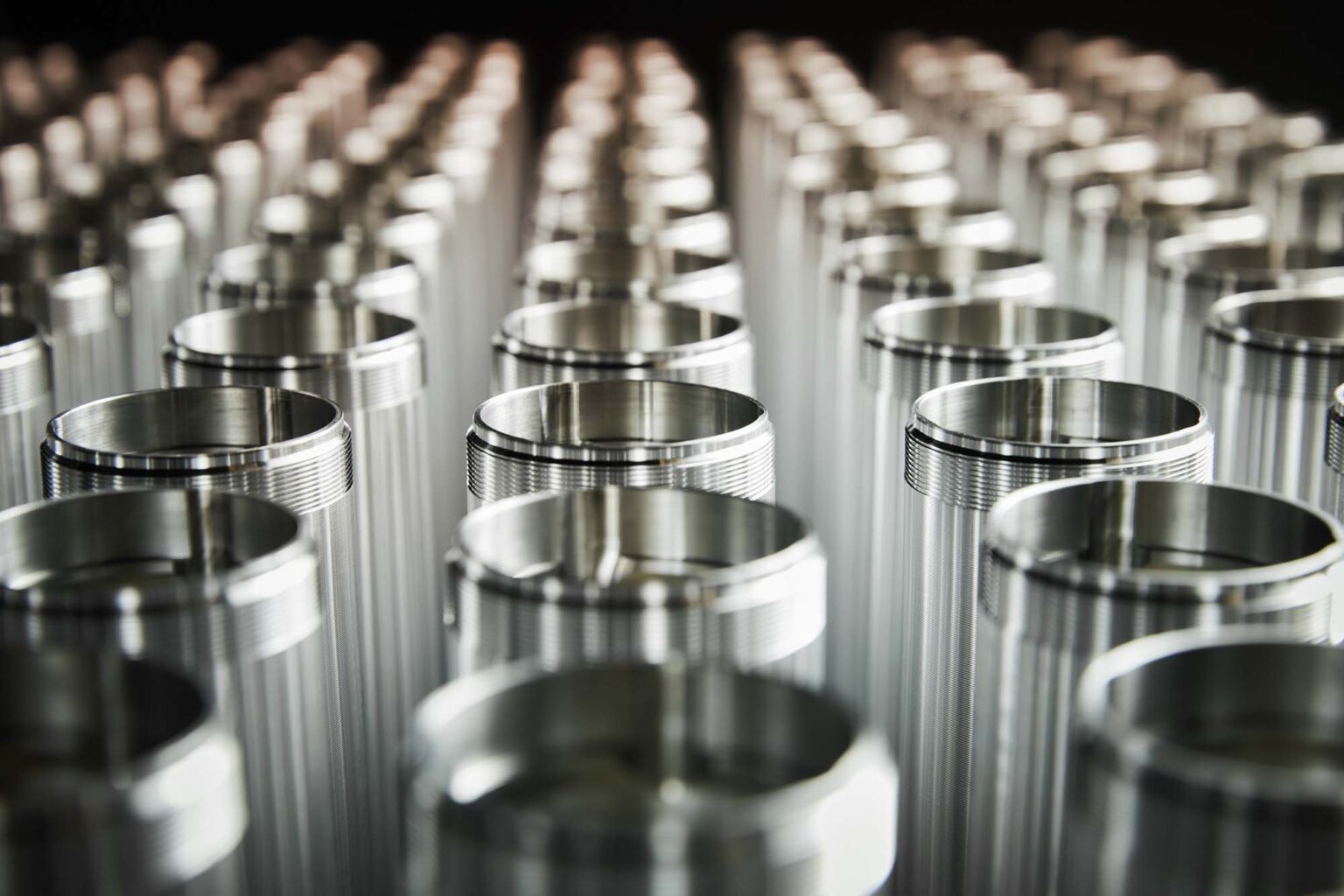
L’alliage d’aluminium qui convient le mieux à votre produit
Le bon alliage d’aluminium ou de magnésium pour votre profil de précision ; le produit final optimal commence par le bon choix de matériau.
