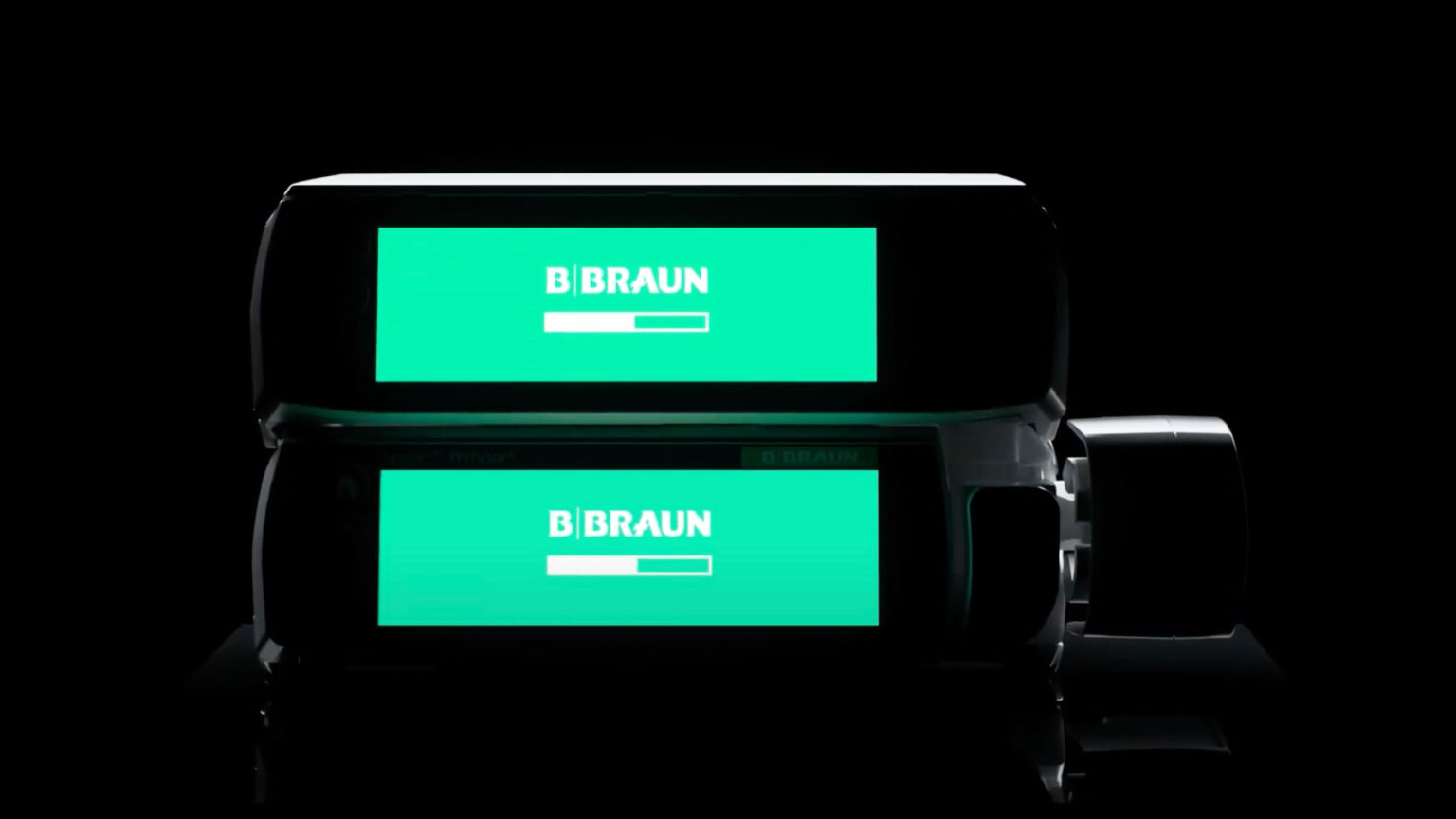
Medical precision profile for new product by B|Braun
Mifa supplies precision profiles for the Perfusor® Space infusion pump by B|Braun
B|Braun manufactures lightweight, small, customized medical equipment and solutions. These involve high-quality and cutting-edge technical solutions. One of these solutions is the infusion pumps. One of the products for which Mifa produces precision aluminium profiles is the infusion pump called Perfusor® Space.
These infusion pumps are used to administer medications and nutrition and are also employed for blood transfusions. The system consists of a large syringe that is mechanically controlled and monitored. This way, the patient receives an exact dose per unit of time.
For the next generation of B|Braun’s infusion pumps, the Spaceplus Perfusor®, the company was looking for digitization, a higher level of safety, reliability, and an extended lifespan.
