, which is lighter and stronger than aluminium.
Mifa as a magnesium extrusion company
Around the year 2000, Mifa’s engineers began the initial experiments with magnesium extrusions and conducted feasibility studies. At that time, magnesium was not deemed cost-effective. However, with the advent of various new techniques and possibilities, we revisited the research years later. This time, it turned out to be financially interesting.
One of our first magnesium products was a component for a weaving machine. Because this component was lighter than the original, the machine was able to produce faster.

Extruded magnesium profiles as a lightweight solution
After years of extensive research and development, Mifa is now able to extrude magnesium profiles with very tight dimensional tolerances starting from +/- 0.02 mm, in addition to custom aluminium profiles. Magnesium is now available as an extrusion material for various markets where the combination of weight and strength is crucial. The design freedom is just as significant as with aluminum, and with the right coating, the product can acquire the properties needed for the intended application.
Magnesium profiles, components, and products are used in various applications, including:
- Lightweight mobility products
- Automotive, Defense, and Aerospace
- Machinery
- Sports & recreation
The magnesium process
Magnesium extrusion may initially seem similar to aluminum extrusion. Like aluminum extrusion, it starts with a block of raw material, which is pressed through a die shape at high temperatures, often using the same presses. However, the process is entirely different. Firstly, the temperature at which magnesium is extruded is very different. The boundary between too cold and too hot is thin and depends on the alloy.
Additionally, with magnesium extrusions, a different die is used. This is due to the structural differences between aluminum and magnesium. Aluminum has a cubic structure, while magnesium has a hexagonal one. Hexagonal material has more connections and is therefore more difficult to deform. This imposes different requirements on the die and the flow through the die—the transition from the round raw material to the profile must be very precise to prevent the material from coming out like a banana.