Alliages d’aluminium et de magnésium
Les alliages d’aluminium et de magnésium sont des mélanges métalliques légers et résistants, largement utilisés dans l’aéronautique, l’industrie automobile et la construction en raison de leur haute résistance et de leur bonne résistance à la corrosion.
Mifa est spécialiste dans la production de profils d’extrusion de précision en aluminium et magnésium. Nous disposons de l’expertise et de l’expérience nécessaires pour sélectionner l’alliage adapté à chaque produit. Ainsi, nous fournissons des profils à divers secteurs, notamment l’industrie, l’aérospatiale, le secteur médical, la mobilité et la défense. Dans chaque marché, des propriétés telles que la résistance du matériau et la résistance à l’usure déterminent le choix de l’alliage d’aluminium approprié. Sur cette page, vous pouvez lire les caractéristiques de tous les alliages que nous proposons.
Facteurs importants dans le choix d’un alliage
Les alliages, composés de divers métaux et autres éléments, présentent différentes caractéristiques cruciales pour l’application finale. Il est donc très important que l’alliage d’aluminium ou de magnésium possède les propriétés adéquates, car ils résistent différemment aux températures extérieures, à l’humidité ou aux conditions chimiques. Les facteurs suivants jouent un rôle dans le choix de l’alliage approprié :
- Résistance à la chaleur
- Résistance à la corrosion
- Résistance mécanique
- Ductilité/élasticité
- Formabilité
- Soudabilité
Les avantages du co-engineering chez Mifa
Les ingénieurs de Mifa possèdent l’expertise et les connaissances nécessaires pour vous conseiller sur les différents types d’alliages d’aluminium et de magnésium, afin que nous puissions ensemble réaliser un produit optimal. De plus, nous combinons notre savoir-faire en alliages métalliques avec notre expertise en extrusion. Le co-engineering offre les avantages suivants :
Nous vous conseillons volontiers sur le choix de l’alliage approprié
Développement et phase de test plus rapides
Économies de coûts
Amélioration de la conception
Optimisation des processus
-
EN AW 1070
L’alliage 1070 est la seule variante de cette série que Mifa propose en standard. En raison de son excellente conductivité électrique, c’est un choix presque incontournable pour de nombreuses applications électroniques.
- Résistance : faible
- Formabilité : bonne à excellente
- Résistance à la corrosion : bonne
- Soudabilité : moyenne
- Qualité de surface : bonne
-
EN AW 3003
Grâce à l’ajout de manganèse, cet alliage est 20 % plus résistant que la série 1xxx. Il est principalement utilisé dans l’industrie automobile pour la fabrication de radiateurs.
- Résistance : moyenne
- Formabilité : excellente
- Résistance à la corrosion : bonne
- Soudabilité : bonne
- Qualité de surface : bonne
-
EN AW 6060
L’alliage d’aluminium 6060 est l’un des mélanges les plus utilisés lorsque la résistance n’est pas un facteur déterminant. Il présente une excellente formabilité, une très bonne finition de surface et convient à la plupart des traitements de surface. De plus, il est bien soudable. L’alliage 6060 peut en fait être utilisé partout, mais il est souvent employé lorsque le produit est visible, comme pour des éléments d’intérieur d’avions, des applications industrielles, etc.
- Résistance : moyenne
- Formabilité : bonne
- Résistance à la corrosion : bonne
- Soudabilité : bonne
- Qualité de surface : bonne
-
EN AW 6063
L’alliage d’aluminium 6063 est presque identique à l’alliage 6060 décrit précédemment, mais en raison d’une teneur plus élevée en magnésium, l’alliage 6063 présente de meilleures propriétés mécaniques que l’alliage 6060.