Customer
B|Braun
Market
Medical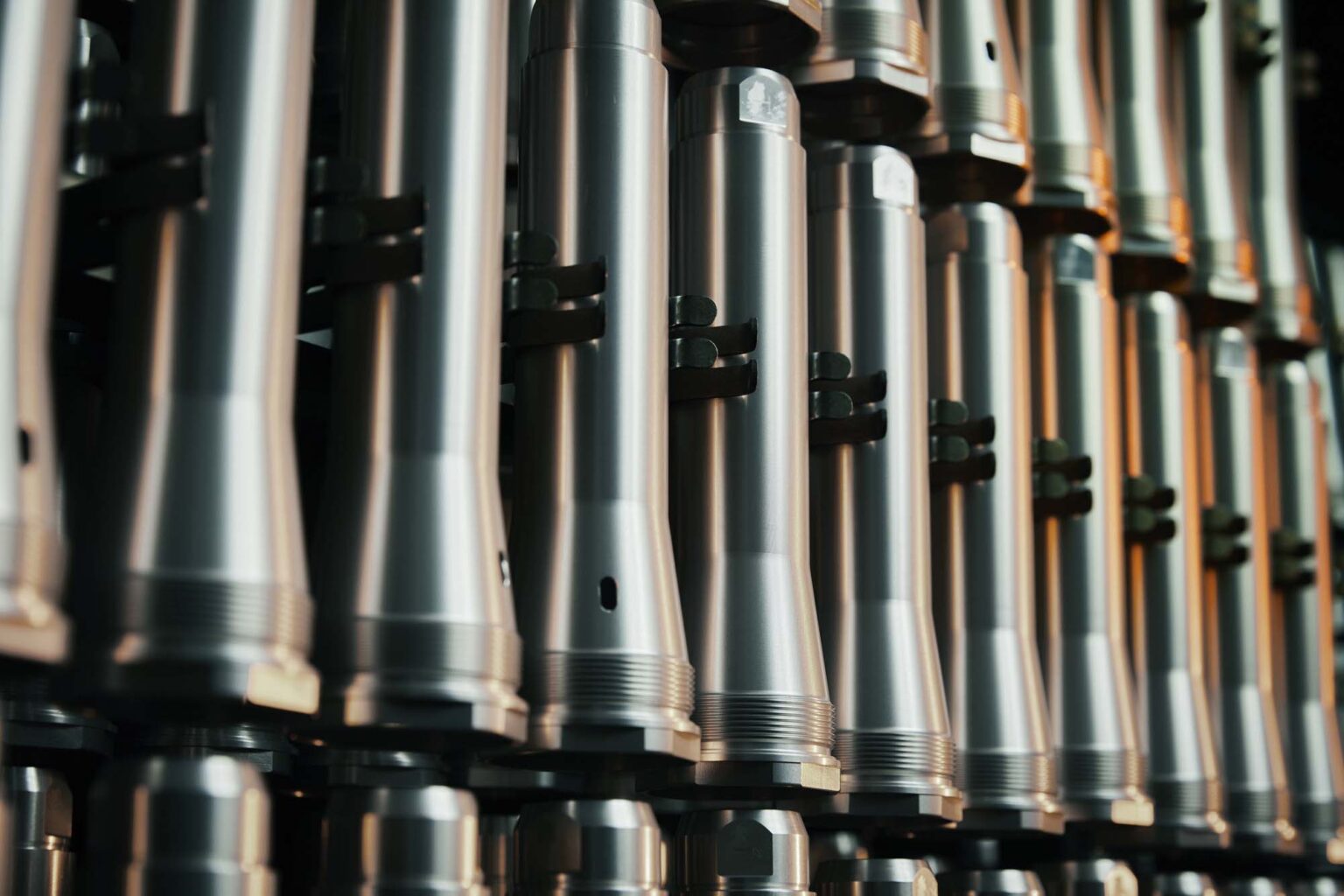
Surface treatment and other in-house treatments
In addition to the precision provided by Mifa, we protect the profile from external influences. With our in-house surface treatment line, we anodize the profiles. This means that we add an extra layer to the profile for protection against corrosion, for example. The customer benefits from our in-house expertise, allowing them to outsource the entire process to one partner for all profile treatments. Brushing, deburring, and machining of the profile are also carried out in-house at Mifa.
Overview of the techniques the profile has undergone:
- Extrusion
- CNC machining
- Surface treatment
- Brushing
- Deburring
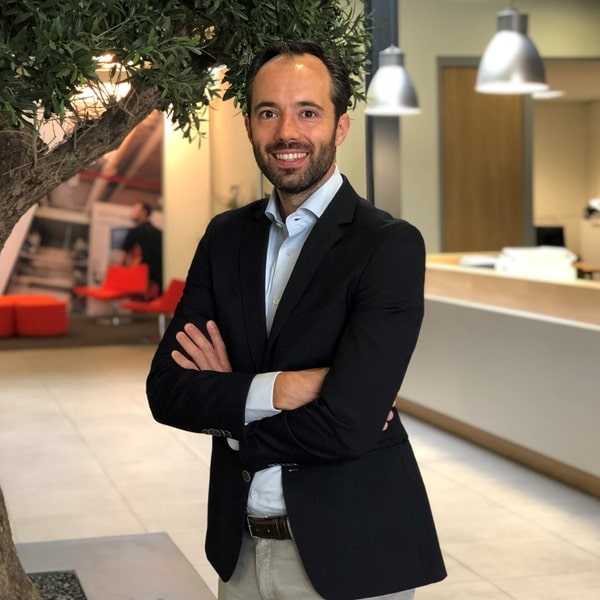
Take us along in the design phase of your product
Call or email Luuk
Area Sales Manager
Innovative extrusion profiles for 3D printer of Rapid Shape
Innovative extrusion profiles for 3D printer of Rapid Shape
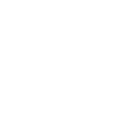
High performance cosmetic requirements in aerospace
High performance cosmetic requirements in aerospace