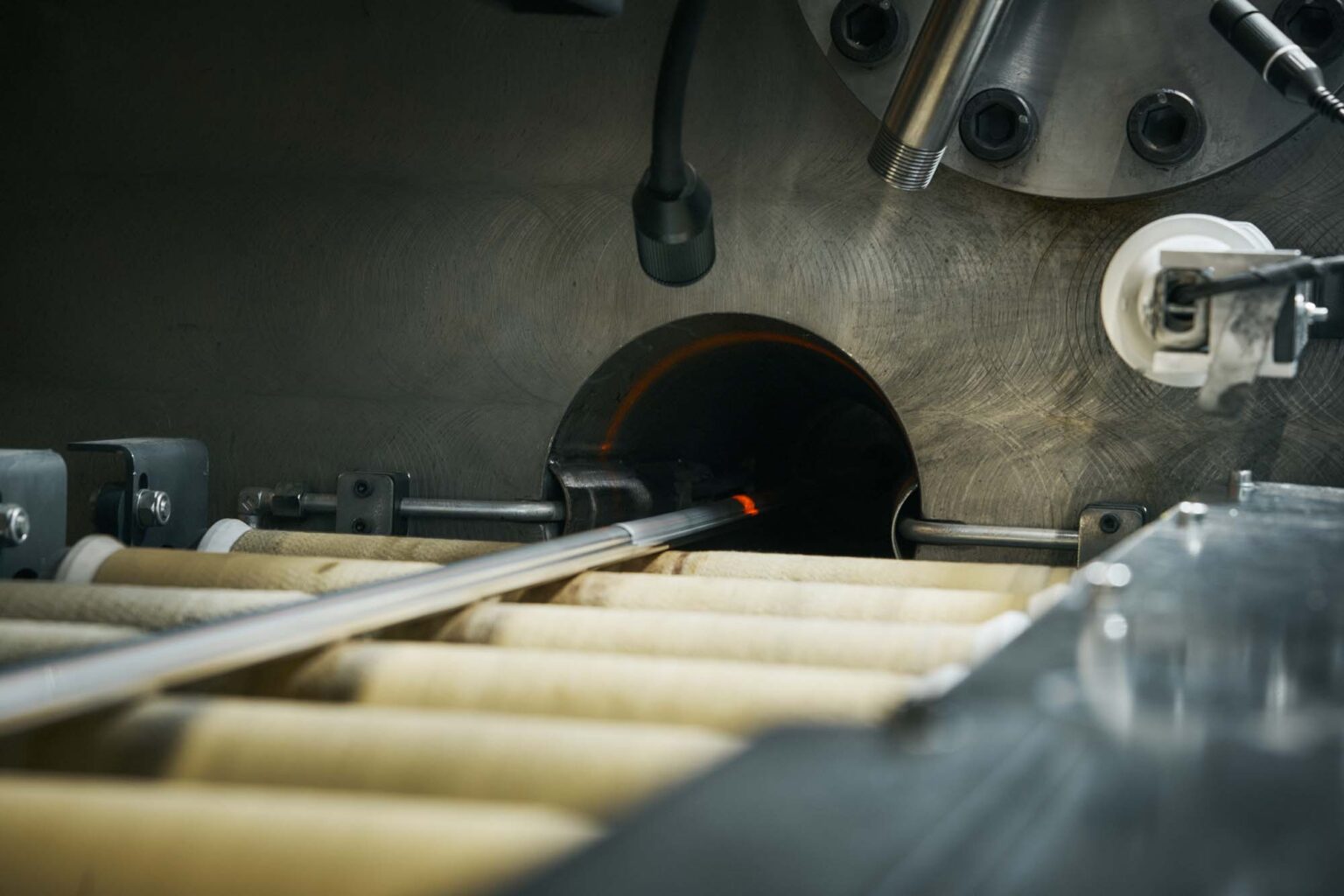
A magnesium extrusion company achieving cost savings
In recent years, at Mifa, we have continually improved the temperature control, flow, and die technology. This has significantly reduced the costs for magnesium profiles. It enables us to achieve high precision in dimensions, torsion, and straightness with magnesium in an economically viable manner. Specifically, we meet the extrusion standard for magnesium (ASTM B107M) in terms of torsion and straightness, and for dimensions, we achieve EN 755-9, which is a standard for aluminum extrusion that is stricter than that for magnesium. With tight tolerances, guaranteed mechanical properties, and extensive knowledge of magnesium surface treatment, we are unique in the world. Optionally, even in small quantities, we can produce a complete component for you.
Alloy | RM (mpa) | RP 0,2 (mpa) | A50 (%) | Hardness (hb) |
AI: 6063 – T6 | 215 | 170 | 6 | 70 |
AI: 6061 – T6 | 260 | 240 | 8 | 85 |
AI: 6082 – T6 | 310 | 260 | 8 | 90 |
Mg: AZ 31 – F | 250 | 180 | 15 | 49 |
Mg: AZ 61 – F | 310 | 228 | 16 | 60 |
The design freedom of extruded magnesium
With magnesium, designers have almost the same design freedom as with aluminium precision extrusion. The advantage of magnesium is that it is 35% lighter than aluminium, and magnesium is also stronger than the usual structural aluminium.
So, if you’re looking for a lightweight yet powerful material, extruded magnesium could be the solution. Mifa produces with two magnesium alloys, AZ 31-F (with 3% aluminium) and AZ 61-F (with 6% aluminium). Due to the higher aluminium content, the second alloy is stronger; this slightly affects design freedom. The drawback of magnesium products is that they are more expensive than aluminium—still, as demand increases, costs are likely to decrease. We are happy to advise you on aluminium versus magnesium and the right alloy for your product.