- Résistance : moyenne
- Formabilité : bonne
- Résistance à la corrosion : bonne
- Soudabilité : bonne
- Qualité de surface : bonne
-
EN AW 6005A
-
EN AW 6061
L’alliage 6061 est souvent utilisé aux États-Unis. Il possède d’excellentes propriétés mécaniques, mais présente une finition de surface légèrement inférieure et est plus difficile à extruder que d’autres variantes de la série 6xxx. Sa résistance est plus élevée que celle de nombreuses autres variantes 6xxx, se situant entre celle des alliages 6005 et 6082.
- Résistance : moyenne
- Formabilité : bonne
- Résistance à la corrosion : bonne
- Soudabilité : bonne
- Qualité de surface : moyenne
-
EN AW 6082
L’alliage 6082 possède d’excellentes propriétés mécaniques et est plus résistant que d’autres variantes de la série 6xxx. Cependant, en raison de la difficulté d’extrusion, il est peu utilisé pour les profils complexes.
- Résistance : moyenne à bonne
- Formabilité : bonne
- Résistance à la corrosion : bonne
- Soudabilité : bonne
- Qualité de surface : médiocre
-
EN AW 7020
En raison de sa haute résistance, l’alliage 7020 est largement utilisé dans l’industrie aérospatiale. Une caractéristique remarquable de l’alliage 7020 est la restauration de la résistance finale après soudage, atteignant environ 80 % de la résistance initiale. Aucune autre variante de cet alliage d’aluminium ne possède cette propriété.
Cela en fait un choix particulièrement fiable pour les pièces soudées devant conserver leur résistance, telles que les structures porteuses, les constructions et aussi les composants structurels dans les applications aéronautiques et spatiales. Par exemple, Mifa a déjà développé une pièce pour un dirigeable avec cette composition, où la pièce retrouve environ 80 % de sa résistance initiale après environ trois mois.
- Résistance : élevée
- Formabilité : moyenne à bonne
- Résistance à la corrosion : moyenne
- Soudabilité : bonne
- Qualité de surface : moyenne
-
EN AW 7022
L’aluminium 7022 est très adapté aux pièces soumises à de fortes contraintes grâce à ses hautes propriétés mécaniques et sa bonne résistance à la fatigue. Cet alliage dur est donc idéal pour les secteurs de l’aéronautique, de la défense et de l’espace.
- Résistance à l’usure : élevée
- Usinabilité : bonne
-
EN AW 7075
En raison de sa haute résistance, l’alliage d’aluminium EN AW 7075 est largement utilisé dans l’industrie aéronautique et spatiale. Il possède d’excellentes propriétés mécaniques et offre une bonne résistance à la fatigue métallique. C’est l’un des alliages d’aluminium les plus utilisés pour les constructions (fortement sollicitées). Cependant, en raison de la haute résistance du matériau, il n’est pas possible de fabriquer des profils creux avec l’alliage EN AW 7075.
- Résistance : très élevée
- Formabilité : bonne
- Résistance à la corrosion : moyenne
- Soudabilité : bonne
- Qualité de surface : moyenne
-
AZ31
L’alliage AZ31 contient un petit pourcentage d’aluminium, ce qui lui confère de meilleures propriétés mécaniques et une meilleure résistance à la corrosion.
- Résistance : élevée
- Formabilité : bonne
- Résistance à la corrosion : bonne (en combinaison avec un revêtement ou un traitement de surface approprié)
- Soudabilité : bonne
- Qualité de surface : moyenne
-
AZ61
L’alliage AZ61 présente des propriétés similaires à celles de l’AZ31, mais en raison de sa teneur plus élevée en aluminium, il offre une meilleure résistance à la corrosion et une résistance mécanique accrue. Cependant, en raison de sa haute résistance, il n’est pas possible de fabriquer des profils creux avec cet alliage.
- Résistance : très élevée
- Formabilité : moyenne à bonne
- Résistance à la corrosion : bonne (en combinaison avec un revêtement ou traitement de surface approprié)
- Soudabilité : bonne
- Qualité de surface : moyenne
-
6066
Cet alliage est utilisé pour l’extrusion dans les constructions soudées. Il contient une teneur significative en magnésium et silicium, et est formulé pour la mise en forme primaire de produits laminés.
- Résistance : bonne
- Formabilité : moyenne à faible, en raison de la haute résistance
- Résistance à la corrosion : excellente
- Soudabilité : bonne
- Qualité de surface : moyenne
-
6463
L’alliage 6463 ressemble à l’alliage 6063, mais offre la possibilité d’obtenir une excellente finition de surface avec des propriétés réfléchissantes. Le 6463 est très facile à extruder.
- Résistance : moyenne
- Formabilité : excellente
- Résistance à la corrosion : bonne
- Soudabilité : bonne
- Qualité de surface : bonne
-
6061 (20% SiC)
L’alliage 6061 est connu pour sa large gamme d’applications dans des industries telles que l’aéronautique, la construction, la marine, le sport, les loisirs et l’électronique. Cet alliage est difficile à extruder et présente des propriétés de surface limitées. Le 6061 est très utilisé aux États-Unis.
- Résistance : excellente
- Formabilité : bonne
- Résistance à la corrosion : bonne
- Soudabilité : bonne
- Qualité de surface : moyenne
-
Metal Matrix Composites (MMCs)
Les composites à matrice métallique (CMM) sont souvent constitués d’un métal à faible densité, comme l’aluminium ou le magnésium, renforcé par des particules ou des fibres d’un matériau céramique.
- Résistance : élevée
- Résistance à l’usure : bonne
-
Alliages aluminium-scandium
Ces alliages constituent un groupe d’alliages d’aluminium délibérément alliés au scandium afin d’améliorer leurs propriétés. Ils sont surtout connus pour leur capacité à offrir des améliorations significatives de la résistance à haute température, comparé aux alliages d’aluminium conventionnels.
- Résistance : excellente
- Ductilité : bonne
- Résistance à la corrosion : bonne
- Soudabilité : bonne
- Qualité de surface : bonne
Contactez-nous pour plus d’informations.