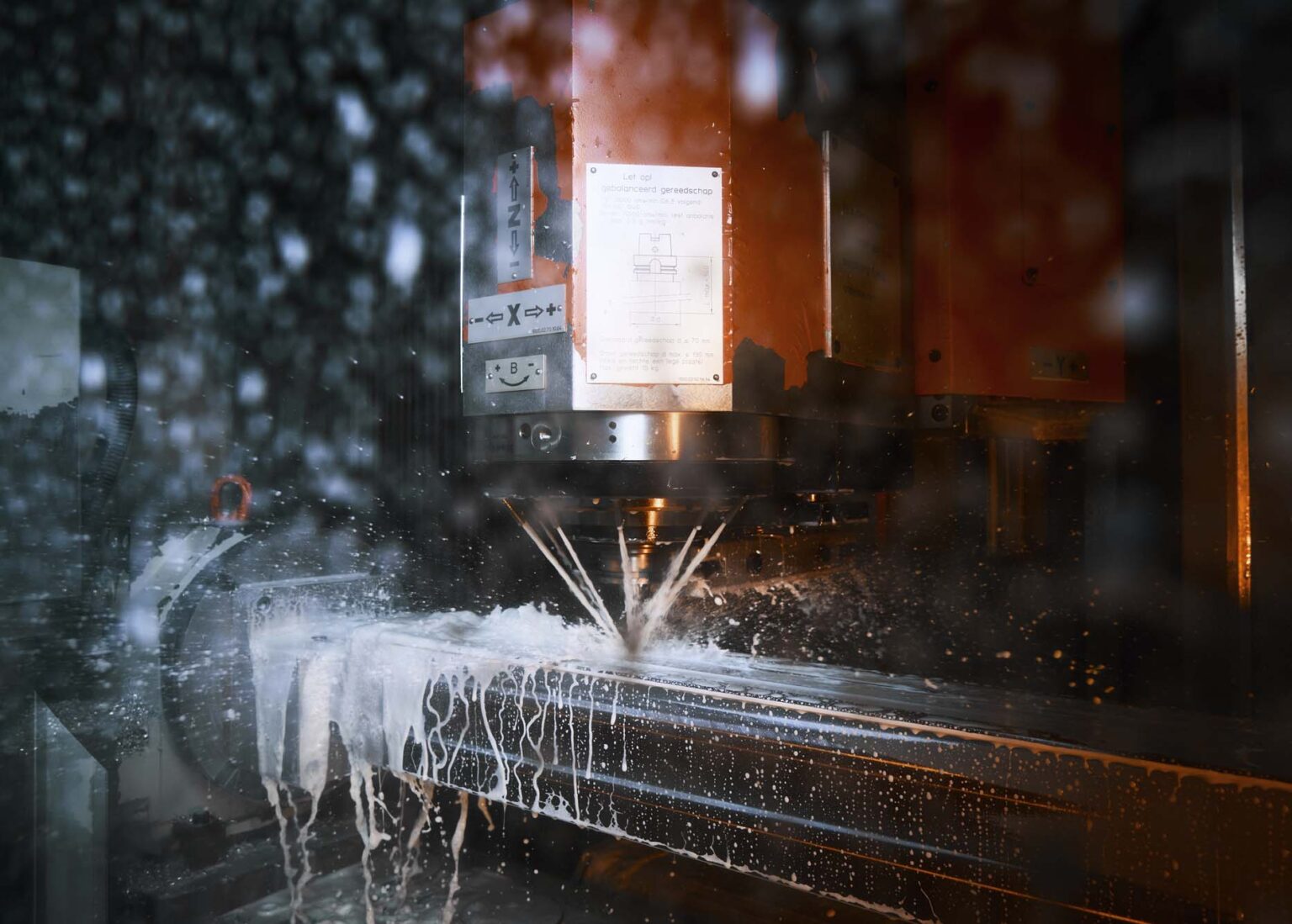
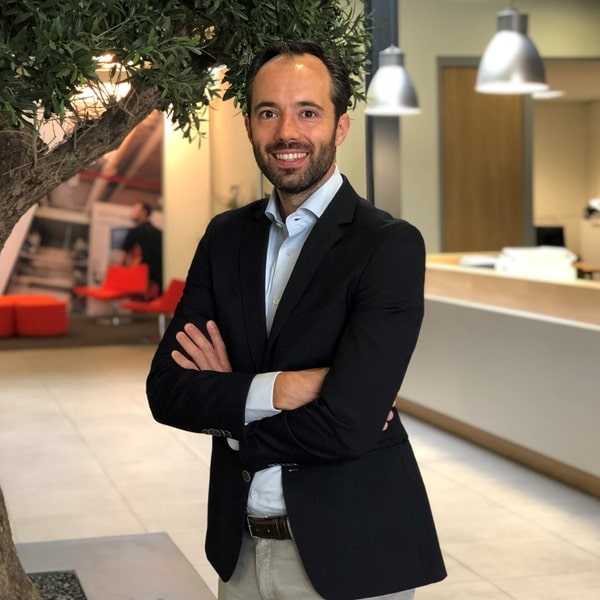