Alliages pour avions et aéronautique
Dans notre offre, nous proposons divers alliages pour des applications aéronautiques. Par exemple, les alliages aluminium 6061 et 7075 sont souvent choisis pour les profils extrudés en raison de leur excellente combinaison de résistance, de résistance à la corrosion et de maniabilité. L’aluminium 6061 est apprécié pour sa polyvalence dans les applications aérospatiales, tandis que l’aluminium 7075 excelle dans les applications nécessitant une résistance maximale.
De plus, les alliages 7020 et 7022 sont également très adaptés à l’aérospatiale et à l’aviation. L’aluminium 7020 se distingue par sa meilleure résistance à la corrosion et à la fatigue, tandis que l’aluminium 7022 est particulièrement adapté aux pièces devant supporter des charges élevées, grâce à ses excellentes propriétés mécaniques et sa bonne résistance à la fatigue.
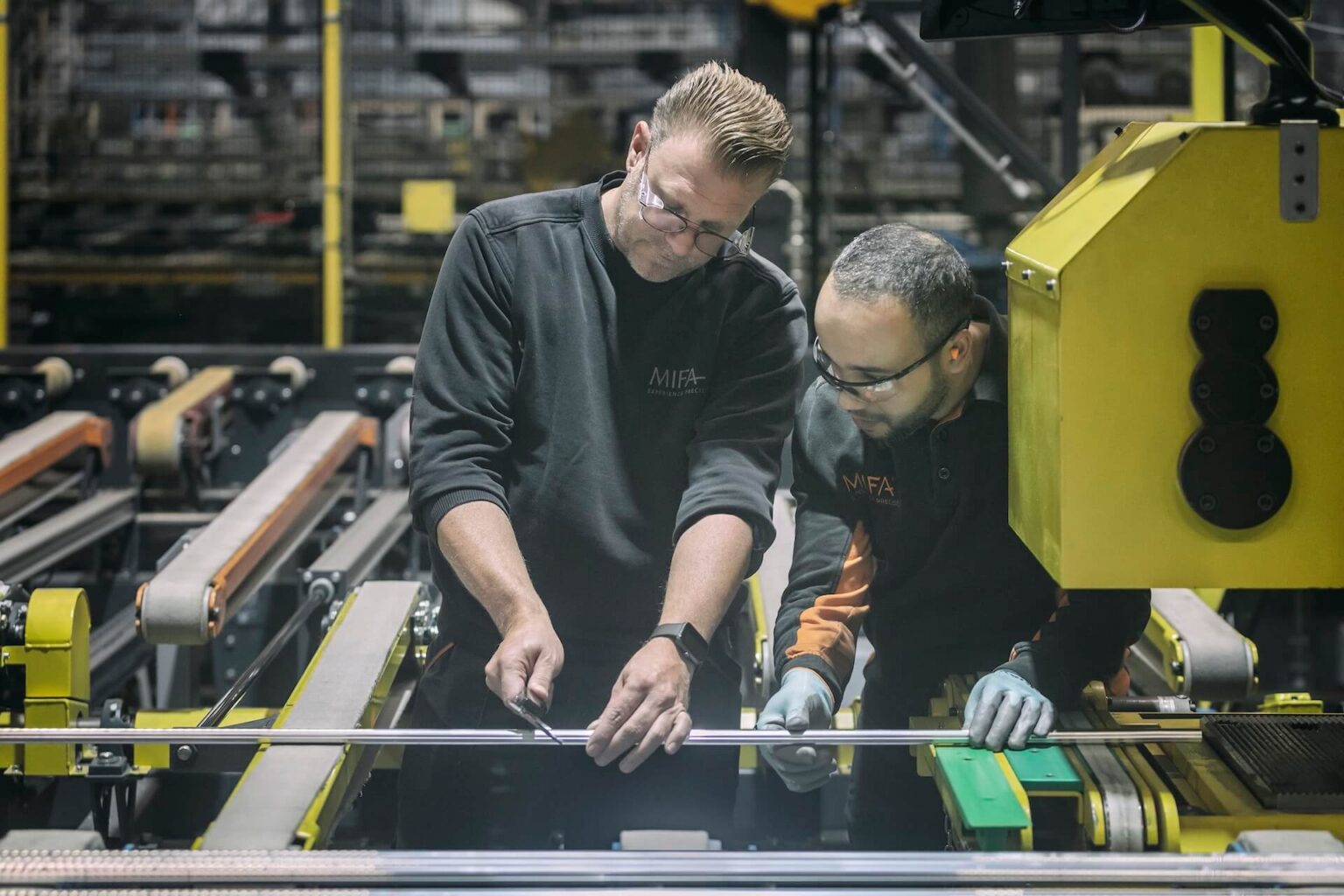
Traitements thermiques de l’aluminium
Pour améliorer certaines propriétés des alliages d’aluminium, des traitements thermiques sont appliqués. Cela peut viser à augmenter la résistance ou à améliorer la formabilité.
Les propriétés modifiées de l’aluminium dépendent de la température, de l’intensité du processus, de l’alliage et de la durée du traitement. Lors d’un traitement thermique de l’aluminium, le profil est renforcé par précipitation des éléments d’alliage. Ce processus diffère fortement du durcissement de l’acier. Les traitements thermiques sont possibles avec les séries 2xxx, 6xxx et 7xxx.
Les traitements thermiques sont basés sur la condition T. Le T signifie « tempered » (trempé), suivi d’un chiffre entre 1 et 10 qui détermine le traitement de base. Des chiffres additionnels précisent les spécifications supplémentaires.
Plusieurs traitements sont possibles, notamment :
- Résistance maximale (peak strength)
- Vieillissement naturel (formabilité améliorée)
- Survieillissement (résistance à la corrosion améliorée)
Les duretés couramment rencontrées sont :
- T5/T6 : trempe en solution, trempage, vieillissement artificiel
- T4 : trempe en solution, trempage, vieillissement naturel
- T7 : trempe en solution (four), trempage, survieillissement. Applicable uniquement à l’alliage T7 7075
- 0 : recuit. Seulement trempe en solution ou vieillissement
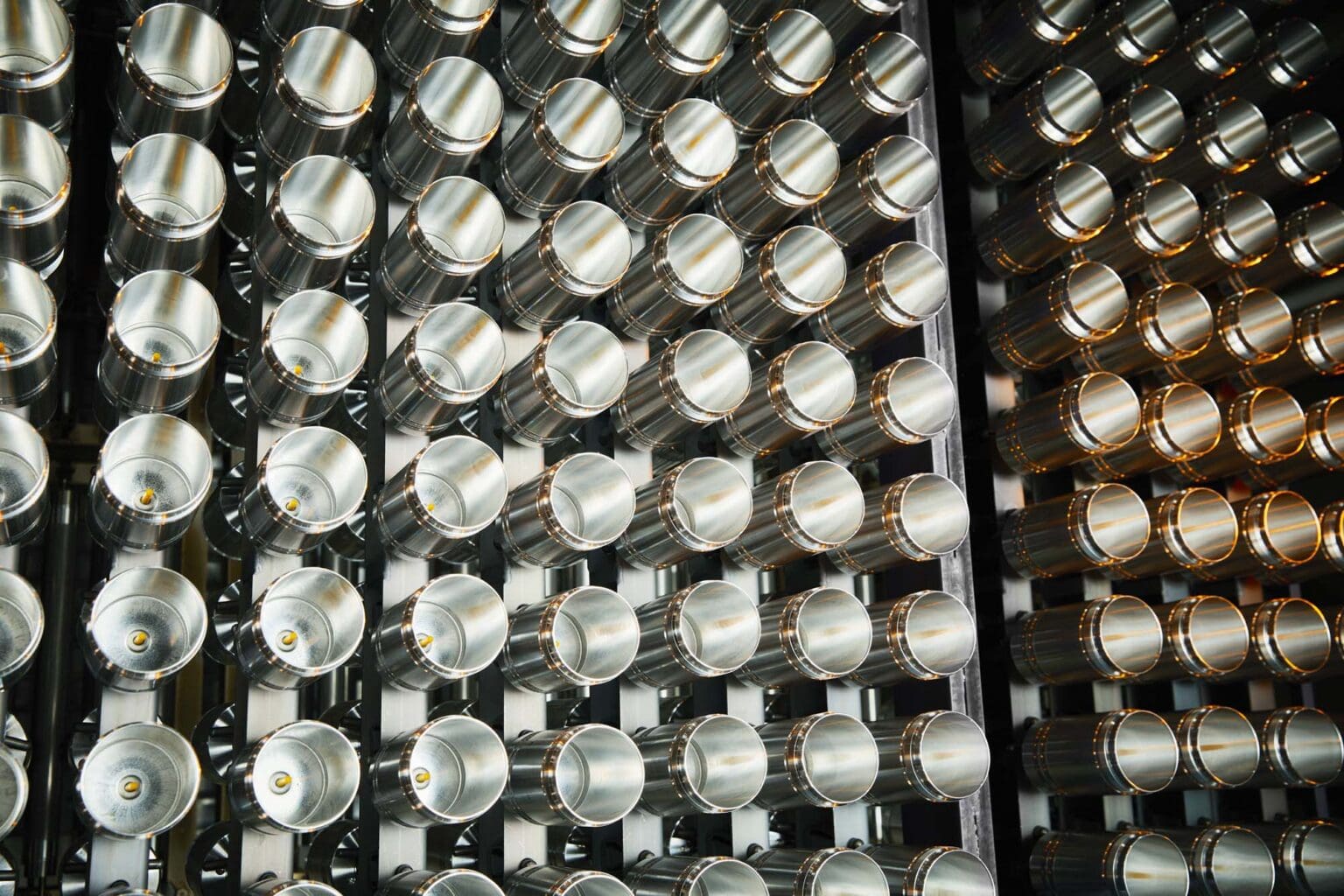
Traitement de surface selon l’alliage métallique
Le choix du bon alliage joue un rôle important dans l’obtention d’un profil extrudé de qualité. De plus, les traitements de surface peuvent encore améliorer la qualité du produit final.
En plus de l’extrusion de précision, Mifa est spécialisée dans les traitements de surface. Cela signifie que nous pouvons gérer l’ensemble du processus de fabrication en interne. Nous constatons ainsi que les profils en aluminium sur mesure sont souvent soumis à un traitement de surface afin d’améliorer ou de supprimer certaines propriétés du produit, comme la résistance à la corrosion. Le bon traitement est crucial pour l’application prévue.
Chez Mifa, nous proposons trois types de traitements de surface :
- Anodisation (dont GLISSCOAT®, HART-COAT®, anodisation technique)
- Passivation
- Couches polymères (dont Tufram®, Lectrofluor, Nedox)
Nous calculons les émissions de CO2 de votre profil extrudé
Le choix d’un alliage d’aluminium peut avoir une influence considérable sur la durabilité d’un produit, tant en termes d’impact environnemental que de durée de vie du produit lui-même. Voici quelques aspects à considérer :
- Recyclabilité : l’aluminium est l’un des matériaux les plus recyclés au monde. Certains alliages sont plus recyclables que d’autres, ce qui signifie qu’ils nécessitent moins d’énergie grâce au réemploi.
- Résistance à la corrosion : la durabilité du profil ou produit en aluminium dépend fortement de l’alliage en ce qui concerne la résistance à la corrosion, ce qui impacte aussi la durée de vie du produit.
- Consommation d’énergie et émissions de CO2 pendant la production : l’alliage choisi peut influencer la consommation d’énergie lors de la fabrication de l’aluminium.
- Les alliages sont souvent choisis en fonction de leurs propriétés, notamment le poids, ce qui a également un impact direct sur la consommation d’énergie et les émissions de CO2.
Nos ingénieurs sont à votre disposition pour vous aider à choisir le bon alliage. Ils peuvent également, sur la base de cet alliage, calculer l’empreinte carbone pour la production d’un profil extrudé en aluminium et conseiller, par exemple, sur l’épaisseur des parois grâce à notre outil LCA personnalisé.
-
Quelles sont les propriétés de l’aluminium ?
L’aluminium est connu pour sa légèreté, sa solidité et sa résistance à la corrosion. Il est aussi très malléable et un excellent conducteur de chaleur et d’électricité. Ces propriétés le rendent idéal pour les applications techniques, en particulier lorsque la précision et l’efficacité sont essentielles.
-
Les alliages d’aluminium sont-ils résistants à la corrosion ?
Oui, mais cela dépend de l’alliage et du traitement de finition. L’aluminium brut forme naturellement une couche d’oxyde, mais pour des applications exigeantes, nous utilisons des traitements supplémentaires comme l’anodisation ou la passivation pour offrir une protection maximale.
-
Les alliages de magnésium sont-ils plus résistants que l’aluminium ?
Le magnésium est plus léger que l’aluminium, mais généralement moins résistant et moins anticorrosion. C’est pourquoi, dans des applications où la solidité structurelle et la durabilité à long terme sont essentielles – comme dans l’aéronautique ou l’ingénierie de précision – les alliages d’aluminium sont généralement préférés.
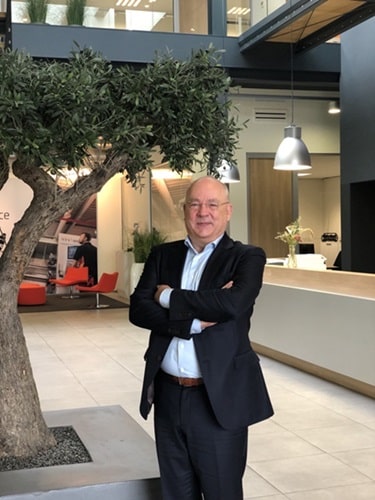
Contactez-nous
Appelez ou envoyez un e-mail Frank
Business Development Manager